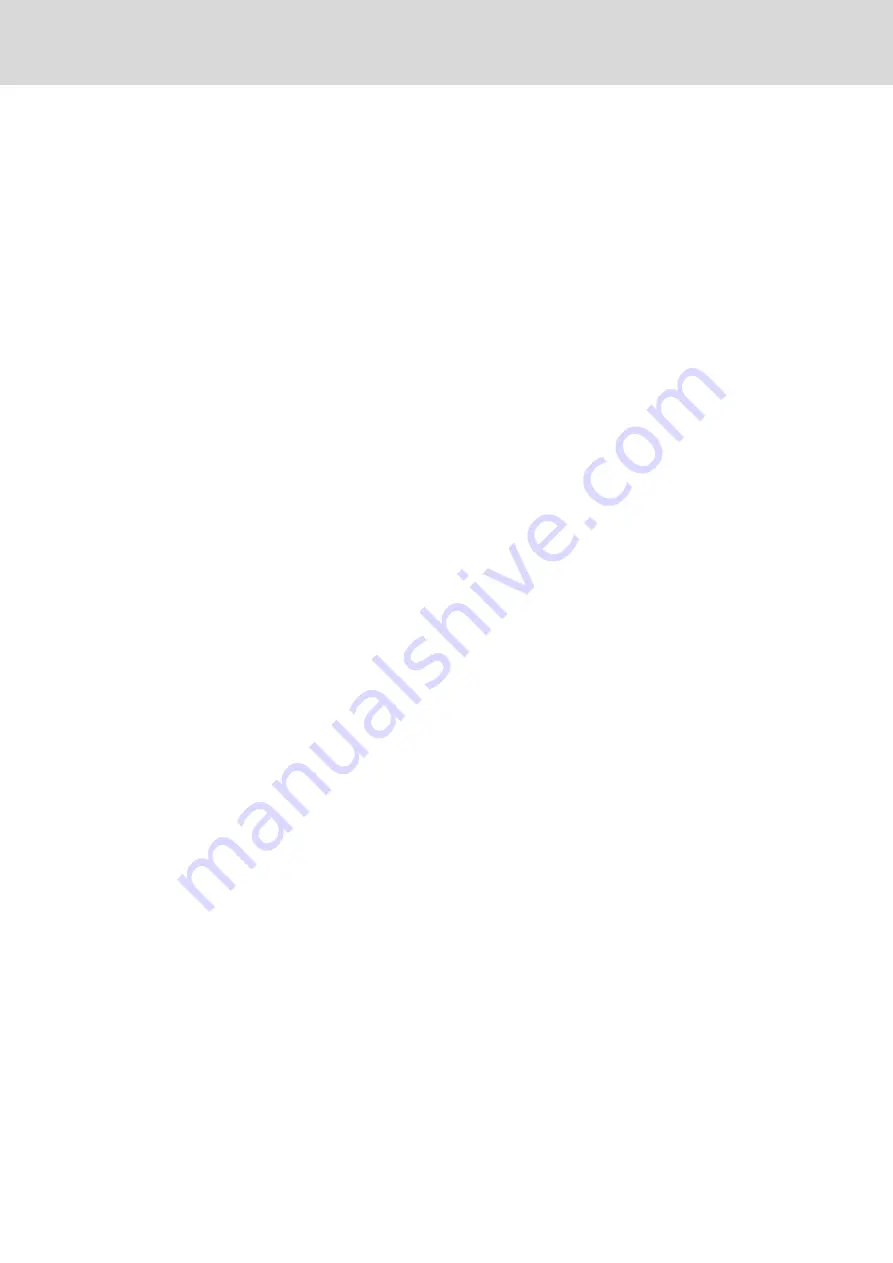
2.
Enter the diameter and the cutting velocity in the provided fields. In this
connection, expressions are allowed (see
). The
order of the entry is of no importance.
3.
Initiate the calculation using the return key or by changing the focus.
4.
If conversion into the other metric system is necessary, activate "Metric
system Inch".
Calculating cutting velocity
The cutting velocity can be calculated in the following way:
1.
