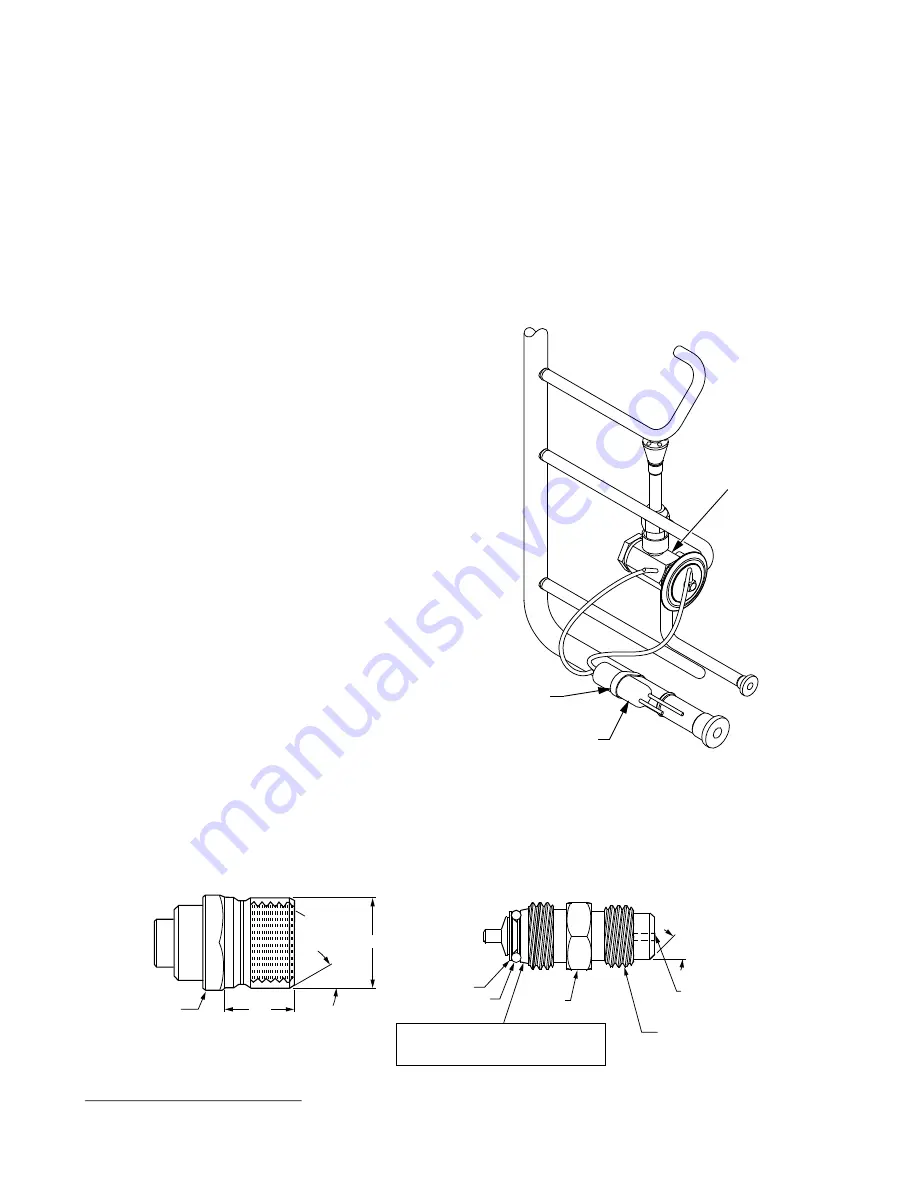
13
closes the pin. The refrigerant flow is effectively stabilized
to the load demand with negligible change in superheat.
Replacing TXV
1. Recover refrigerant.
2. Remove TXV support clamp using a
5
/
l6
-in. nut driver.
3. Remove TXV using a wrench and an additional wrench on
connections to prevent damage to tubing.
4. Remove equalizer tube from suction line of coil. Use file
or tubing cutter to cut brazed equalizer line approximately
2 inches above suction tube.
