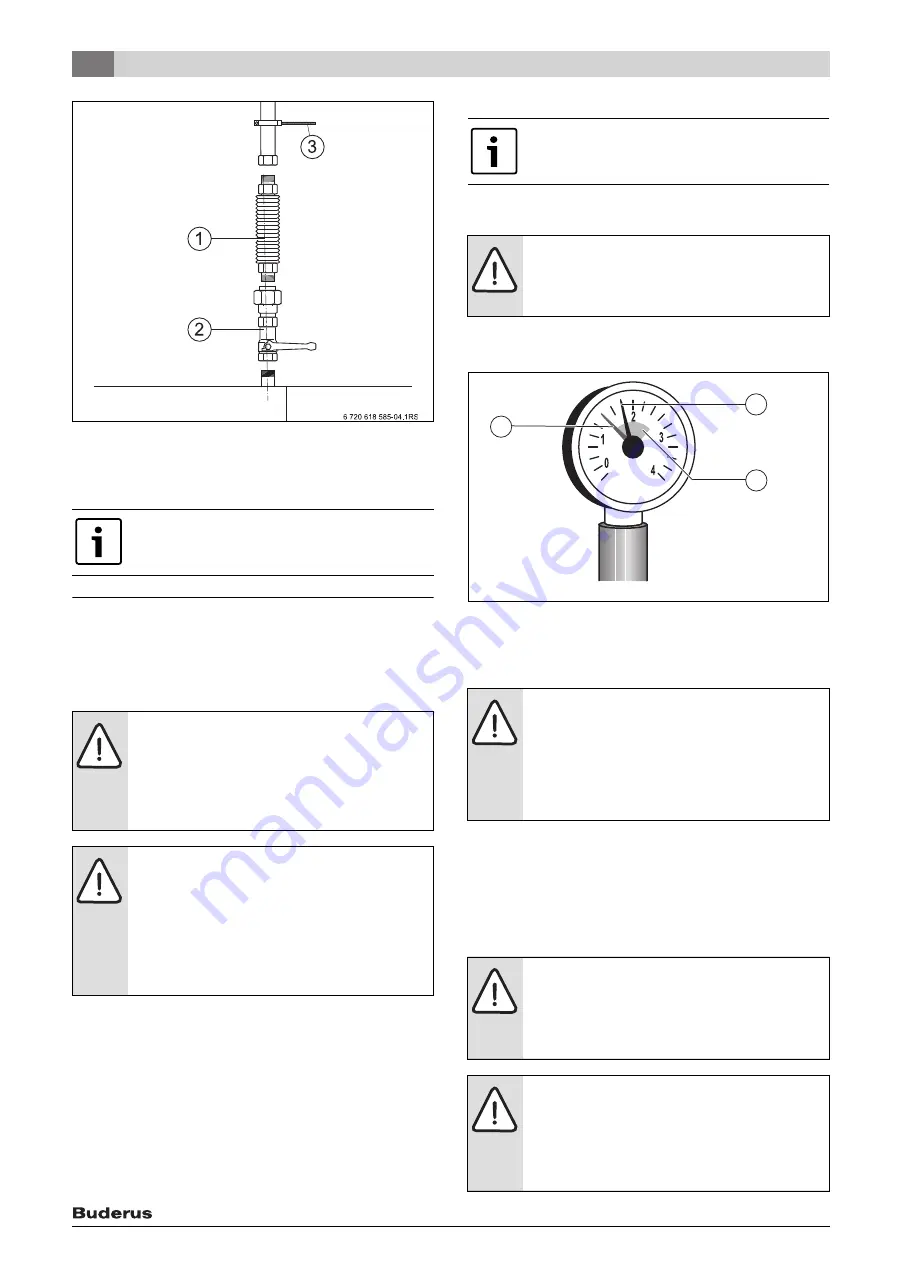
7
Start up the heating system
Logano plus GB402 – 6 720 820 700 (2018/01)
24
Fig. 25 Gas connection
[1]
Expansion joint
[2]
Gas tap (here with thermally activated shut-off equipment)
[3]
Flue bracket
7
Start up the heating system
This chapter describes commissioning using the standard control unit
module.
▶ After completing the work described below, complete the
commissioning report (
▶ Never operate the boiler when there is a lot of dust, e.g. due to
building work. Never install air filters in the inlet path if there is a high
dust load. Convert the boiler to balanced flue operation if the dust
loads are excessive.
▶ Burners contaminated during building work must be cleaned before
commissioning.
▶ Inspect flue and combustion air pipework (with balanced flue
operation) and the apertures for combustion air supply and
ventilation (
7.1
Checking the operating pressure
▶ Prior to commissioning, check the operating pressure of the heating
system on the water side and adjust if required.
▶ Set the red needle [1] of the pressure gauge to the required
operating pressure of at least
1 bar
.
Fig. 26 Pressure gauge for sealed systems
[1]
Red needle
[2]
Pressure gauge needle
[3]
Green marking
▶ Top up heating water or drain off water via the on-site drain & fill valve
until the required operating pressure has been reached.
▶ During filling, vent the heating system via the radiator bleed valves.
7.2
Checking for leaks
Prior to commissioning, check all new line sections on the gas side for
external gas tightness.
For higher gas supply pressures than shown in table 12,
(
page 28), Buderus offers additional gas pressure
regulators as accessories.
NOTICE:
Boiler damage through excessive dust and dirt
contamination in open flue mode!
Strong dust and dirt contamination can occur, for
example, due to building work in the installation room.
▶ During building work, operate the boiler in balanced
flue mode.
NOTICE:
Risk of boiler damage through contaminated
combustion air!
▶ Never use chlorinated cleaning agents or
halogenated hydrocarbons (as contained in spray
cans, solvents, cleaning agents, paints and
adhesives, for example).
▶ Never store or use such substances in the installation
room.
This boiler cannot be operated with open vented heating
systems.
NOTICE:
System damage through boiler scaling!
▶ Observe the water quality requirements in
accordance with the "Water Quality Operators Log"
and enter the volume and quality of the fill water.
CAUTION:
Health risk through contaminated drinking
water!
▶ Always observe the regulations and standards
applicable in your jurisdiction for the prevention of
contamination of drinking water (e.g. by water from
heating systems).
▶ In Europe, observe standard EN 1717.
DANGER:
Risk of explosion!
There is a risk of explosion if gas lines and gas
connections leak.
▶ Carry out an appropriate tightness test with a
foaming agent.
DANGER:
Risk of system damage due to short circuit!
▶ Cover the areas at risk before performing a tightness
test, e.g. the internal water pressure sensor and the
return sensor on the boiler return.
▶ Never spray or let leak detection agent drip onto
cable entries, plugs or electrical cables/leads.
6 720 615 876-59.2T
3
2
1
Содержание GB402-320-5
Страница 62: ...Logano plus GB402 6 720 820 700 2018 01 62 Notes...
Страница 63: ...Logano plus GB402 6 720 820 700 2018 01 63 Notes...
Страница 64: ......