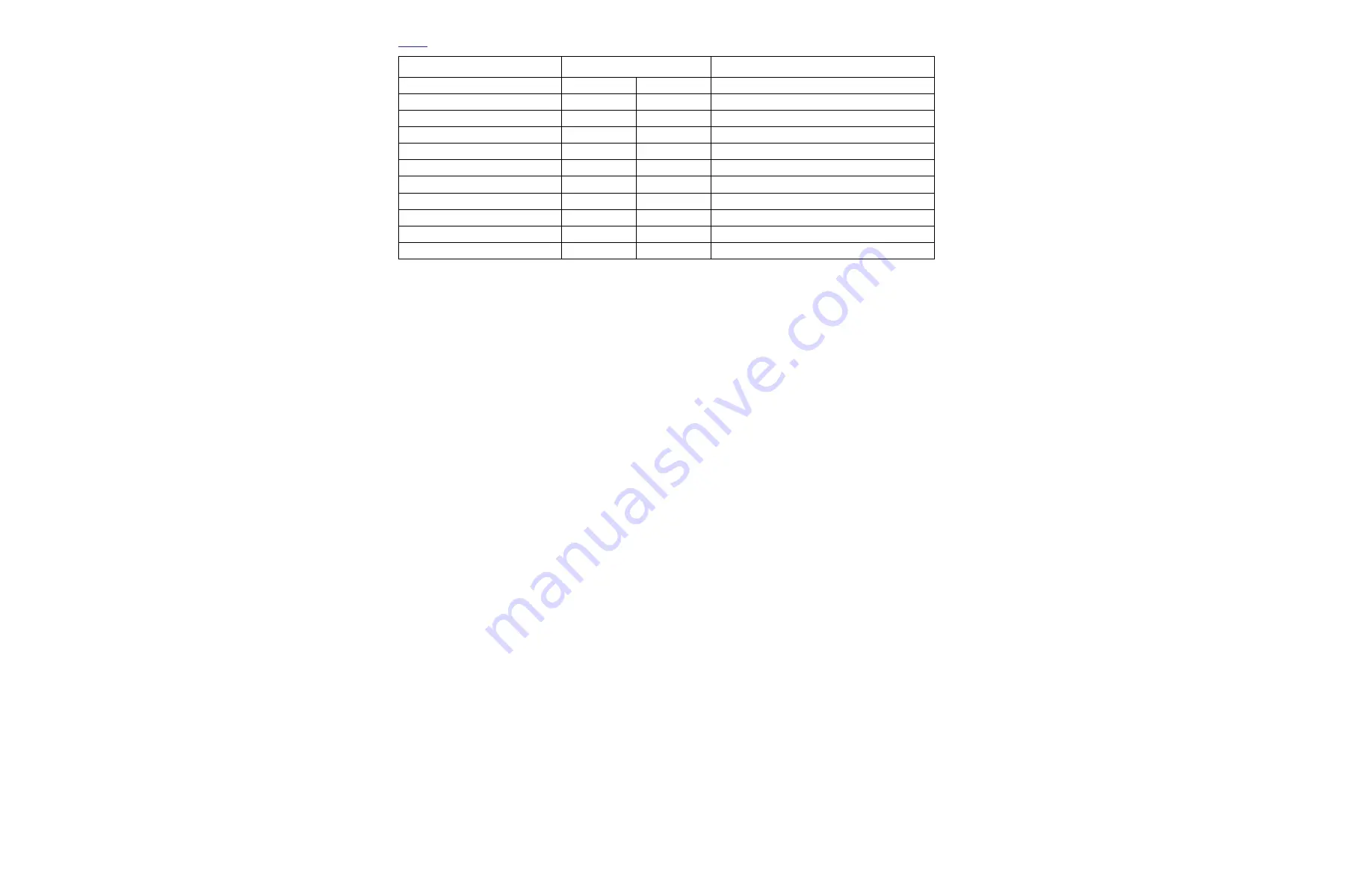
2-4
2004 Buell Firebolt: Chassis
38-42 ft-lbs
52-57 Nm
page 2-52
17-19 ft-lbs
23-26 Nm
LOCTITE 272 (red), page 2-52
Swingarm brace mounting fasteners
25-27 ft-lbs
34-37 Nm
page 2-58
24-26 ft-lbs
32-35 Nm
page 2-58
Switch housing fasteners, right
25-33
in-lbs
3-4 Nm
page 2-63
36-48
in-lbs
4-5 Nm
page 2-86
12-36
in-lbs
1-4 Nm
page 2-86
21-23 ft-lbs
28-31 Nm
LOCTITE 272 (red), page 2-85
40-45 ft-lbs
54-61 Nm
page 2-73
40-44
in-lbs
4-5 Nm
page 2-21
36-48
in-lbs
4.1-5.4 m
page 2-74
ITEM
TORQUE
NOTES
Содержание Firebolt XB12R 2004
Страница 52: ...2 52 2004 Buell Firebolt Chassis HOME NOTES ...