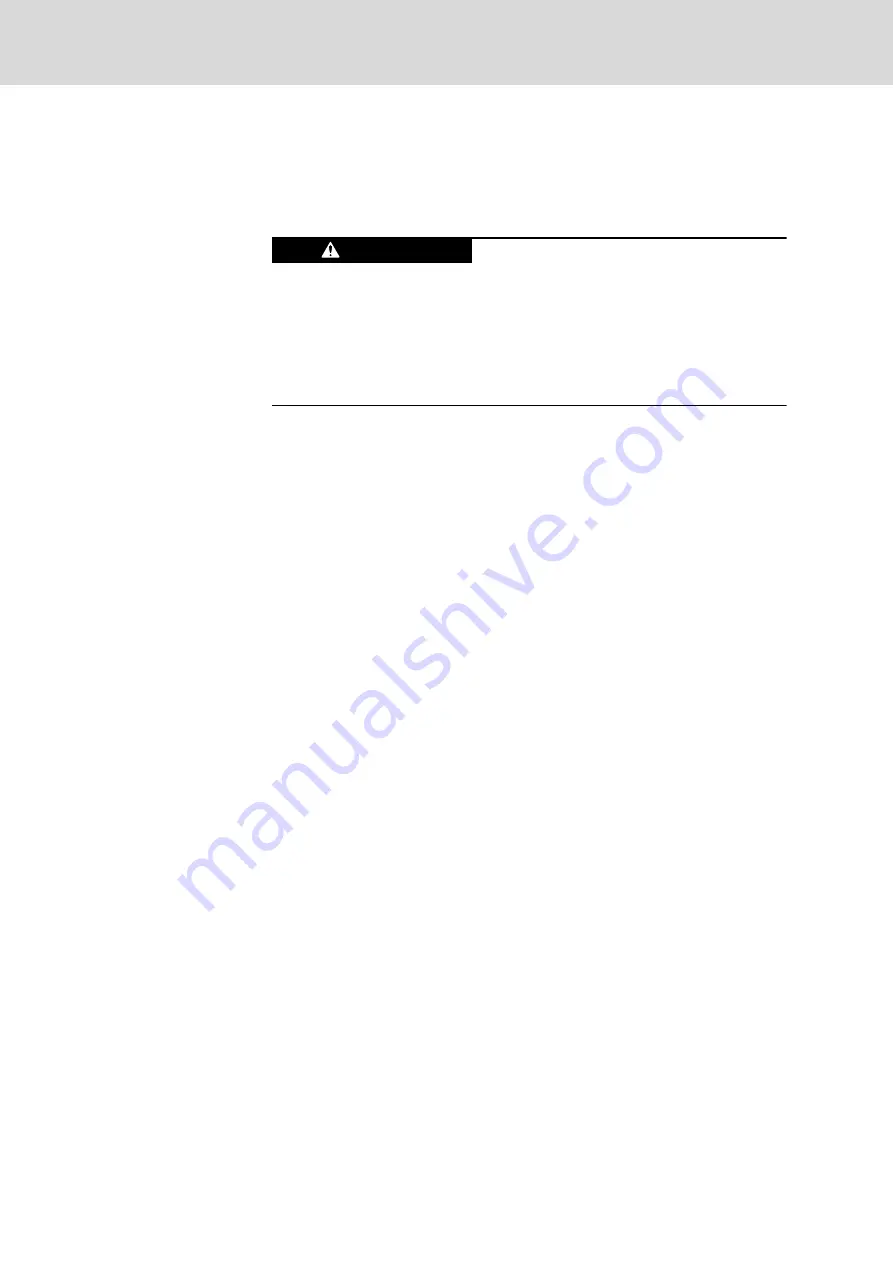
Project planning recommendation
In order to ensure plant safety, the holding torque required by the application
must be reduced to 60% of the static holding torque (M4) of the holding
brake.
10.10.4 Holding brake - commissioning and maintenance instructions
Danger of life or material damage, danger of
explosion due to inappropriate use!
WARNING
●
Any commissioning and maintenance works must only be carried out in
non-explosive environments. The environment must be free from explo‐
sive gas or dust.
●
Before commissioning and maintance works are carried out, the rooms
are to be ventilated, if applicable, in order to remove any existing explo‐
sive gas.
To ensure the function of the holding brake, the holding brake must be
checked before commissioning the motors. The check and, if necessary, the
loop-in can be carried out "mechanically by hand" or "automatically by soft‐
ware function".
Manual check and loop-in of the
holding brakes
Measure the holding torque (M4) of the holding brake, if necessary loop in
the holding brake.
Measure the holding torque (M4) of the holding brake
1.
Disconnect the motor from the power supply and secure it against being
switched on again.
2.
Measure the transferable holding torque (M4) of the holding brake with a
torque wrench. Holding torque (M4): see technical data.
When the specified holding torque (M4) is reached, the motor is ready
for installation.
If the specified holding torque (M4) is not reached, the holding torque
can be restored by the subsequent loop-in process.
Looping in the holding brake
1.
With the holding brake closed, turn the output shaft approx. 5 turns by
hand, for example with a torque wrench.
2.
Measure holding torque (M4).
When the specified holding torque (M4) is reached, the motor is ready
for installation.
If the specified holding torque (M4) is not reached after several loops,
the holding brake is not functional. Please contact the service of
Rexroth.
Check and loop-in of the holding
brakes via software function
Check holding torque (M4) by command Holding system check
P-0-0541, C2100
1.
The effectiveness of the holding brake and the open state is checked by
the drive controller by starting the routine "P-0-0541, C2100 command
Holding system check".
If the holding brake is OK, the drive is ready for operation after the rou‐
tine has expired. If the braking torque is too low, the drive control unit
issues a corresponding message.
Bosch Rexroth AG
DOK-MOTOR*-MSK*EXGIIK3-PR09-EN-P
134/175
Synchronous Servomotors MSK For Potentially Explosive Areas
Operating conditions and application notes
Содержание MSK030B NSNN Series
Страница 110: ...Bosch Rexroth AG DOK MOTOR MSK EXGIIK3 PR09 EN P 108 175 Synchronous Servomotors MSK For Potentially Explosive Areas ...
Страница 142: ...Bosch Rexroth AG DOK MOTOR MSK EXGIIK3 PR09 EN P 140 175 Synchronous Servomotors MSK For Potentially Explosive Areas ...
Страница 146: ...Bosch Rexroth AG DOK MOTOR MSK EXGIIK3 PR09 EN P 144 175 Synchronous Servomotors MSK For Potentially Explosive Areas ...
Страница 152: ...Bosch Rexroth AG DOK MOTOR MSK EXGIIK3 PR09 EN P 150 175 Synchronous Servomotors MSK For Potentially Explosive Areas ...
Страница 166: ...Bosch Rexroth AG DOK MOTOR MSK EXGIIK3 PR09 EN P 164 175 Synchronous Servomotors MSK For Potentially Explosive Areas ...
Страница 172: ...Bosch Rexroth AG DOK MOTOR MSK EXGIIK3 PR09 EN P 170 175 Synchronous Servomotors MSK For Potentially Explosive Areas ...
Страница 174: ...Bosch Rexroth AG DOK MOTOR MSK EXGIIK3 PR09 EN P 172 175 Synchronous Servomotors MSK For Potentially Explosive Areas ...