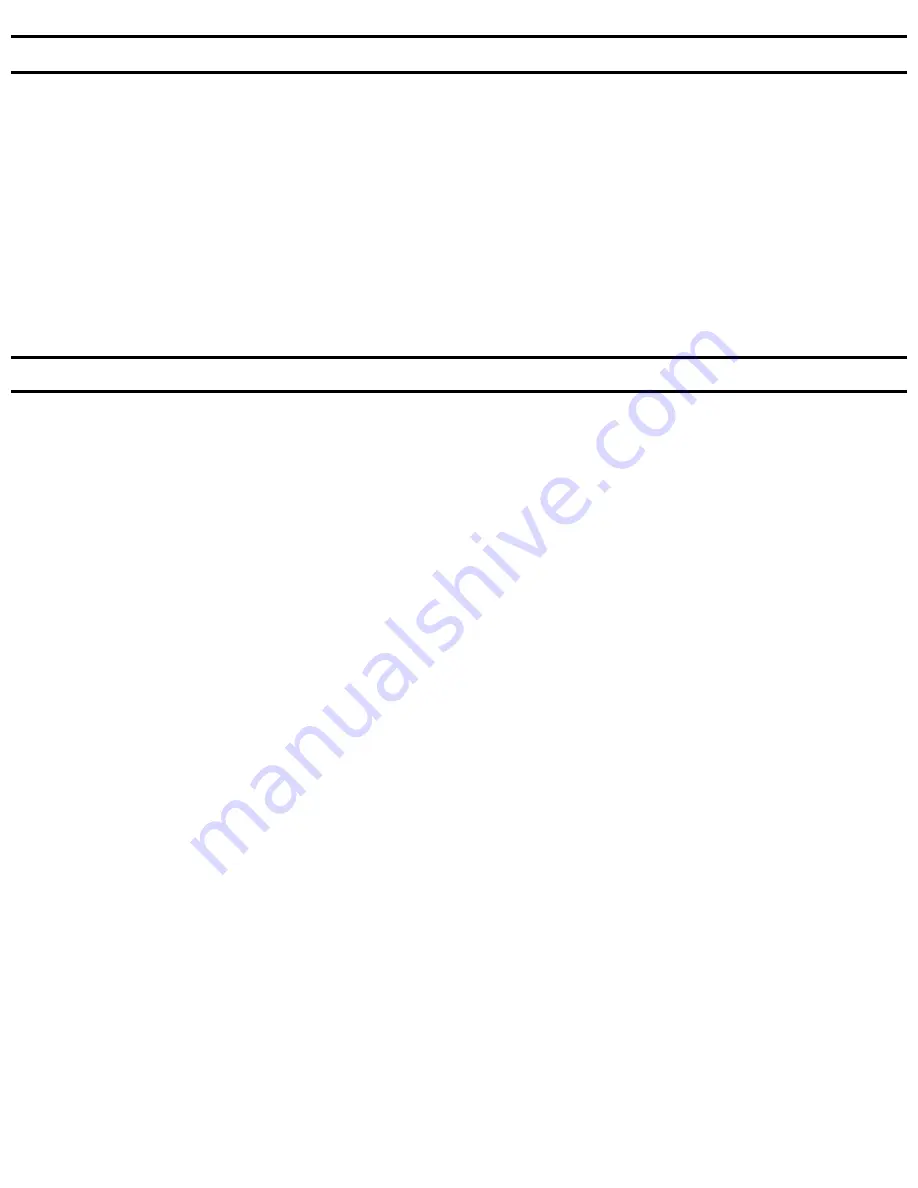
Shut down procedure
1. Turn off the power switch on the pressure washer.
2. Relieve pressure on line by pulling trigger gun.
3. Shut off water supply and disconnect garden hose.
4. Be sure to check for water leaks or oil leaks that should be repaired before the next operation.
5. If you are going to store the machine for extended period of times in cold climates be sure to anti-
freeze the equipment. A 50% anti-freeze solution may be drawn in through the inlet of the pump
using a short remnant of garden hose. This fluid should be run through the pump when the fluid is
discharged from the pump discharge your machine is winterized.
Do not allow machine to freeze.
The pump oil should be changed after the first 50 hours of operation, then every year for average ser-
vice or more frequently for extensive use or hostile environments {dusty or high moisture}
Water filters, hoses and fittings should be checked prior to every operation for cleanliness, leaks and
repair needs. Repair or replace as needed.
Storage
Pump
Filters
Low
Nozzle
Pressure
Surging
Operation
Soap
Injector
Not
Working
Properly
Notice
Troubleshooting - Common Problems and Solutions
Low nozzle pressure is a common complaint. In a majority of instances, low nozzle pressure is general-
ly caused by one of the following:
1. Plugged nozzle tip.
2. Inlet screen plugged.
3. Insufficient flow in gallons per minute (not pressure) to the pump.
4. Unloader valve stuck open due to debris lodged under the check valve ball.
5. Customer use of shut-off-type quick connectors.
6. Plugged hose.
7. Incorrect nozzle or soap tip installed.
Another complaint is that pressure
surges.
That is, when the trigger is pulled, pressure is satisfactory for
a moment then falls off. When the trigger is released, pressure builds up to normal levels. This is gen-
erally a sign that the water supply cannot provide the flow rate (gallons per minute) required by the
pump. Following are some possible solutions:
1. Make sure the supply is not restricted; that there are no under-sized fittings and the inlet screen is
unobstructed.
2. Make sure the flow rate of the water supply is sufficient for the pump. First, find the capacity of your
pump in gallons per minute (gpm) as shown in the
Water Supply section on Page 5
. Then determine
the flow rate of your supply by measuring the gallons that can be delivered in one minute. If your
supply does not deliver the gpm your pump requires, do
not
use the pump. It will suck air, causing
cavitation that can quickly damage pump components.
3. Check for leaks in the supply fittings. Any leak will cause the pump to draw air and perform poorly.
When a soap injector is not working properly, the problem is generally fairly easy to isolate. Check the
following:
1. Make sure the Black, soap tip is installed. Soap injectors will
not
work when high pressure nozzles
are installed.
2. Be sure that the soap injector valve is turned on, and turn selector valve to desired setting.
3. A piece of debris may be caught in the injector valve, injector ball valve, or orifice. Disassemble
and clean the injector.
User maintenance procedures include replacing valves and seal. Unloader components are
not
user
serviceable. Repairs involving unloaders and crankcase components should be referred to the factory or
a factory authorized repair center.