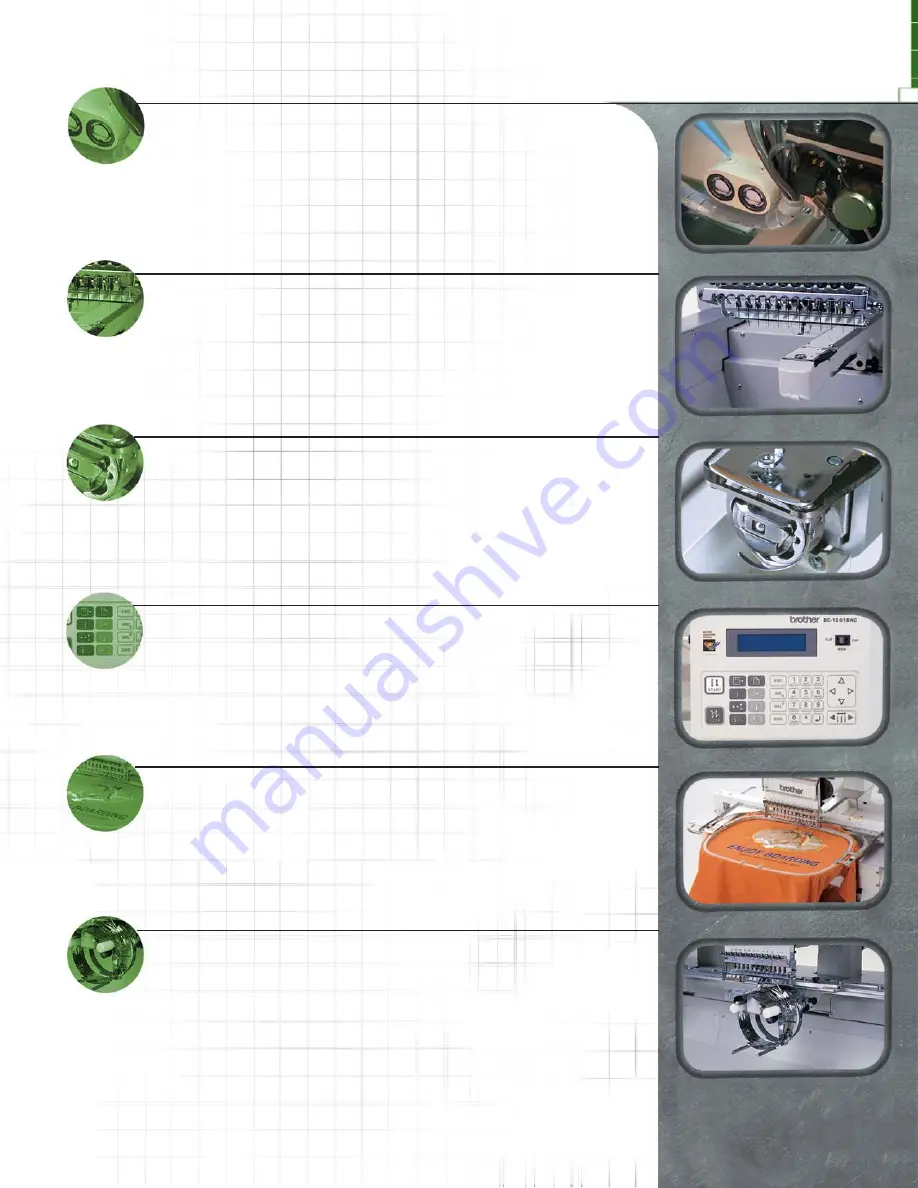
AUTOMATIC LUBRICATION SYSTEM
EASY-TO-USE CONTROL PANEL
Brother’s unique wick oiling system significantly reduces machine maintenance
downtime. Oil is poured into a conveniently located reservoir on the machine, and a
wick that is threaded through the internal workings of the sewing head delivers oil
when and where it is needed, eliminating the time-consuming task of oiling
numerous hard-to-reach locations.
Developed by Brother, the cam-driven presser foot allows the machine to run faster and
quieter. The precise movement of the cam reacts faster than the previous spring-loaded
technology and reduces the noisy pounding of the presser foot on the throat plate. The
single presser foot also facilitates increased machine speed and less maintenance.
JUMBO BOBBIN
Maximize system productivity with fewer bobbin changes with the larger capacity,
jumbo “M” style bobbins. Brother perfected the performance of the jumbo bobbin by
designing the cams and gears inside the sewing head to accommodate the longer
rotation of the larger bobbin.
Start sewing faster with the simple, logical commands found on the control panel. For
example, the hoop feed button moves the pantograph out from under the needles for
trouble-free applique placement and easier loading and unloading of hoops.
MEMORY RETENTION
Resume stitching a partially complete design after the machine has been turned off,
unplugged, or even after power failure. Shut the machine off to work with a customer,
go home for the evening, or even move the machine across town and never lose a
stitch or go off registration — another Brother first.
SINGLE CAM-DRIVEN PRESSER FOOT
INDIVIDUAL CAP FRAME ADJUSTMENT
Adjust the center point of the cap on each head independently while it’s in the frame
and mounted on the machine. Eliminate off-center designs and time-consuming
framing adjustments with this advanced cap frame driver design.
Содержание BE-0901E-AC
Страница 1: ...BROTHER EMBROIDERY SYSTEMS ...