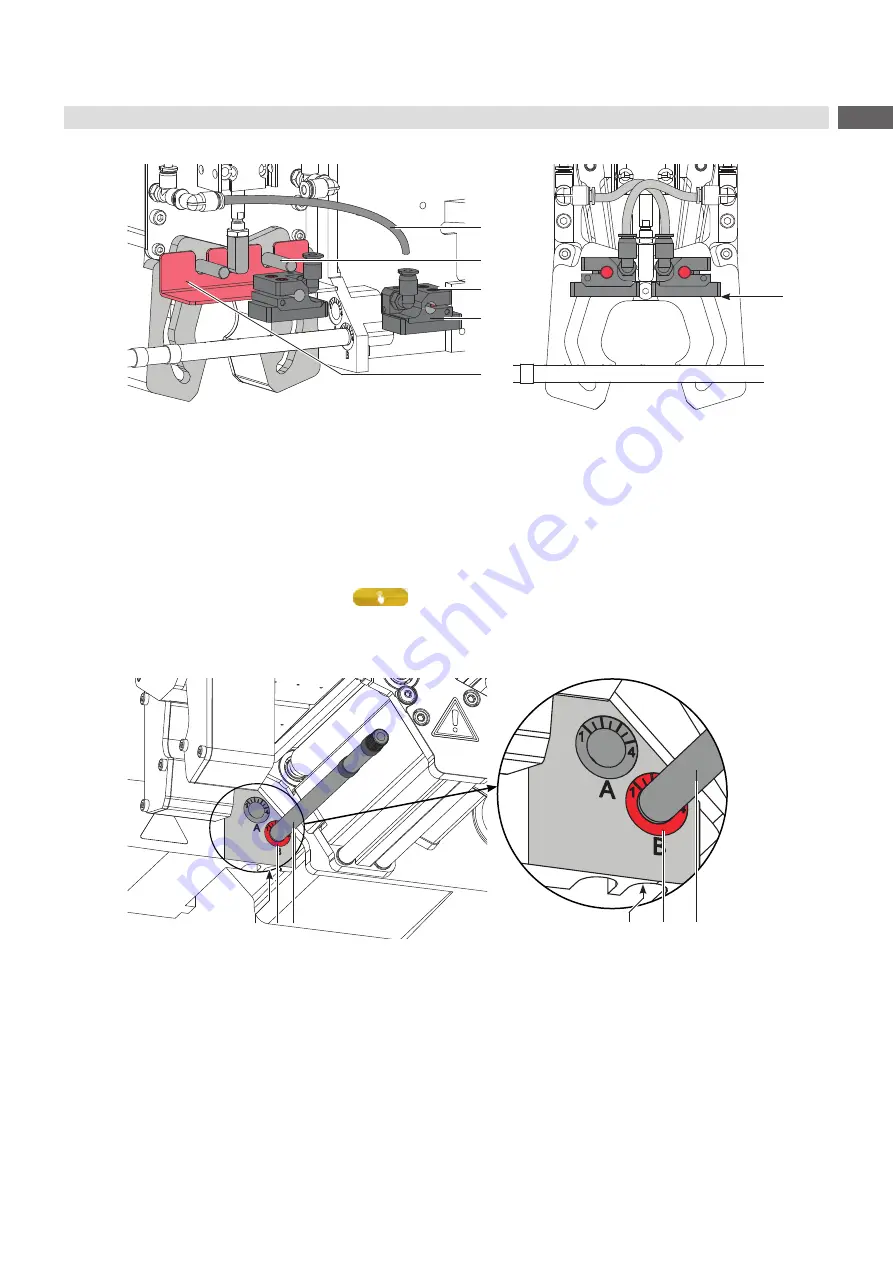
15
3.9
Mounting the Suction Pads
4
1
2
5
3
6
Fig. 10
Mounting the suction pads
1. Loosen screws (3).
2. Use the adjusting tool (6) included (cab serial No.: 5972857) as shown in the picture to adjust the suction plates.
3. Slide each suction plate (4) over the corresponding driving pin (2) to the adjusting tool (6).
Mount the suction plates (4) so that the L connectors (hose connections) are accessible from the front.
4. Tighten screws (3).
5. Remove adjustment tool (6) downwards.
The lower surfaces must now be aligned at an angle of 0 ° and at a height to each other.
6. By repeatedly pressing the button
, the motion sequence of the applicator is run through.
Then check the alignment of the tamps and adjust if necessary.
3.10
Mounting the Blow Tube
1
2 3
1
2
3
Fig. 11
Mounting the blow tube
The blow tube (3) can be rotated around its axis. By this principle the direction of the compressed air can be
optimized.
1. Loosen the screw (1).
2. Insert the blow tube (3) as far as possible into the provided slot B (2).
3. Tighten the screw (1) to ensure the blow tube stays in place.