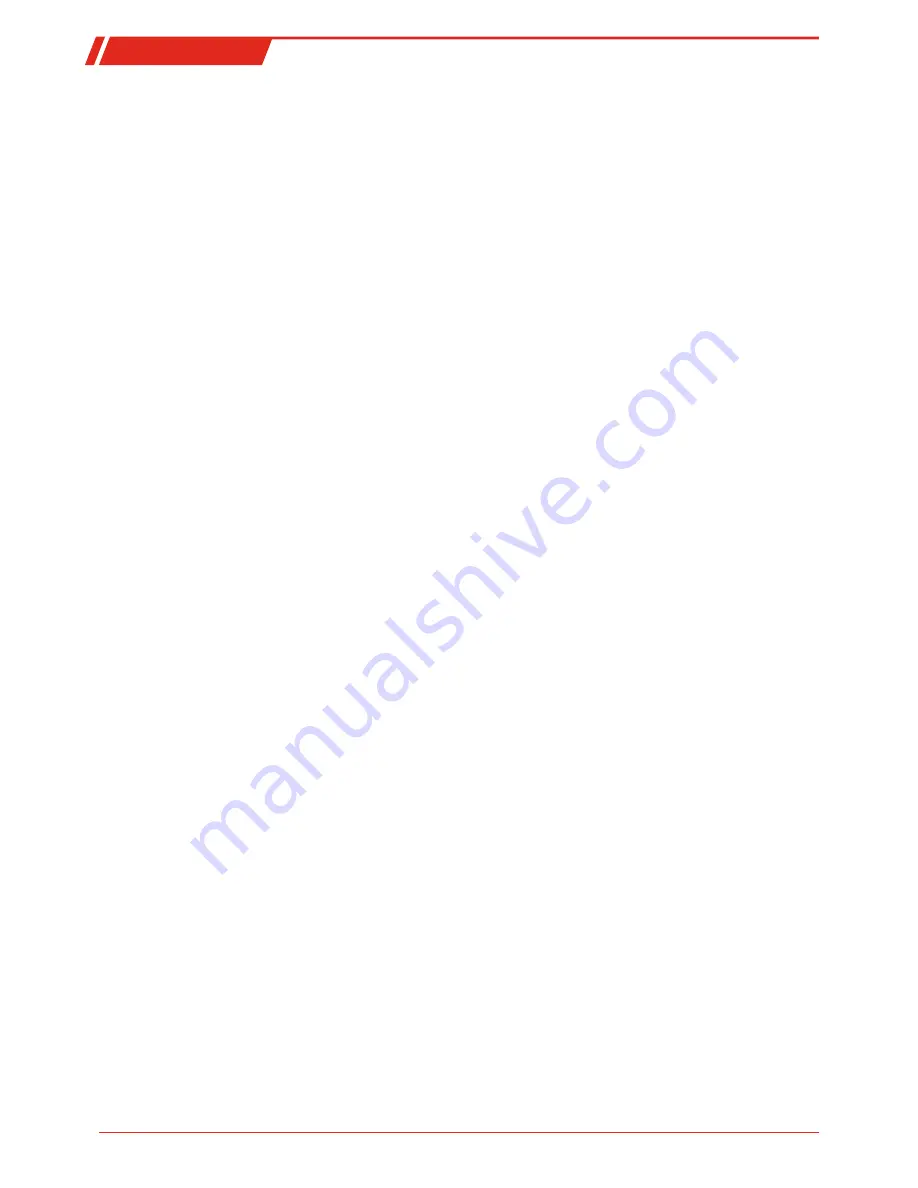
BA 4000 Inj.
5.1.3 Calibration for BA 4000 Inj. KV
The unit should be on for approx. 30 min. before calibrating it so all components are at operating temperature. The puncture
device should be removed from the gas inlet during calibration.
Setting the zero point with zero gas
Disconnect the connection hose to the vacuum pump. Switch on the pump/valve switch (1), which will open the solenoid valve.
– Connect a hose to the gas inlet. Connect the test gas cylinder and set the pressure regulator on the cylinder to max. 0.1 bar
overpressure.
Use the same anaerobic gas (N
2
or CO
2
) as the zero gas used to gas the packaging to be tested. Set the toggle switch at the
back of the unit to the corresponding setting.
– Slowly open the valve on the pressure regulator. If the reading on the analyser’s gauge fluctuates, reduce the pressure with
the pressure regulator.
– If the reading is steady, set the pump/valve switch to 0, which will close the solenoid valve. Disconnect the hose (calibration
with stagnant gas).
– Use the zero potentiometer to set to 0.0 %.
Adjusting the zero point via pressure gauge (optional)
With an optional pressure gauge (BA 4000 Inj. KV/D), the zero point calibration requires no zero gas. The toggle switch at the
back of the unit must be in the position corresponding with the filling gas for the packaging.
– Attach the connection hose to the vacuum pump. Switch off the pump/valve switch, which will close the solenoid valve.
– Switch on the mbar/O
2
switch. The display will show the pressure.
– Switch on the vacuum pump.
– Once the required vacuum has been created, switch off the mbar / O
2
switch. The O
2
concentration will appear.
– Use the zero potentiometer to set to 0.0 %.
Adjusting the range (sensitivity)
– Attach the connection hose to the vacuum pump. Switch on the pump/valve switch (1), which will open the solenoid valve.
– Switch on the vacuum pump, air or the span gas will be drawn in.
– Once the reading is steady, switch off the pump/valve switch, which will close the solenoid valve (calibration with stagnant
gas).
– If necessary, set the "Span" potentiometer via the front panel on the unit so the value matches the span gas (e.g. 20.9 Vol.%
for air).
5.1.4 Carrier gas influence (cross-sensitivity)
The selectivity of the unit’s measuring method is based on the extreme magnetic susceptibility (measured variable for magnet-
isation) of oxygen. The magnetic susceptibility of other gases is typically so low that its influence on the measurement can be
vastly disregarded.
Significant measuring errors only occur when e.g. using nitrogen as the zero gas for calibration, but using CO
2
as the sample gas
(filling gas for the packaging) . The unit will then show a value, even if the sample gas contains no oxygen, i.e. it is cross-sensitive
to the other gas component. In this case, recalibrate with the toggle switch at the back of the unit in the correct position. If the
measurement is still incorrect, please contact Service for assistance.
5.2 Notes on operating the BA 4000 Inj. KV/D with pressure gauge (optional)
Use the mbar/O
2
switch to toggle between displaying the pressure and concentration. The pressure is displayed in mbar, the
concentration in Vol.%. So in addition to the concentration, the internal pressure for the packaging can also be displayed.
10
Bühler Technologies GmbH
BE550004 ◦ 07/2016-2
Содержание 55 11 399
Страница 21: ......