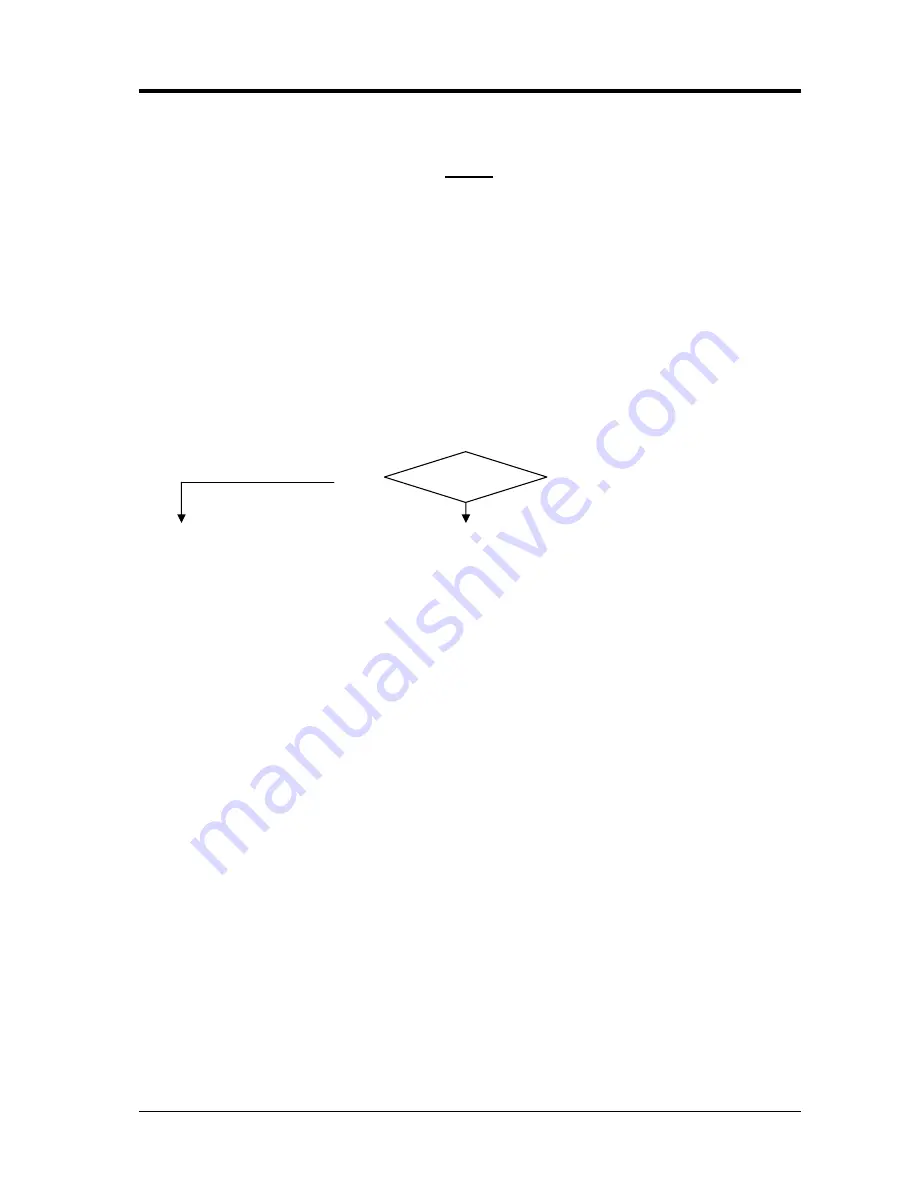
CEBORA S.p.A.
18
3.3.11
- When start button is released, the wire sticks to the workpiece (ineffective motor
braking).
NOTE
The “Burn-Back” function is included in the working programs and is adjustable via the
control panel (see Instruction Manual).
With this function the power source delays stopping current generation during the slowdown
of the wire output from the torch, since even though it brakes after welding, the wire feeder
motor still requires a certain amount of time to come to a complete stop.
This time depends on various circumstances such as the type of torch, size of the wire coil,
type of wire, wire speed during welding, etc.
Thus if the wire sticks to the workpiece at the end of the welding process, consider the
aforementioned conditions and perform the following test.
WIRE FEEDER MOTOR (403) BRAKING TEST.
Correct?
Control board (4), connector J8 terminals 1 and 2 (gnd) = fig. 5.2.1, when the start button is
released, with the power source open-circuit (no wire in the torch). The wire feeder motor
stops immediately (braking time <200 msec.).
YES
NO
♦
If you encounter fig. 5.2.2 (the motor slows from its own inertia), the braking
circuit on the control board (4) does not work properly, replace control board (4).
♦
Make sure that there are no mechanical impediments preventing the wire coil from stopping
despite the braking action of the motor (ex.: sliding by wire feeder rollers, improperly
adjusted roller spring).
♦
Replace the control board (4) and/or motor (403).
3.302.200
29/04/05