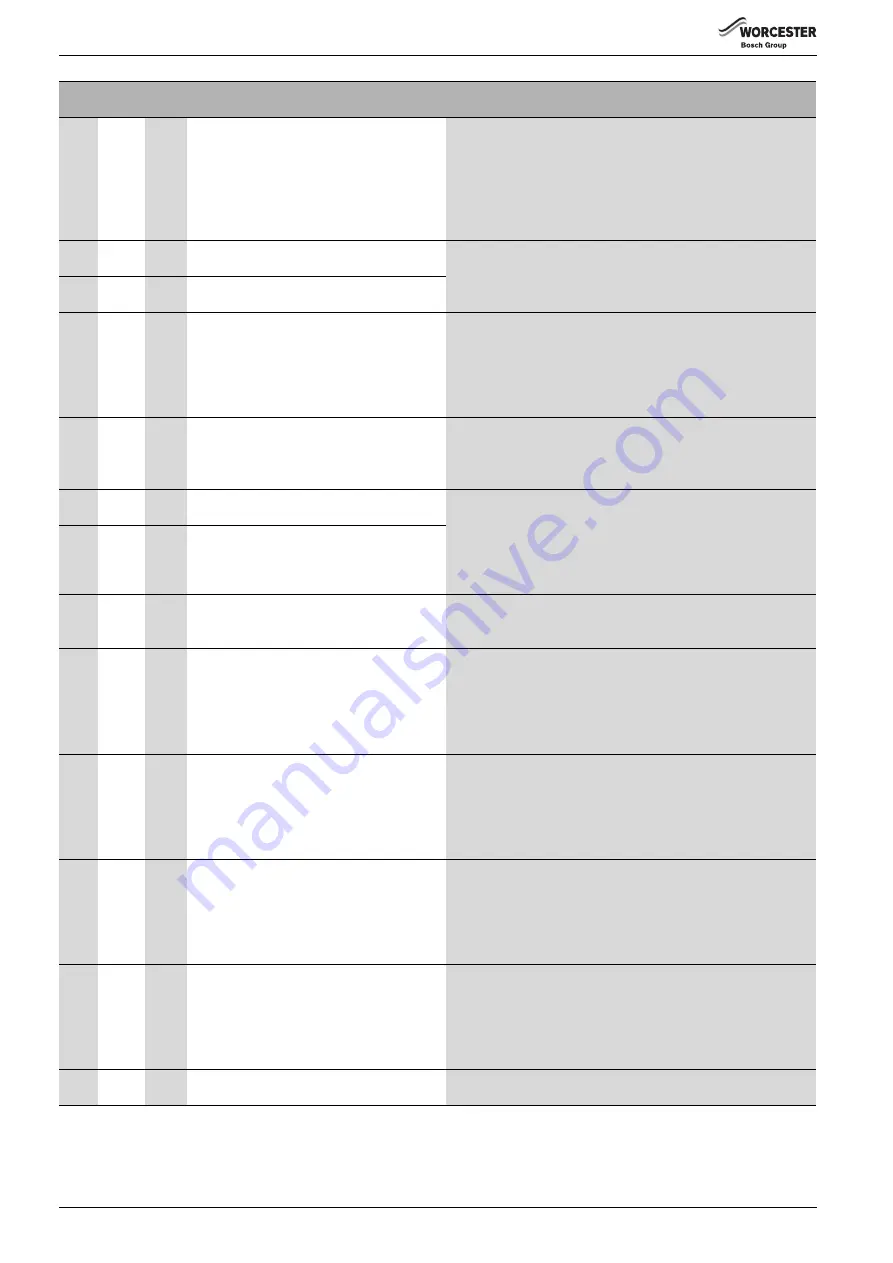
Display codes
6720814332 (2018/04)
46
d 4
2 8 6
3
The boiler return temperature sensor has
detected a return temperature higher than
105 °C.
▶ Check the water pressure of the boiler, vent the heating system and
the boiler.
▶ Check whether it is possible to achieve sufficient flow in the heating
system.
▶ Check plug and cabling of the boiler return temperature sensor.
▶ Check the function of the boiler by replacing the boiler return
temperature sensor.
E 2
2 2 2
3
Short circuit in the flow temperature sensor
contacts.
▶ Check the plug of the sensor.
▶ Check the operating characteristics of the boiler by replacing the
sensor.
E 2
2 2 3
3
The flow temperature sensor contacts have been
interrupted.
E 5
2 1 8
3
The temperature captured by the flow
temperature sensor exceeds 105 °C.
▶ Check the water pressure of the boiler, vent the heating system and
the boiler.
▶ Check whether it is possible to achieve sufficient flow in the heating
system.
▶ Check the operating characteristics of the pump and the flow
temperature sensor. Replace the faulty component if necessary.
E 9
2 1 0
3
The temperature measured by the flue gas sensor
is too high and it is open.
▶ Check the function of the flue gas sensor. Replace if necessary.
▶ Check the boiler for soiling. Carry out a service if necessary.
▶ Check, via the flue inspection elbow, the seating of the flue gas non-
return valve. Check for obstruction.
E 9
2 1 9
3
The safety temperature sensor has captured a
temperature in excess of 105°C.
▶ Check the water pressure of the boiler, vent the heating system and
the boiler.
▶ Check whether it is possible to achieve sufficient flow in the heating
system.
▶ Check the operating characteristics of the pump and the sensor.
Replace the faulty component if necessary.
E 9
2 2 0
3
The contacts for the safety temperature sensor
have shorted or the safety temperature sensor has
detected a temperature higher than 130 °C.
E 9
2 2 1
3
The contacts of the safety temperature sensor
have been interrupted.
▶ Check the plug of the sensor.
▶ Check the operating characteristics of the boiler by replacing the
sensor.
E 9
2 2 4
3
The temperature measured by a device
thermostat (e.g. maximum or burner thermostat)
is too high and it is open.
▶ Check whether it is possible to achieve sufficient flow in the heating
system.
▶ Check the burner gaskets for flue gas leaks. Replace the faulty burner
gaskets if necessary.
▶ Check the heat exchanger for soiling.
▶ Check the gas/air ratio.
E 9
2 7 6
2
The temperature measured by the flow
temperature sensor exceeds 95 °C.
▶ Check the water pressure of the boiler, vent the heating system and
the boiler.
▶ Check whether it is possible to achieve sufficient flow in the heating
system.
▶ Check the cabling and function of pump and flow temperature
sensor. Replace the faulty component if necessary.
E 9
2 7 7
2
The safety temperature sensor has measured a
temperature in excess of 95 °C.
▶ Check the water pressure of the boiler, vent the heating system and
the boiler.
▶ Check whether it is possible to achieve sufficient flow in the heating
system.
▶ Check the cabling and function of the pump and safety temperature
sensor. Replace the faulty component if necessary.
E 9
2 8 5
2
The boiler return temperature sensor has
measured a temperature higher than 95 °C.
▶ Check the water pressure of the boiler, vent the heating system and
the boiler.
▶ Check whether it is possible to achieve sufficient flow in the heating
system.
▶ Check the cabling and function of the pump and boiler return
temperature sensor. Replace the faulty component if necessary.
E 9
3 1 8
3
The flue gas temperature sensor contacts have
been interrupted.
▶ Check the function of the flue gas temperature sensor. Replace if
necessary.
Code
Code
type Designation
Remedy
Table 19 Operating and fault codes
Содержание Worcester GB162-100 V2
Страница 49: ...6720814332 2018 04 49 Notes ...