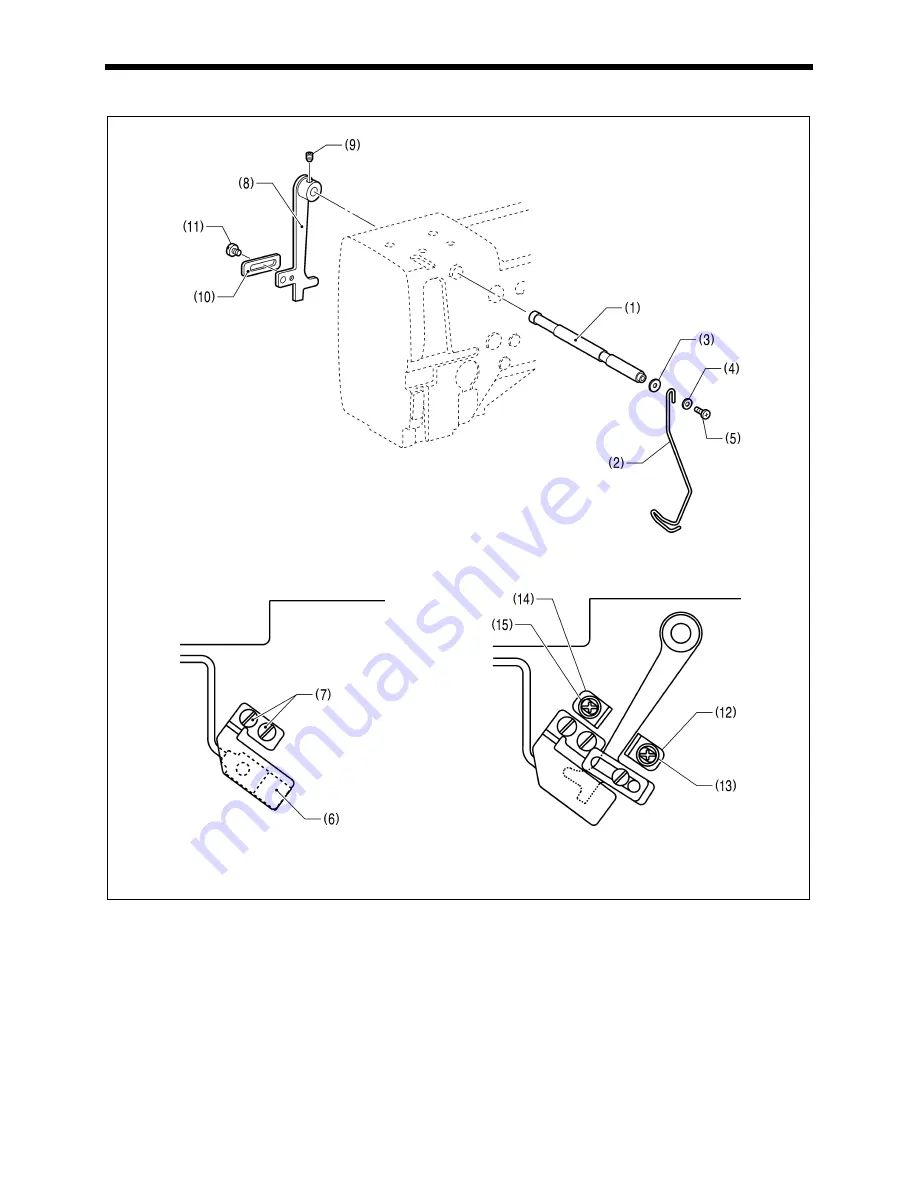
3. ASSEMBLY
HE-800A
71
3-21. Thread breakage detection mechanism
1. Provisionally install the thread guide (2) to the thread breakage perceiving shaft (1) with the plain washers (3)
and (4) and the screw (5), and then insert the thread breakage perceiving shaft (1) into the arm.
2. Provisionally install the thread breakage sensor assembly (6) with the two screws (7).
3. Install the cutter bar fixing plate (8) to the thread breakage perceiving shaft (1) with the set screw (9).
4. Install the balancer (10) to the cutter bar fixing plate (8) with the screw (11).
5. Install the lever stopper (12) at the correct angle with the screw (13).
6. Provisionally install the lever stopper (14) with the screw (15).
* After installing, carry out the steps in “4-17. Adjusting the thread breakage detector”.
4261Q
4262Q
4260Q