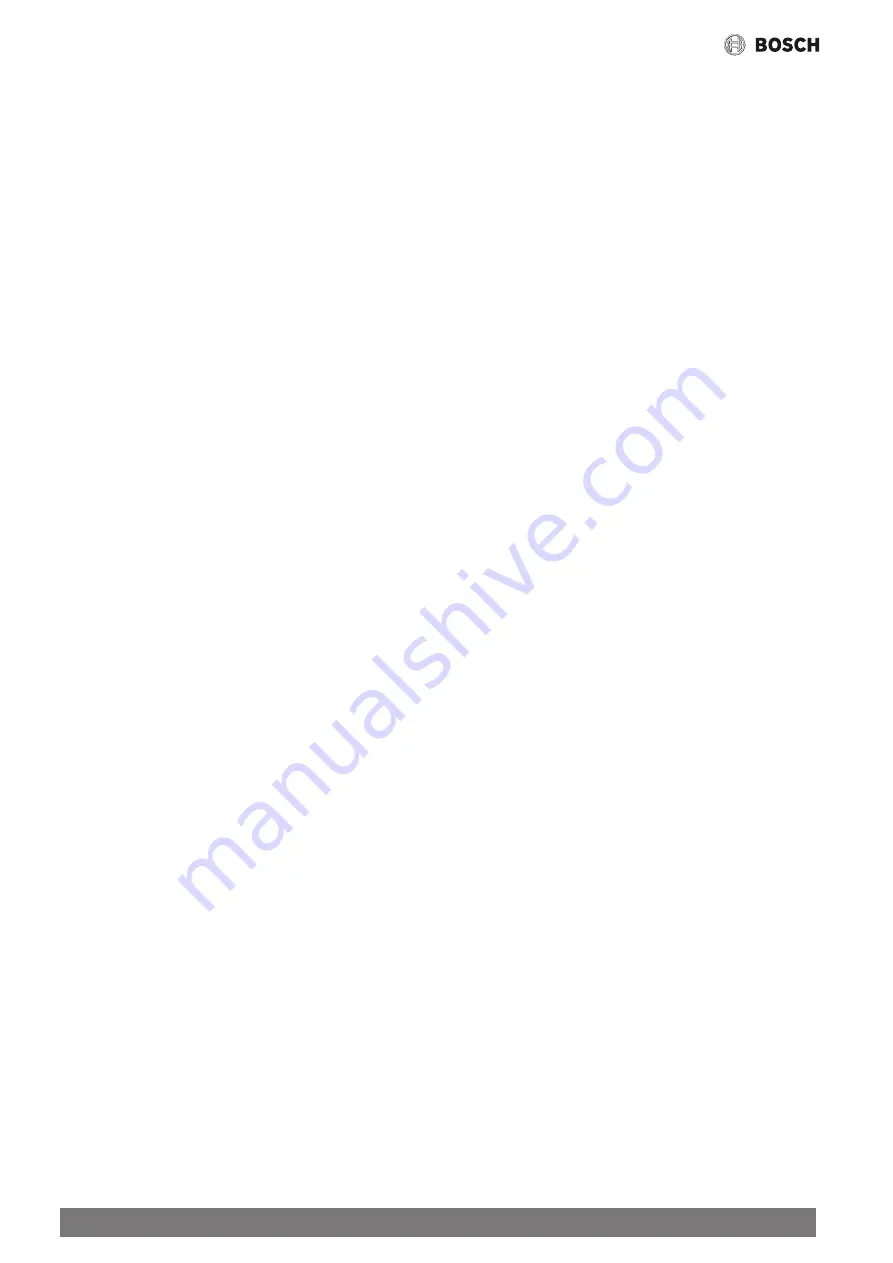
26
Climate 5000 – 6720886909 (2018/04)
Information Servicing
13. Detection of flammable refrigerants
Under no circumstances should potential sources of ignition be used
when searching for or detecting refrigerant leaks. A halide torch (or any
other detector using a naked flame) must not be used.
14. Leak detection methods
The following leak detection methods are deemed acceptable for
systems containing flammable refrigerants. Electronic leak detectors
must be used to detect flammable refrigerants, but the sensitivity may
not be adequate or may need re-calibration. (Detection equipment
must be calibrated in a refrigerant-free area.) Ensure that the detector
is not a potential source of ignition and is suitable for the refrigerant.
