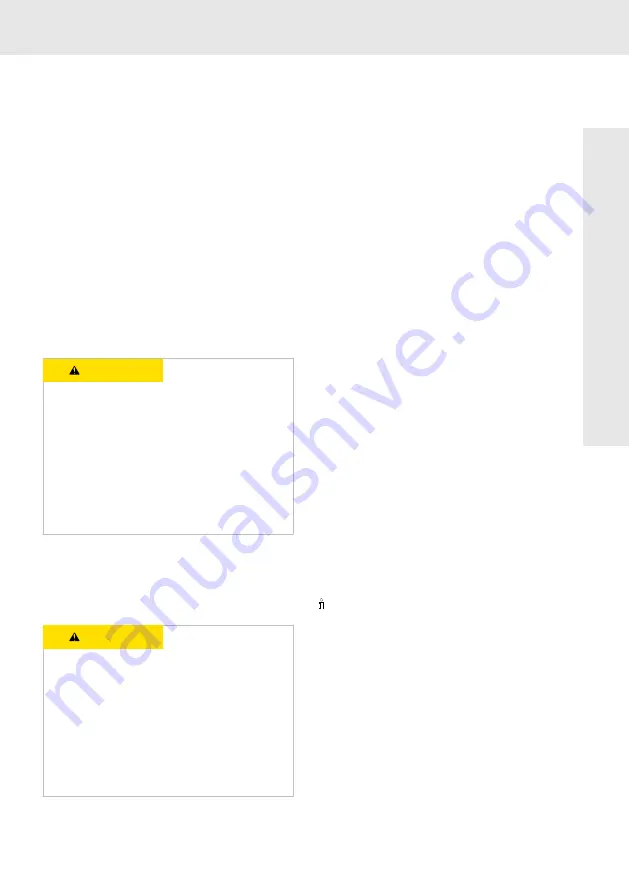
27 / 72
MS2N
Features and functions
Bosch Rexroth AG
R911347581, Edition 05
•
Number of operating cycles ≥ 5,000,000
•
The holding brakes with emergency stop
function are intended to secure motor shafts
at standstill. The holding brakes are no oper-
ation brakes to decelerate motors in opera-
tion from speed.
•
In case of an emergency stop or voltage
drop, the brake operation is only allowed to
a limited extend. Up to 500 breaking cycles
from speed 3000 1/min can be performed,
whereas the maximum switched energy per
emergency stop of the brake must not be
exceeded. The number of brake applications
per hour is 20, whereas a uniform scheduling
is a precondition. For specifications about
the max. switched energy per emergency
stop, see
CAUTION
Malfunctions due to wear
Impermissibly high wear due to breaking from
speed by exceeding the specified emergency
stop properties.
Avoid deceleration from speed during setup
mode.
Using the operating brake to decelerate the
rotating motor is not permissible.
The voltage supply of the holding brake has to
be designed so as to guarantee under the worst
installation and operation conditions that a suffi-
cient voltage 24 V DC ±10% is available at the
motor in order to release the holding brake.
CAUTION
Malfunction in case of exceeded tolerance of the
rated voltage (switching voltage)
For safe switching of the holding brake, a rated
voltage of 24 V DC ±10% is required at the
motor.
Ensure correct dimensioning of the supply wires
(wire length and cross-section) for the holding
brake.
The control voltage can be reduced using the
energy saving function after safely releasing the
brake, see
Chapter “Energy saving function for
.
The holding brakes are intended for direct con-
nection to the IndraDrive controller. A protective
circuit to switch inductive loads of holding brakes
is integrated in IndraDrive controllers. Please
observe when operating of third-party converters
that MS2N motors do not have an integrated pro-
tective circuit.
Energy saving function for holding brakes
Decrease brake voltage
The control voltage of the holding brake in
MS2N holding brakes can be reduced after
executing the switching operation Open brake
by using control modules (e.g. brake control
module HAT02.1-003). By decreasing the con-
trol voltage, energy can be saved of up to 50%
and the self-heating of the motor can be reduced.
To decrease the control voltage of MS2N holding
brakes, the following conditions apply:
•
Maximum decrease of control voltage to U
N
≥
17
V
DC
•
Waiting time after releasing the holding brake
is at least 200 ms
•
Decreasing the control voltage by voltage
control or pulse width modulation with a
PWM cycle frequency ≥ 4 kHz
Refer to the instructions in the control module
documentation.:
Refer to the notes for dimensioning of the cable
length and cable cross-section of brake cables.
Safety technology
The permanent magnet brake of a MS2N motor is
no safety brake. This means, a torque reduction
by non- influenceable disturbance factors can
occur. Especially for use in vertical axes.
About this pr
oduct