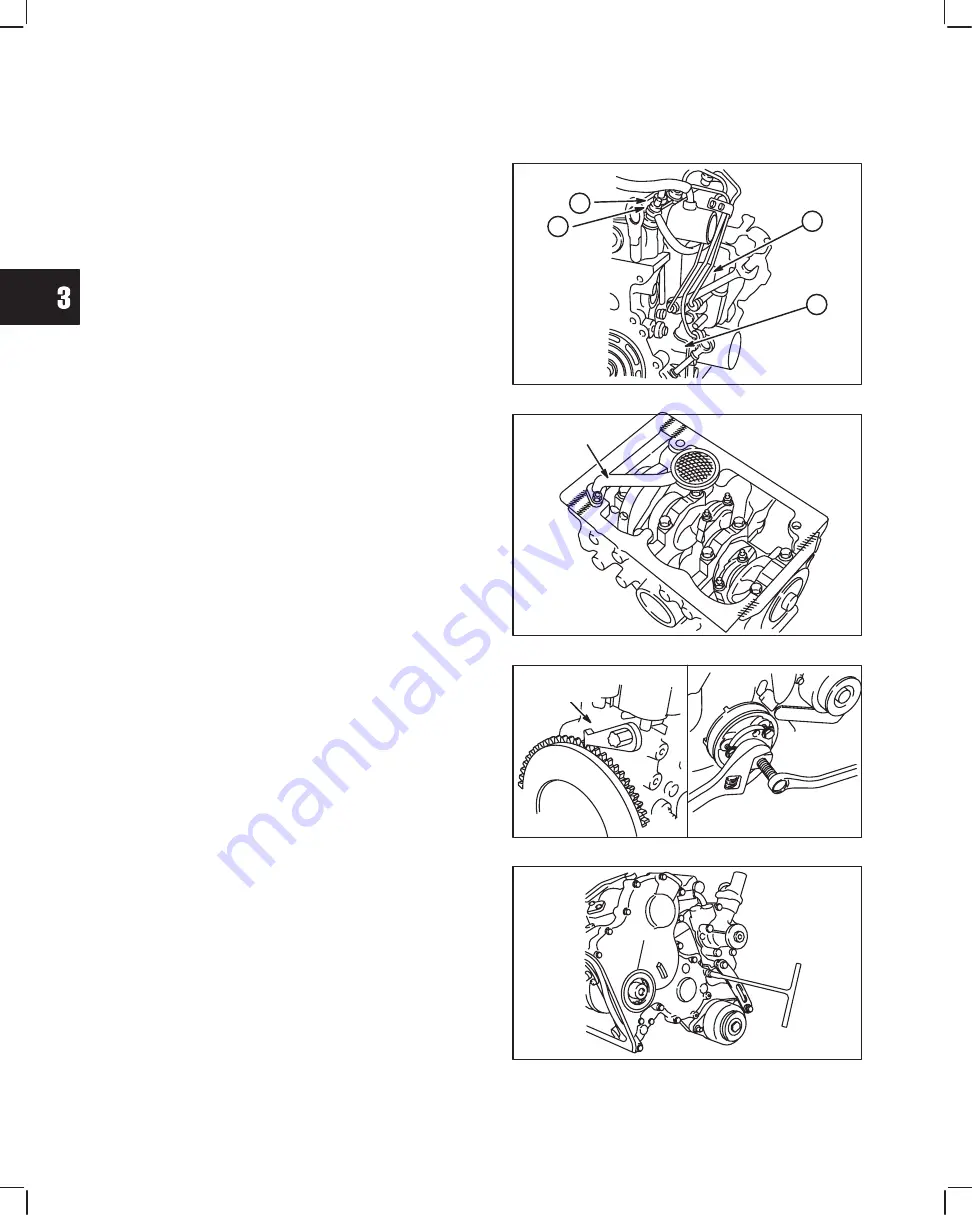
3
2
TIMING GEARS AND GEAR CASE
REMOVING TIMING GEAR COVER
AND GEARS
Make sure that #1 cylinder is at TDC, compression
stroke. See Section 2, Fig. 6.
Remove V-belt and fan (if equipped). Drain oil from
engine.
NOTE:
Clean areas around fuel lines and injec-
tors to prevent dirt entry.
1. Remove the following parts, Fig. 1.
a. Glow plug wiring.
b. Glow plugs.
c. Injector pump bracket.
d. Remove fuel delivery lines.
Fig. 1 – Remove Fuel Delivery Lines
B
A
C
D
2. Remove the following parts, Fig. 2.
a. Remove oil pan and discard gasket.
b. Remove oil pick-up tube and strainer. Discard
gasket.
Fig. 2 – Removing Oil Pan
OIL PICK-UP
TUBE
3. Remove bell housing adapter screw if equipped.
and install flywheel holder, Tool #19418.
4. LEAVE TOOL INSTALLED.
a. Remove crankshaft pulley using Tool
# 19420, Fig. 3.
Fig. 3 – Removing Crankshaft Pulley
FLYWHEEL
HOLDER
5. Remove timing gear cover, Fig. 4.
a. Discard timing gear cover gasket.
Fig. 4 – Removing Timing Gear Cover