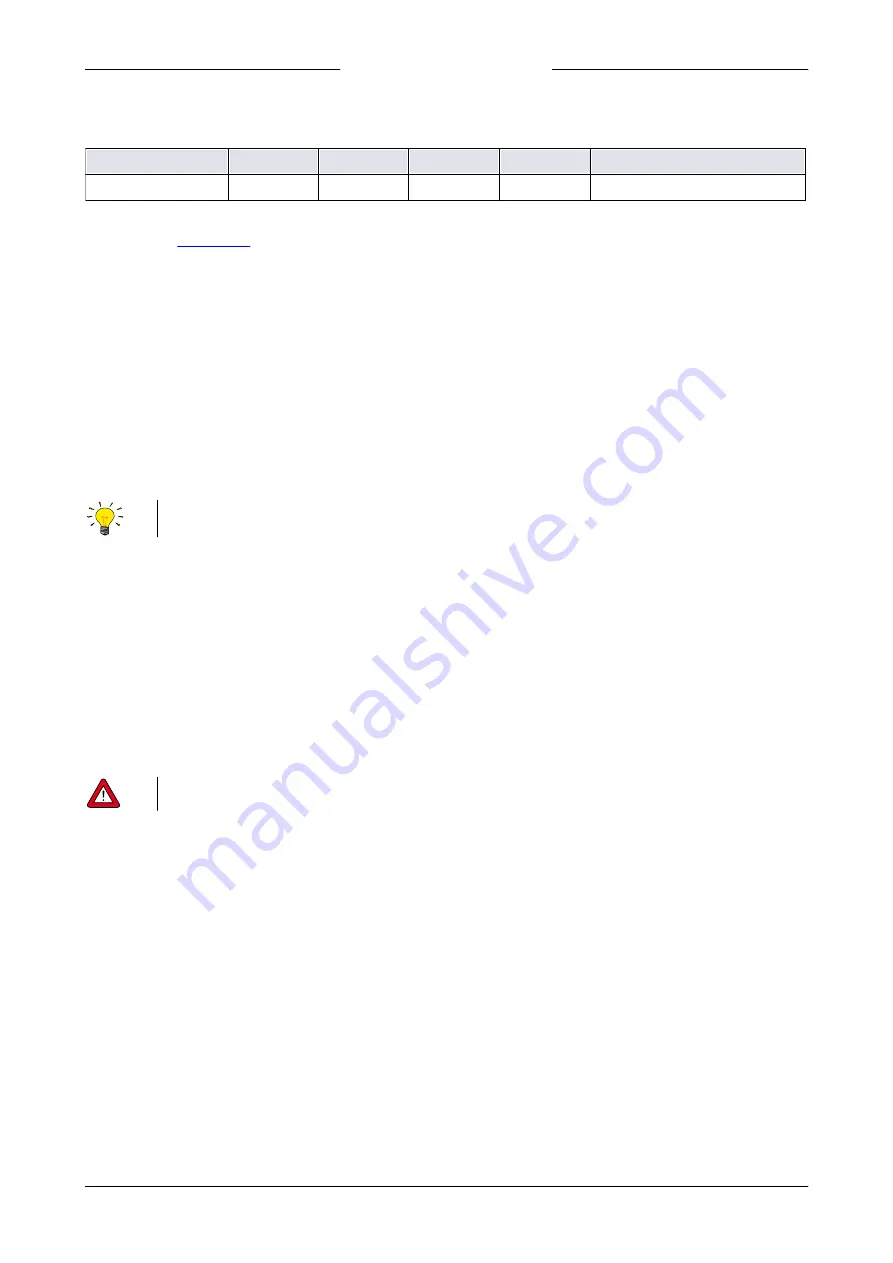
Bronkhorst®
Instruction Manual ES-FLOW™
9.17.145E
47
3.4.9.1
Default control mode
IO Status
Type
Access
Range
FlowDDE
FLOW-BUS
Modbus
Unsigned char
RW
0…255
86
114/11
0x0E4B/3660
The instrument is set to accept a setpoint from either an analog or a digital source. Although this setting can be changed
with parameter
, the instrument usually returns to its default control mode at every power-up or reset. The
default control mode can be set with parameter
IO Status
; to change it, use the procedures as described below.
Changing from digital operation to analog operation:
1. Set parameter
Init Reset
to 64 (unlocked)
2. Read parameter
IO Status
3. Add 64 to the read value
4. Write the new value to parameter
IO Status
5. Set parameter
Init Reset
to 82 (locked)
Changing from analog operation to digital operation:
1. Set parameter
Init Reset
to 64 (unlocked)
2. Read parameter
IO Status
3. Subtract 64 from the read value
4. Write the new value to parameter
IO Status
5. Set parameter
Init Reset
to 82 (locked)
The procedures described above do not change the value of parameter
Control Mode
directly. To apply the new default
control mode immediately, change the value of parameter
Control Mode
manually or reset or restart the instrument.
3.5
Adjusting zero point
The zero point (the signal that corresponds to zero flow) of a Bronkhorst® flow meter/controller is factory adjusted at
approximately 20 °C and atmospheric pressure, with the instrument in an upright position. If the ambient conditions or
mounting position are significantly different, the instrument might detect a flow when actually there is none. In that case,
the instrument needs to be adapted to the new conditions by re-adjusting the zero point.
Zeroing an instrument requires that:
·
the ambient conditions (temperature, pressure) match those of the operating environment of the instrument
·
the instrument is filled homogeneously with the operational media
·
there is absolutely no flow through the instrument; preferably, this is achieved by closing a valve immediately after the
outlet of the instrument (control valve, shut-off valve)
Blocking the flow through the instrument is absolutely essential; zeroing an instrument while there is still a flow will lead to
measurement errors.
The zeroing procedure can be performed in the following ways:
·
with the autozero function of the integrated user interface module
·
manually (using the multifunctional switch)
·
digitally (via RS-232 or fieldbus)
Once started, the zeroing procedure takes approximately 25 seconds to complete (longer if the output signal is unstable),
regardless of the preferred method.