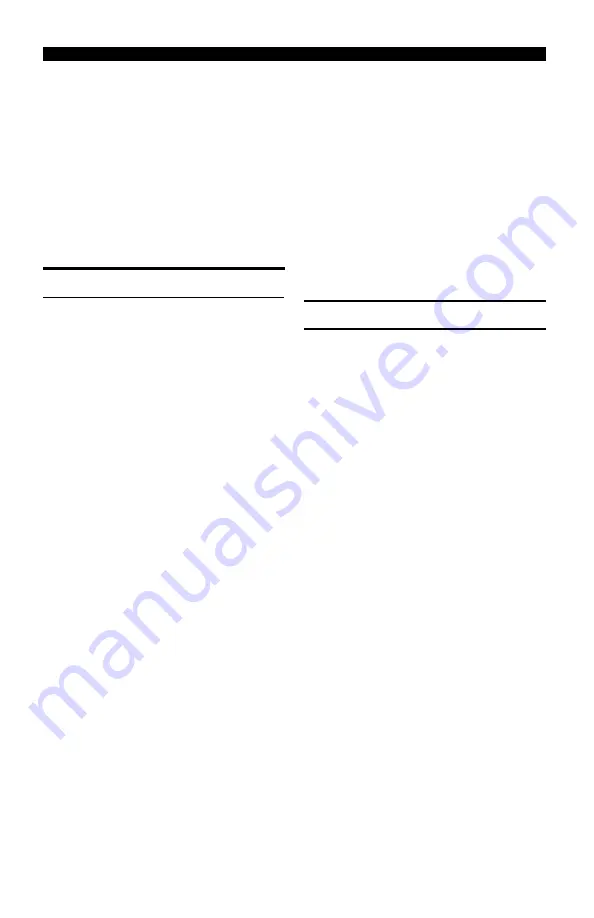
M A I N TAINING THE FREE-AIR PUMP
FOR THE PUMP TO OPERATE AT ITS OPTIMUM PERFORMANCE
LEVEL, THE FOLLOWING ROUTINE MAINTENANCE PROCEDURES
MUST BE PERFORMED.
FOR THE SPECIFIC LOCATION OF THE
PUMP COMPONENTS REFERRED TO
BELOW, SEE THE LIST OF PUMP COMPO-
NENTS ON PAGE 4.
Maintaining The Air Motor
The air motor is a rotary 4-vane type. The
vanes require no adjustment and will last
5,000-15,000 hours if properly maintained.
1. Maintain INLET AIR PRESSURE
R E G U L ATOR FILTER (15):
- It is equipped with a 40-micron filter ele-
ment that can plug up if air supply is not
prefiltered at the compressor.
- Remove and clean filter periodically to
prevent clogging.
2. Maintain LUBRICATOR (12):
- Keep filled with SAE 10 Automotive oil.
(Do not use a heavier grade)
- Maintain drip rate at approximately 1 per
minute.
- DO NOT fill while running or while under
pressure.
3. Flush MOTOR (9):
If motor is sluggish or inefficient, flush with
LOCTITE Safety Solvent, or any non-toxic,
nonflammable industrial cleaning solvent).
Use the following directions to flush the
motor:
a. Shut-off the pressure into the air motor
and disconnect the airline from the Drive
Air Inlet (16).
b. Locate the pump in a safe area. Solvent
will spray from the exhaust port during
flushing. Protect your face and eyes
from the spray.
c. Remove the Plug (11) and pour several
teaspoons of solvent into the opening.
d. Replace the Plug, reconnect the airline
back to the Drive Air Inlet. Turn the pres-
sure back on.
e. Run the pump at a very low speed (10-
20 RPM) for approximately 1 minute or
until all the solvent is flushed.
NOTE: Motor bearings are grease
packed and sealed. They require no
maintenance.
Maintaining The Pump
Pump is rotary 4 vane type. The vanes take
require no adjustment and will last 5,000 to
10,000 hours if properly maintained.
1. Maintain FILTERS
- Dirty filters restrict outlet air flow and can
cause the motor to overload or cause
premature pump failure.
- Replace CARBOFINE OUTLET FILTER
CARTRIDGE (6) at least once every 200
running hours (Catalog No. S17101).
- Replace INLET FILTER (1) at least once
every 500 running hours to maintain
proper pressure and full air flow. To
check the filter - while running the pump,
momentarily remove the FILTER (1) from
the Inlet PIPE (2). If the motor speeds up
or the outlet pressure shown on GAUGE
(5) increases, the filter needs replace-
ment.
2. Flush PUMP if necessary
Should dirt, foreign particles, moisture or
oil be permitted to enter, the vanes will
become sluggish, resulting in a lowering of
outlet air pressure. Flush the pump with
LOCTITE Safety Solvent. (DO NOT USE
KEROSENE).
Pump should be operated for at least a few
minutes every one to two weeks to reduce
the likelihood of rust film forming in the
rotor.
If pump remains idle in humid environment
for some time, FLUSHING may be required
to remove rust film in chamber and rotor
slots.
11