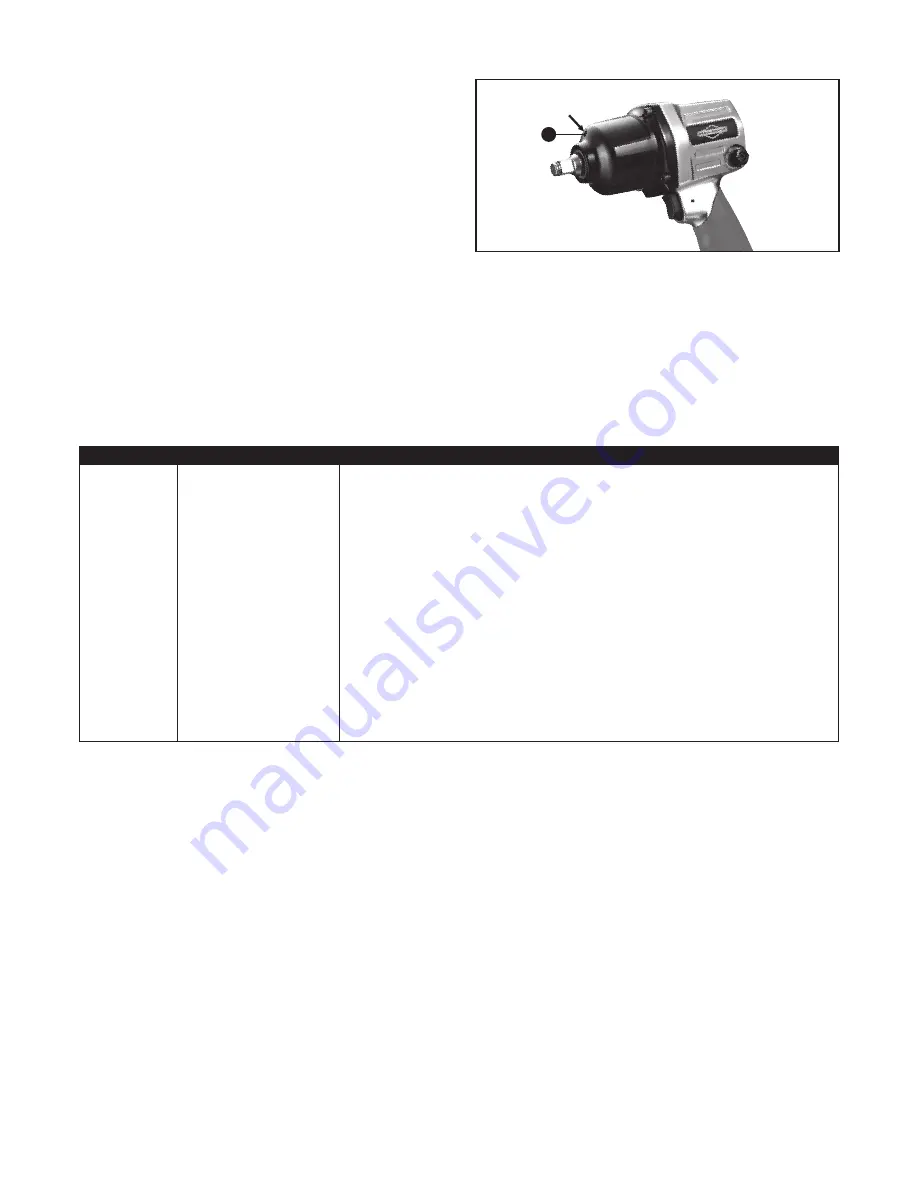
NOTE
This tool also features a grease cap (F) on the protector
cover. Remove the screw in the grease cap with a hex key (not
provided). Use a grease gun (not included) and insert the gun
nozzle into the grease cap. Several drops of grease are
recommended for lubrication. After lubrication, replace the screw
secure and tight. This will help the hammer assembly to work in
good condition and extend too life. Lubricate the hammer
assembly once every working day. (See Figure 6)
Figure 6
F
6
BRIGGSandSTRATTON.COM
Care and Maintenance
An in-line oiler is recommended to be installed on air supply line as it increases tool life and keeps the tool in sustained opera-
tion. The in-line oiler should be regularly checked and filled with air-tool oil. Proper adjustment of the in-line oiler is performed
by placing a sheet of paper next to the tool's exhaust ports and holding the throttle open approximately 30 seconds. The in-line
oiler is properly set when a light stain of oil collects on the paper. Excessive amounts of oil should be avoided.
In the event that it becomes necessary to store the tool for an extended period of time, it should receive a generous amount of
lubrication at that time. The tool should be run for approximately 30 seconds to ensure oil has been evenly distributed through-
out the tool. The tool should be stored in a clean and dry environment.
Recommended lubricants: use air-tool oil or any other high-grade turbine oil containing moisture absorbent, rust inhibitors,
metal wetting agents and an EP (extreme pressure) additive.
Clean the tool all over with a cotton rag after each use. Keep the tool in a dry and safe place out of reach of children.
Troubleshooting
1. Flush the tool with air tool oil or gum solvent.
2. Lubricate the tool.
3. a. Adjust the regulator on the tool to the maximum setting if available.
b. Adjust the compressor regulator to the tool maximum of 90 PSI/6.3 bar.
4. Tighten and seal hose fittings if leaks are found. Use sealing tape.
5. a. Be sure the hose is the proper size. Long hose or tools using large volumes
of air may require a hose with an I.D. of 1/2 in. or larger depending on the
total length of the hoses.
b. Do not use a multiple number of hoses connected together with quick-
connect fittings. This causes additional pressure drops and reduces the tool
power. Directly connect the hoses together.
6. Have qualified technician replace the rotor blade.
7. Drain water from tank. (See the air compressor manual). Oil the tool and
continue running it until no water is evident. Oil the tool again and run for
1-2 seconds.
T
ool runs
slowly or will
not operate.
1. Grit or gum in the tool.
2. No oil in the tool.
3. Low air pressure.
4. Air hose leaks.
5. Pressure drops.
6. Worn rotor blade.
7. Moisture blowing out
of the tool exhaust
.
PROBLEM
CORRECTIVE ACTION
POSSIBLE CAUSE
Not
for
Reproduction