Ensure that the metric system suitable for your entries is active. For the
Anglo-American metric system, "Metric system Inch" must be checked.
2.
Enter the diameter and the speed in the provided fields. In this connection,
expressions are allowed. The order of the entry is of no importance.
3.
Initiate the calculation using the return key or by changing the focus.
4.
If conversion into the other metric system is necessary, activate "Metric
system Inch".
Feed Calculations
Calculating the Feed
The feed can be calculated in the following way:
1.
Ensure that the metric system suitable for your entries is active. For the
Anglo-American metric system, "Metric system Inch" must be checked.
2.
Enter the speed. If the speed is not known, it is to be calculated from the
Calculating the Cutting Velocity/Speed
3.
Enter the number of teeth 1 if you want to get the feed per rotation; oth‐
erwise, enter the number of teeth of the tool.
4.
Enter the feed speed.
5.
Initiate the calculation using the return key or by changing the focus.
6.
If conversion into the other metric system is necessary, activate "Metric
system Inch".
Calculating fees velocity
The feed speed can be calculated as follows:
1.
Ensure that the metric system suitable for your entries is active. For the
Anglo-American metric system, "Metric system Inch" must be checked.
2.
Enter the speed. If the speed is not known, it is to be calculated from the
Calculating the Cutting Velocity/Speed
3.
Enter the number of teeth 1 if you know the feed per rotation; otherwise,
enter the number of teeth of the tool.
4.
Enter the feed.
5.
Initiate the calculation using the return key or by changing the focus.
6.
If conversion into the other metric system is necessary, activate "Metric
system Inch".
Errors
Error Causes
Errors are caused in the entry of values and/or expressions. The following cau‐
ses can be considered:
●
Inadmissible mathematical operations,
●
Syntax errors and
●
exceedance of a value range.
Error display
In the lower part of the form, an error message appears, either with reference
to the violated value range or as format error. The focus is automatically reset
to the faulty entry field.
Bosch Rexroth AG
DOK-MTX***-NC*OP***V11-AP01-EN-P
Rexroth IndraMotion MTX 11VRS Standard NC Operation
286/301
Extended Functionality
Содержание Rexroth IndraMotion MTX 11 VRS
Страница 1: ...Electric Drives and Controls Pneumatics Service Linear Motion and Assembly Technologies Hydraulics ...
Страница 14: ...Bosch Rexroth AG DOK MTX NC OP V11 AP01 EN P Rexroth IndraMotion MTX 11VRS Standard NC Operation 12 301 ...
Страница 26: ...Bosch Rexroth AG DOK MTX NC OP V11 AP01 EN P Rexroth IndraMotion MTX 11VRS Standard NC Operation 24 301 ...
Страница 36: ...Bosch Rexroth AG DOK MTX NC OP V11 AP01 EN P Rexroth IndraMotion MTX 11VRS Standard NC Operation 34 301 ...
Страница 76: ...Bosch Rexroth AG DOK MTX NC OP V11 AP01 EN P Rexroth IndraMotion MTX 11VRS Standard NC Operation 74 301 ...
Страница 114: ...Bosch Rexroth AG DOK MTX NC OP V11 AP01 EN P Rexroth IndraMotion MTX 11VRS Standard NC Operation 112 301 ...
Страница 160: ...Bosch Rexroth AG DOK MTX NC OP V11 AP01 EN P Rexroth IndraMotion MTX 11VRS Standard NC Operation 158 301 ...
Страница 290: ...Bosch Rexroth AG DOK MTX NC OP V11 AP01 EN P Rexroth IndraMotion MTX 11VRS Standard NC Operation 288 301 ...
Страница 294: ...Bosch Rexroth AG DOK MTX NC OP V11 AP01 EN P Rexroth IndraMotion MTX 11VRS Standard NC Operation 292 301 ...
Страница 303: ...Notes DOK MTX NC OP V11 AP01 EN P Rexroth IndraMotion MTX 11VRS Standard NC Operation Bosch Rexroth AG 301 301 ...