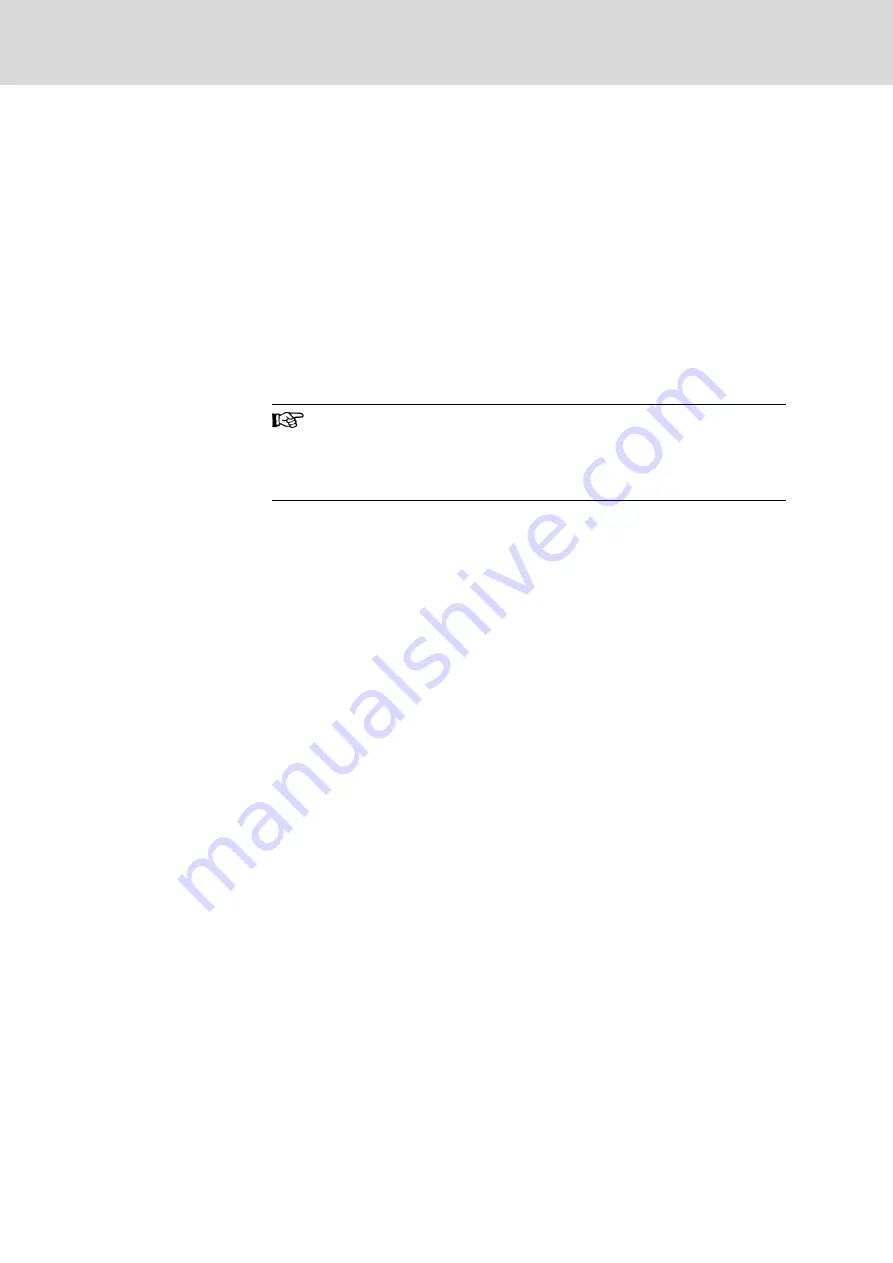
face (ET) of the control section, e.g. “CIP Safety on Sercos“, “Safety over
EtherCat“ or “PROFIsafe on PROFINET“.
Safety-capable encoder system
and encoder evaluation
In the case of encoder-dependent safety functions the selection of the encod‐
er system on the load side is decisive. The safety-capable encoder system
must
●
fulfill the preconditions for utilizing “Safe Motion”
●
always be connected to the first multiple encoder interface (EC) of the
X4 interface at the control section.
●
be supplied via the multiple encoder interface (EC) of the drive. (Supply
voltages of +5 V
DC
and +12 V
DC
are available.)
●
be electrically correctly connected to the multiple encoder interface as
specified. Pay particular attention to a proper execution of shield con‐
nections according to standards.
The precondition for utilizing “Safe Motion” is described in detail in
the application manual “Rexroth IndraDrive Integrated Safety
Technology "Safe Motion" (as of MPx-18)”, 911338920, see
ter 1.2 "Required and supplementary documentation" on page 5
.
These preconditions must strictly be fulfilled.
Testing of safety functions
To maintain the hydraulic safety function of the self-contained servo-hydraulic
linear axis, the customer has to initiate the operation mode “TEST MODE",
see
chapter "Description of state of optional “TEST MODE”" on page 61
at
regular intervals. When called, the self-test function deactivates alternately
one of the two retaining valves of the hydraulic safety function and monitors
its drop to the rest position via the assigned position monitoring feature. In
the case of malfunction the self-contained servo-hydraulic linear axis is stop‐
ped and an error message issued. The intervals between two self-tests have
to be determined under the responsibility of the machine manufacturer. He
knows the safety requirements for the complete machine and the end cus‐
tomer’s target application.
5.2.5
Extended filtering system (optional)
The optional extended filtering system is used in the case of harsh ambient
conditions or long periods of operation. For more detailed information, please
refer to
chapter 9.2 "Operational states" on page 59
, description of state of
optional “FILTERING OPERATION".
Bosch Rexroth AG
Operating Instructions
24/91
Self-contained servo-hydraulic linear axis Type SHA...
About this product
Содержание Rexroth SHA Series
Страница 1: ...Self contained servo hydraulic linear axis Type SHA Operating Instructions RE 62266 B_12 18 Edition 1 ...
Страница 6: ...Bosch Rexroth AG Operating Instructions IV 91 Self contained servo hydraulic linear axis Type SHA ...
Страница 20: ...Bosch Rexroth AG Operating Instructions 18 91 Self contained servo hydraulic linear axis Type SHA ...
Страница 48: ...Bosch Rexroth AG Operating Instructions 46 91 Self contained servo hydraulic linear axis Type SHA ...
Страница 60: ...Bosch Rexroth AG Operating Instructions 58 91 Self contained servo hydraulic linear axis Type SHA ...
Страница 68: ...Bosch Rexroth AG Operating Instructions 66 91 Self contained servo hydraulic linear axis Type SHA ...
Страница 74: ...Bosch Rexroth AG Operating Instructions 72 91 Self contained servo hydraulic linear axis Type SHA ...
Страница 76: ...Bosch Rexroth AG Operating Instructions 74 91 Self contained servo hydraulic linear axis Type SHA ...
Страница 78: ...Bosch Rexroth AG Operating Instructions 76 91 Self contained servo hydraulic linear axis Type SHA ...
Страница 86: ...Bosch Rexroth AG Operating Instructions 84 91 Self contained servo hydraulic linear axis Type SHA ...
Страница 88: ...Bosch Rexroth AG Operating Instructions 86 91 Self contained servo hydraulic linear axis Type SHA ...
Страница 90: ...Bosch Rexroth AG Operating Instructions 88 91 Self contained servo hydraulic linear axis Type SHA ...
Страница 93: ...Notes Operating Instructions Bosch Rexroth AG 91 91 Self contained servo hydraulic linear axis Type SHA ...