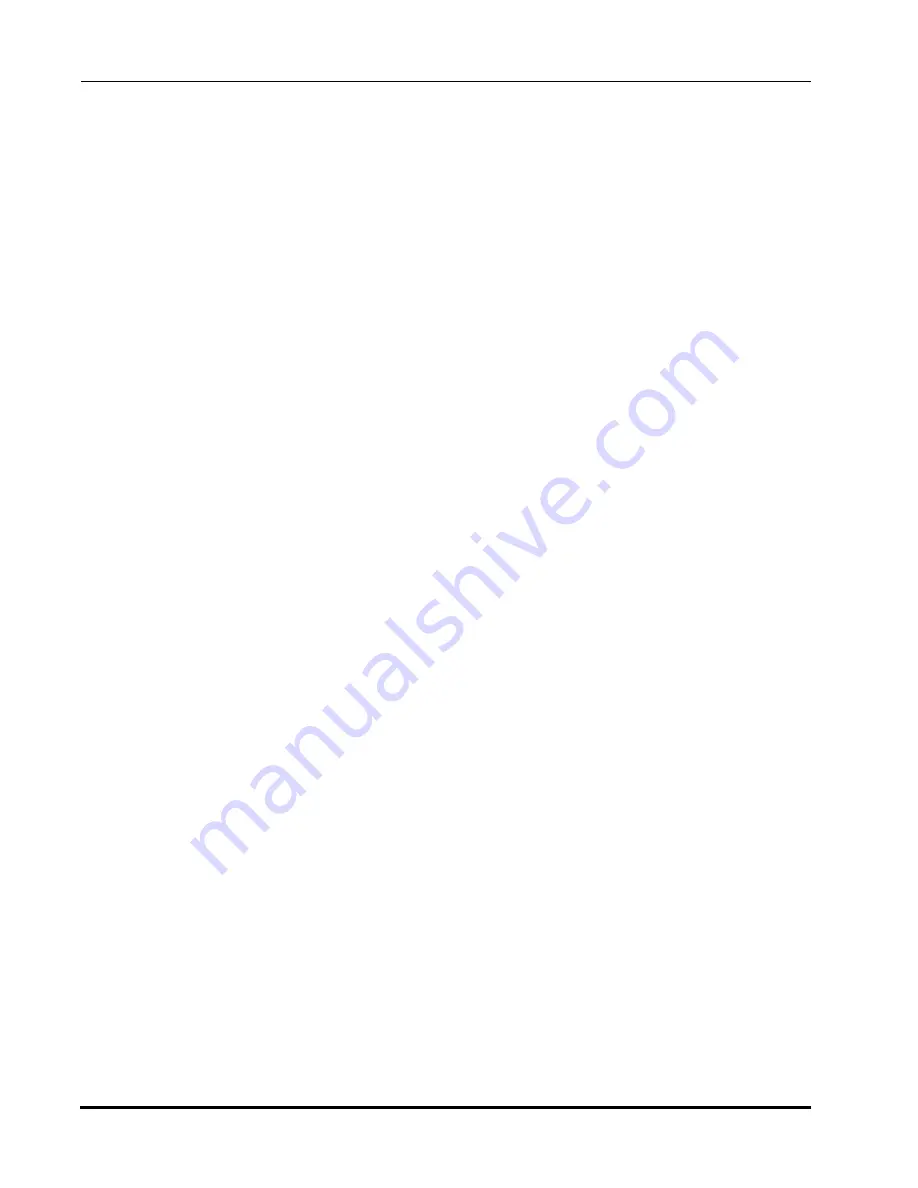
Alignment and Calibration
MagnaTran 7.1 User’s Manual
Robot Alignment
MN-003-1600-00
Brooks Automation
7-2
Revision 2.2
Robot Alignment
The Brooks Automation MagnaTran 7 Robot must be aligned with the system that it
will be operating in to prevent misplacement of the wafers or collision of the robot
with other parts of the system. Note that even a small misalignment can interfere
with proper system operation.
The user must perform the following alignment procedure as part of installing the
robot in a system, during routine maintenance, whenever the robot’s arms or end
effectors require replacement, or when one of the system modules requires replace-
ment. Brooks Automation recommends an alignment check under the following cir-
cumstances:
•
A complete alignment when the MagnaTran 7 robot is first set up at the user’s
site.
•
A complete check at all stations when the robot’s end effector, the robot’s arms,
or the robot is replaced.
•
A complete check of the robot if it was involved when an Emergency Off
(EMO) occurs.
•
A partial alignment at the appropriate station(s) whenever any component,
such as a cassette elevator, the degass module, or a robot is replaced.
•
A partial check at the problem station when a wafer transfer error occurs.
•
A complete check of the robot if it was involved in a collision.
Required Tools and Test Equipment
Performing the alignment procedure requires the following tools and materials:
•
A set of Allen wrenches in inch sizes
•
A set of Allen wrenches in metric sizes
•
The MagnaTran 7 Robot User’s Manual
•
The robot’s Control/Display Module (CDM)
•
One wafer of the size for which the system is being set up
•
Granite surface block