5. Remove bulb from vapor tube inside cabinet.
6. Install the new TXV using a wrench and an additional
wrench on connections to prevent damage to tubing while
attaching TXV to distributor.
7. Attach the equalizer tube to the suction line. If the coil has
a mechanical connection, then use a wrench and an addi
-
tional wrench on connections to prevent damage. If the
coil has a brazed connection, use a file or a tubing cutter to
remove the mechanical flare nut from the equalizer line.
Then use a new coupling to braze the equalizer line to the
stub (previous equalizer line) in suction line.
8. Attach TXV bulb in the same location where the original
(in the sensing bulb indent) was when it was removed,
using the supplied bulb clamps. See Fig. 20.
9. Route equalizer tube through suction connection opening
(large hole) in fitting panel and install fitting panel in place.
10. Sweat the inlet of TXV marked “IN” to the liquid line. Avoid
excessive heat which could damage the TXV valve. Use
quenching cloth when applying heat anywhere on TXV.
Refrigerant System Pressure Access Ports
There are two access ports in the system: on the suction tube near
the compressor and on the discharge tube near the compressor.
These are brass fittings with black plastic caps. The hose connec
-
tion fittings are standard
1
/
4
-in. SAE male flare couplings.
The brass fittings are two-piece high flow valves, with a recep
-
tacle base brazed to the tubing and an integral spring-closed
check valve core screwed into the base. See Fig. 21. This check
valve is permanently assembled into this core body and cannot
be serviced separately; replace the entire core body if neces
-
sary. Service tools are available from RCD that allow the re
-
placement of the check valve core without having to recover
the entire system refrigerant charge. Apply compressor refrig
-
erant oil to the check valve core’s bottom o-ring. Install the
fitting body with 96 ± 10 in.-lb (10.85 ± 1.1 Nm) of torque; do
not over-tighten.
PURON (R-410A) REFRIGERANT
This unit is designed for use with Puron
®
(R-410A) refrigerant.
Do not use any other refrigerant in this system.
Puron (R-410A) refrigerant is provided in pink (rose) colored
cylinders. These cylinders are available with and without dip
tubes; cylinders with dip tubes will have a label indicating this
feature. For a cylinder with a dip tube, place the cylinder in the
upright position (access valve at the top) when removing liquid
refrigerant for charging. For a cylinder without a dip tube, in
-
vert the cylinder (access valve on the bottom) when removing
liquid refrigerant.
Because Puron (R-410A) refrigerant is a blend, it is strongly
recommended that refrigerant always be removed from the cyl
-
inder as a liquid. Admit liquid refrigerant into the system in the
discharge line. If adding refrigerant into the suction line, use a
commercial metering/expansion device at the gage manifold;
remove liquid from the cylinder, pass it through the metering
device at the gage set and then pass it into the suction line as a
vapor. Do not remove Puron (R-410A) refrigerant from the
cylinder as a vapor.
Fig. 20 — TXV Valve and Sensing Bulb Location
Fig. 21 — CoreMax
1
Access Port Assembly
TXV SENSING
BULB
CLAMP
THERMAL EXPANSION
(TXV) VALVE
SENSING BULB INSULATION REMOVED FOR CLARITY
1. CoreMax is a registered trademark of Fastest, Inc.
5/8
” HEX
0.47
30°
0.596
1/2-20 UNF RH
1/2
” HEX
45°
WA
S
HER
O-RING
7/16-20 UNF RH
DEPRE
SS
OR PER AHRI 720
+.01/-.035
FROM FACE OF BODY
This surface provides a metal to metal seal when
torqued into the seat. Appropriate handling is
required to not scratch or dent the surface.
S
EAT
CORE
(Part No. EC39EZ067)
Содержание 547K
Страница 94: ...94 APPENDIX D WIRING DIAGRAMS Fig I 547K 04 06 Power Wiring Diagram 208 230 1 60 ...
Страница 95: ...95 APPENDIX D WIRING DIAGRAMS Fig J 547K 04 07 Power Wiring Diagram 208 230 3 60 ...
Страница 96: ...96 APPENDIX D WIRING DIAGRAMS Fig K 5047K 04 07 Power Wiring Diagram 460 575 3 60 ...