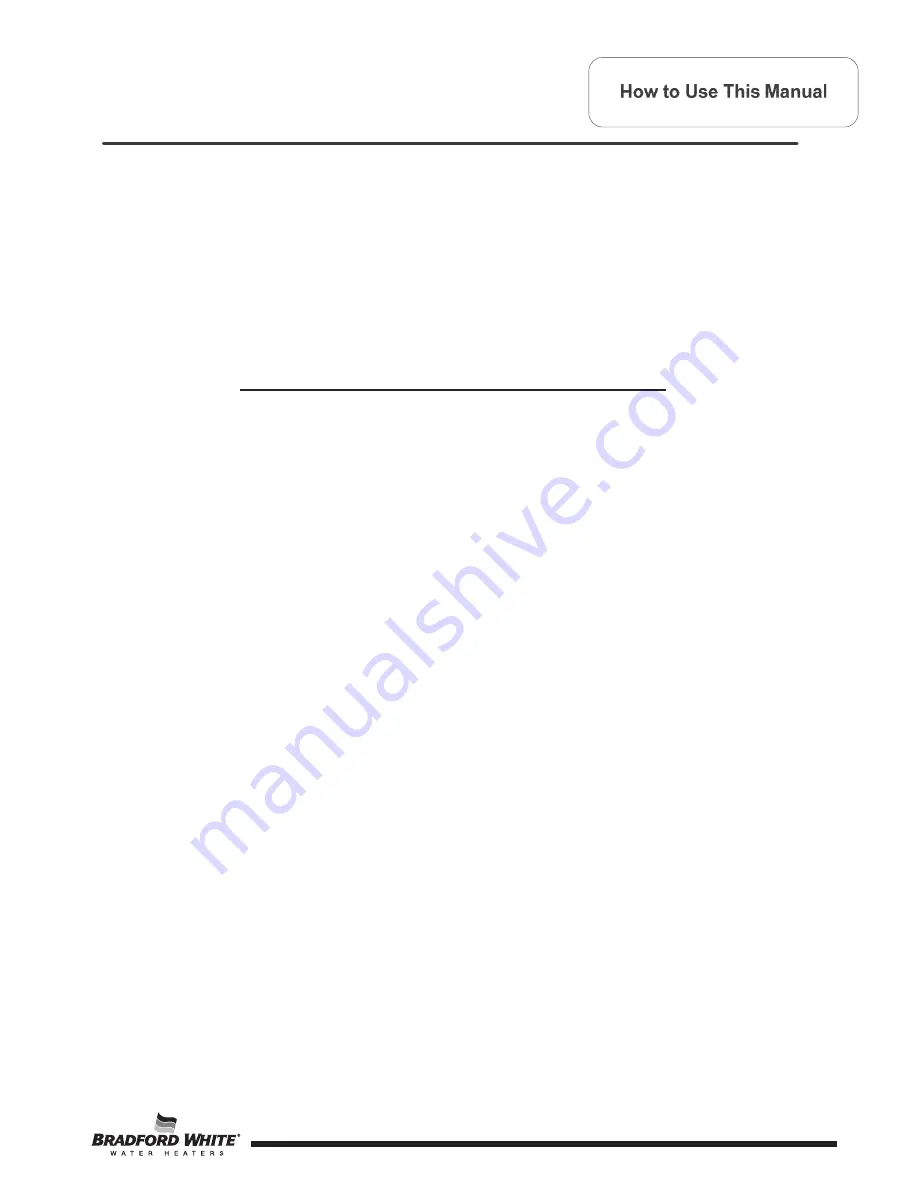
5
ECO Defender Series
5
It is intended for this manual to be used by qualified service personnel for the primary purpose of
troubleshooting and repair of the Bradford White ECO-DEFENDER Series water heaters.
The Honeywell WV8860 Gas Control will display status codes in the event of abnormal operation. Status
codes are listed in the troubleshooting chart beginning on page 6 of this service manual. The troubleshooting
chart will also indicate the probable cause for the status code and direct the service professional to a service
procedure to properly diagnose the abnormal operation.
Contact the Bradford White technical support group immediately if diagnosis cannot be made using the
methods described in this service manual.
Tools Required for Service
Manometer:
Multi-Meter:
Electronic Probes:
Thermometer:
Water Pressure Gage:
Various Hand Tools:
A liquid “U” tube type or a digital (magnahelic) type can be used. This
device is used to measure gas and/or air pressure and vacuum.
A digital type is strongly recommended. This device is used to measure
electrical values. The meter you select must have the capability to
measure volts AC, volts DC, Amps, micro-amps and ohms.
In some cases, standard multi-meter probes will damage or simply not be
effective to obtain certain voltage and ohm readings. It will be necessary to
have special electronic “pin” type multi-meter probes. These probes are
available at most electronic wholesale outlets.
Used to measure water temperature. An accurate thermometer is
recommended.
Used to measure water supply pressure. Also used to determine tank
pressure by adapting to the drain valve of the heater.
Pipe wrench, channel locks, open end wrenches (3/8”, 7/16”, 1/2”), 12”
crescent wrench, allen wrench set, screw drivers (common & Phillip’s), 1/4”
nut driver, pliers (common & needle nose), socket set, side cutters, wire
cutters, wire strippers, wire crimpers, torpedo level, small shop vac, step
ladder, flashlight and 5 gallon pail.
Содержание URG130T*N Series
Страница 28: ......