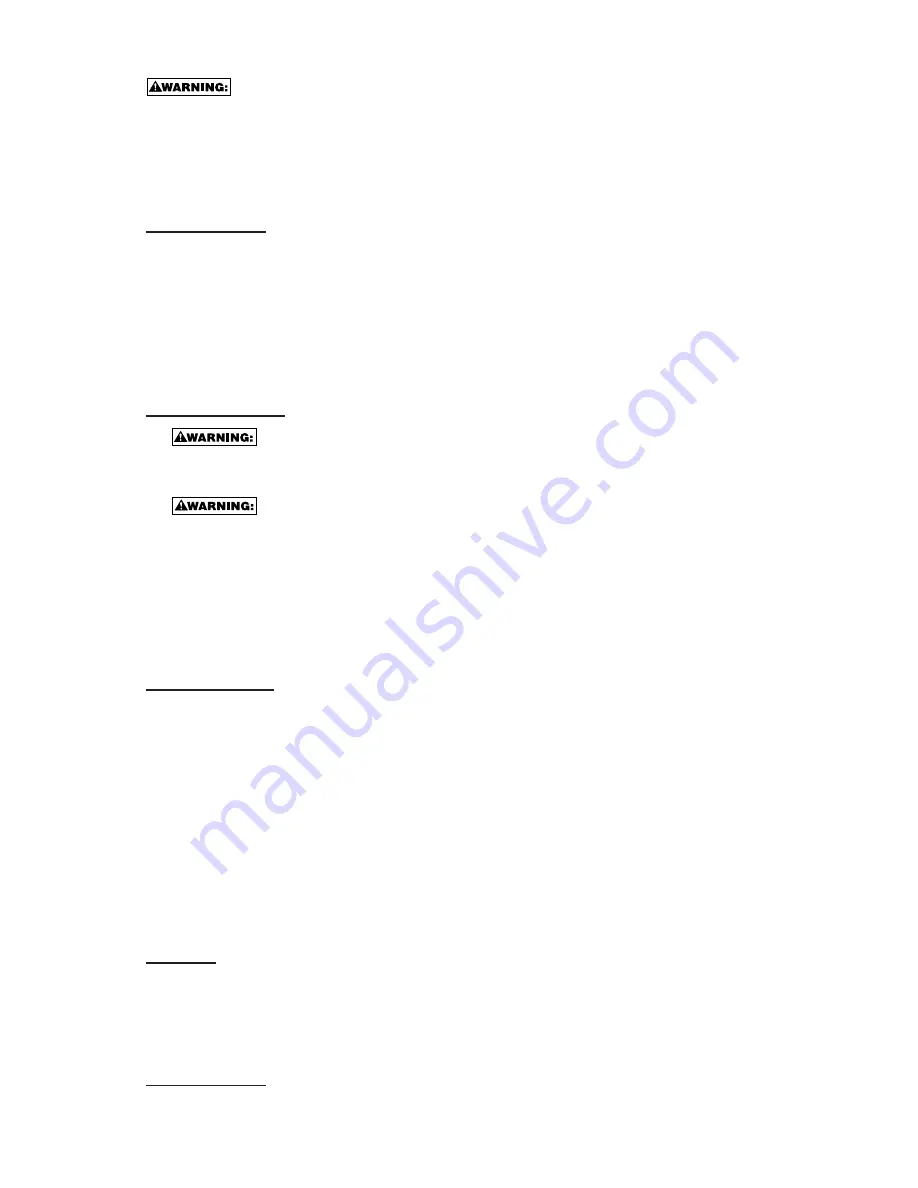
TO PREVENT ACCIDENTAL INJURIES:
• Never place a hand or any other part of the body in staple discharge area of
tool while the air supply is connected.
• Never point the tool at anyone else.
• Never engage in horseplay.
• Never pull the trigger unless nose is directed at the work.
• Always handle the tool with care.
• Do not pull the trigger while loading the tool.
TO OPERATE
SHUT OFF AIR SUPPLY BEFORE MAKING ADJUSTMENT, REMOVING CLOGGED STAPLES OR SERVICING.
To operate machine, grasp handle. Position machine on box placing directly over the seam between flaps and
in line with desired staple location. Squeeze trigger and release completely before moving machine. Move
machine to each staple position and repeat. Strongest closure requires end staples close to end of box,
approximately 1” (25.4mm). Be sure staples penetrate inner flaps. Check staple clinching in sample of box
board, such as that being used. Adjustment for depth of penetration is easy and full advantage should be taken.
Clincher adjusting clamp settings as listed in chart are offered only as a guide and may have to be slightly
modified.
MAINTENANCE
Always disconnect air supply: 1.) Before making adjustments; 2.) When servicing the tool;
3.) When clearing a jam; 4.) When tool is not in use; 5.) When moving to a different work
area, as accidental actuation may occur, possibly causing injury.
When working on air tools note the warnings in this manual and use extra care when
evaluating problem tools.
Specify the part number when ordering replacement parts. Do not order by description. Do not wrench, twist or
force parts during servicing, as damage may result.
Check screws periodically for tightness. Observe caution against stripping threads when tightening. When the
tool is disassembled, clean thoroughly. Lubricate all moving parts after cleaning. Apply “Magnalube-G” to O-
rings. Examine all parts for wear during servicing so that replacement parts can be ordered in advance of
trouble.
LUBRICATION
Frequent, but not excessive, lubrication is required for best performance. Oil added through the air line
connection will lubricate the internal parts. Use BOSTITCH Air Tool Lubricant, Mobil Velocite #10, or
equivalent. Do not use detergent oil or additives as these lubricants will cause accelerated wear to the seals
and bumpers in the tool, resulting in poor tool performance and frequent tool maintenance.
If no airline lubricator is used, add oil during use into the air fitting on the tool once or twice a day. Only a few
drops of oil at a time is necessary. Too much oil will only collect inside the tool and will be noticeable in the
exhaust cycle.
CAUTION:
Do not store tools in a cold weather environment to prevent frost or ice formation on the tools
operating valves and mechanisms that could cause tool failure.
NOTE:
Some commercial air line drying liquids are harmful to “O”-rings and seals – do not use these low
temperature air dryers without checking compatibility.
FILTER:
Dirt and water in the air supply are major causes of wear in pneumatic tools. A filter will help to get the best
performance and minimum wear from the tool. The filter must have adequate flow capacity for the specific
installation. The filter has to be kept clean to be effective in providing clean compressed air to the tool.
Consult the manufacturer’s instructions on proper maintenance of your filter. A dirty and clogged filter will
cause a pressure drop which will reduce the tool’s performance.
REGULATOR:
A pressure regulator with an operating pressure of 0 - 125 p.s.i. (0 - 8.79 KG/CM2) is required to control the
operating pressure for safe operation of this tool. Do not connect this tool to air pressure which can potentially
exceed 200 p.s.i. (14 KG/CM2)as tool may fracture or burst, possibly causing injury.