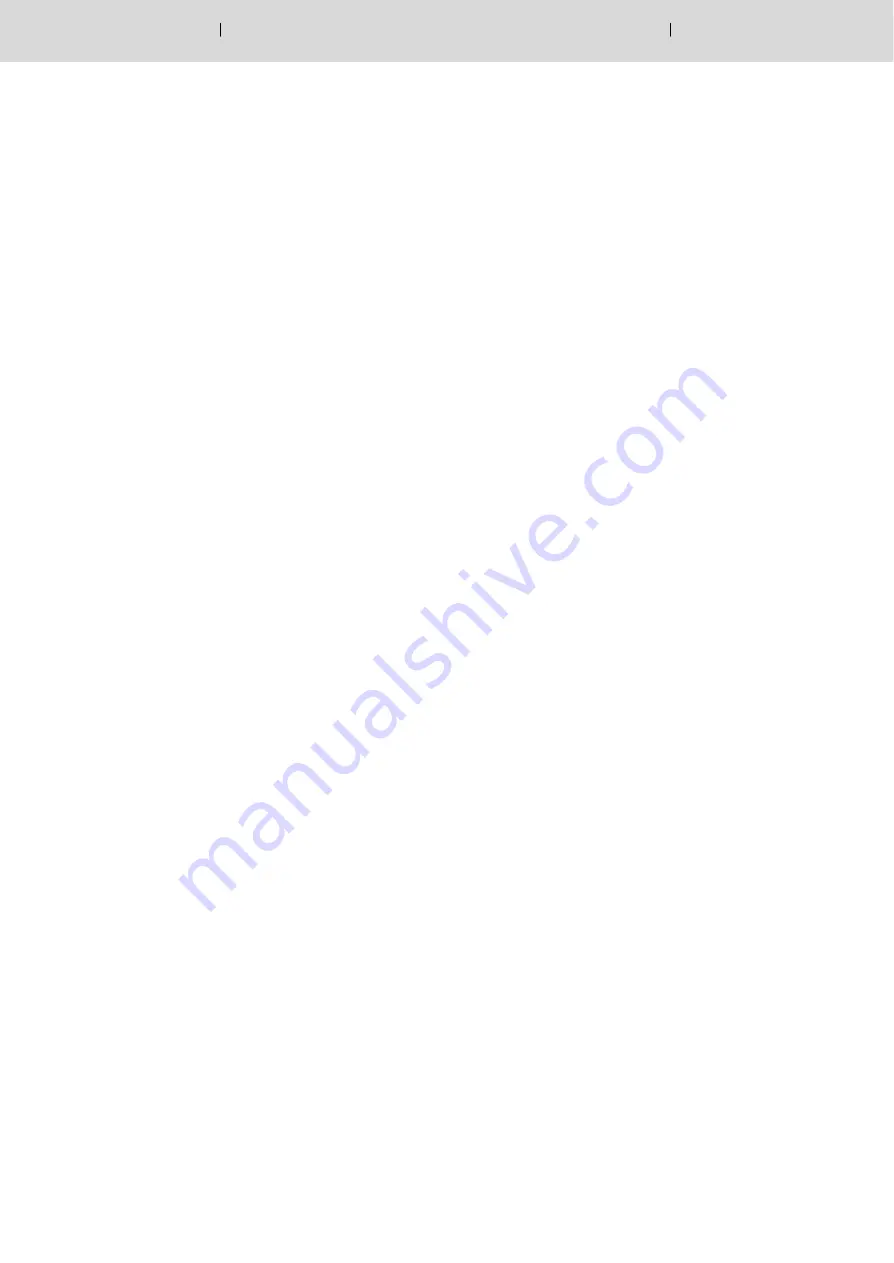
Electric Drives
and Controls
5−29
Bosch Rexroth AG
RhoMotion
1070072367 / 04
CAN-Bus peripheral equipment
5.6
SR-CAN module
To make sure that the machine parameters always fit to the kinematic
(mechanics) the machine parameters concerning the mechanics are
stored on an SR-CAN module. This module is firmly connected with the
robot mechanics, and is maintained during the robot service life.
The communication with the SR-CAN module takes place by means of
the CAN protocol. To be able to read and write the machine parameters,
corresponding functions are available in BAPS and as rho4 library func-
tions. The library functions are contained in the system group. The func-
tions for reading the SR-CAN modules are named rSGSrCan() and
rSGSerialNb(), the functions for writing in the SR-CAN module are na-
med rSSSrCan() and rSSSerialNb(). The machine parameters and se-
rial numbers contained in the real time core of the rho4.1 are loaded into
the SR-CAN module by means of these functions. Additionally, a rea-
ding and writing operation of the machine parameters and serial num-
bers to the SR-CAN module with PHG2000 are offered. The PHG menu
tree contains a mode protected by a password for this purpose. Mode
7.8.6.1 is assigned for reading and mode 7.8.6.2 for writing the serial
number onto the SR-CAN modules. Mode 7.8.6.3 is assigned for rea-
ding and mode 7.8.6.4 for writing the machine parameters onto the SR-
CAN modules.
Read/write functions
For the communication with the SR-CAN module, the before mentioned
read/write functions are available. As transfer parameters, the SR-CAN
module number and the kinematic (Kin1 to 16) have to be indicated in
any case, since a control can address several robots at the same time.
Machine parameter and serial number are separated on the SR-CAN
modules and have also to be written and read separately. During the run-
up phase of the control it is possible to quickly check which machine pa-
rameters are to be activated, since only the serial number of the SR-CAN
module has to be read.
When calling the write function rSSSrCan(), the complete machine para-
meters are loaded into the SR-CAN module. This is preferably be done
while measuring the robot kinematic of a new system or when changing
a defective SR-CAN module.
When calling the read function rSGSrCan(), at first also the complete
machine parameters are loaded from the SR-CAN module onto an inter-
mediate storage place in the control, yet are not active at this time. There
is a filter between this intermediate storage place and the valid machine
parameters that can be configured and only takes over selected ma-
chine parameters.
If all machine parameters are selected, the read function rSGSrCAN ()
acts as a machine parameter backup, i.e. the machine parameters are
all taken over from the SR-CAN module. To activate the machine para-
meters, the control must be run-up again.
Содержание Rexroth Rho 4.0
Страница 12: ...XII Electric Drives and Controls Bosch Rexroth AG RhoMotion 1070072367 04 Contents Notes ...
Страница 22: ...2 2 Electric Drives and Controls Bosch Rexroth AG RhoMotion 1070072367 04 System overview Notes ...
Страница 78: ...4 14 Electric Drives and Controls Bosch Rexroth AG RhoMotion 1070072367 04 PCLrho4 0 Notes ...
Страница 168: ...A 4 Electric Drives and Controls Bosch Rexroth AG RhoMotion 1070072367 04 Appendix Notes ...