Leak detection equipment must be set at a percentage of the LFL of
the refrigerant and must be calibrated to the refrigerant employed and
the appropriate percentage of gas (25% maximum) is confirmed. Leak
detection fluids are suitable for use with most refrigerants, but the use
of detergents containing chlorine should be avoided, since the chlorine
may react with the refrigerant and corrode the copper pipe-work.
If a leak is suspected, all naked flames should be removed or
extinguished. If a leakage of refrigerant is found which requires brazing,
all of the refrigerant must be recovered from the system or isolated (by
means of shut off valves) in a part of the system remote from the leak.
Oxygen-free nitrogen (OFN) must then be purged through the system
both before and during the brazing process.
15. Removal and evacuation
When breaking into the refrigerant circuit to make repairs for any
other purpose, conventional procedures must be used, However, it
is important that best practice is followed, since flammability is a
consideration. The following procedure must be adhered to:
•
remove refrigerant;
•
purge the circuit with inert gas;
•
evacuate;
•
purge again with inert gas;
•
open the circuit by cutting or brazing.
The refrigerant charge should be recovered into the correct recovery
cylinders. The system should be flushed with OFN to render the unit safe.
It may be necessary to repeat this process several times. Compressed
air or oxygen must not be used for this task.
Flushing should be achieved by breaking the vacuum in the system
with OFN and continuing to fill until the working pressure is achieved,
then venting to atmosphere and finally pulling down to a vacuum. This
process must be repeated until no refrigerant is within the system.
When the final OFN charge is used, the system must be vented down
to atmospheric pressure to enable work to take place. This operation is
absolutely vital if brazing operations on the pipe-work are to take place.
Ensure that the outlet for the vacuum pump is not close to any ignition
sources and ventilation is available.
16. Charging procedures
In addition to conventional charging procedures, the following
requirements must be followed:
•
Ensure that contamination of different refrigerants does not occur
when using charging equipment. Hoses or lines should be as short
as possible to minimize the amount of refrigerant contained in them.
•
Cylinders must be kept upright.
•
Ensure that the refrigeration system is earthed prior to charging the
system with refrigerant.
•
Label the system when charging is complete (if not already).
•
Extreme care should be taken not to overfill the refrigeration
system.
•
Prior to recharging the system it must be pressure tested with OFN.
The system must be leak tested on completion of charging but prior
to commissioning. A follow-up leak test must be carried out prior to
leaving the site.
17. Decommissioning
Before carrying out this procedure, it is essential that the technician
is completely familiar with the equipment and all its detail. It is
recommended good practice that all refrigerants are recovered safely.
Prior to the task being carried out, an oil and refrigerant sample must
be taken.
If analysis is required prior to re-use of reclaimed refrigerant, it is
essential for electrical power to be available before commencing the
task.
a. Become familiar with the equipment and its operation.
b. Isolate system electrically
c. Before attempting the procedure ensure that:
•
mechanical handling equipment is available, if required, for han-
dling refrigerant cylinders;
•
all personal protective equipment is available and is being used
correctly;
•
the recovery process is supervised at all times by a competent
person;
•
recovery equipment and cylinders conform to the appropriate
standards.
d. Pump down refrigerant system, if possible.
e. If a vacuum is not possible, make a manifold so that refrigerant can
be removed from various parts of the system.
f. Make sure that the cylinder is situated on the scales before recovery
takes place.
g. Start the recovery machine and operate in accordance with
manufacturer’s instructions.
h. Do not overfill cylinders. (No more than 80% volume liquid charge).
i. Do not exceed the maximum working pressure of the cylinder, even
temporarily.
j. When the cylinders have been filled correctly and the process
completed, make sure that the cylinders and the equipment are
removed from site promptly and all isolation valves on the equipment
are closed off.
k. Recovered refrigerant must not be charged into another refrigeration
system unless it has been cleaned and checked.
18. Labelling
Equipment must be labelled stating that it has been de-commissioned
and emptied of refrigerant. The label must be dated and signed. Ensure
that there are labels on the equipment stating that the equipment
contains flammable refrigerant.
19. Recovery
•
When removing refrigerant from a system, either for service or
decommissioning, it is recommended good practice that all refriger-
ants are removed safely.
•
When transferring refrigerant into cylinders, ensure that only appro-
priate refrigerant recovery cylinders are employed. Ensure that the
correct numbers of cylinders for holding the total system charge are
available. All cylinders to be used are designated for the recovered
refrigerant and labelled for that refrigerant (i.e special cylinders
for the recovery of refrigerant). Cylinders should be complete with
pressure relief valve and associated shut-off valves should be in
good working order.
•
Empty recovery cylinders are evacuated and cooled before recovery
occurs, if possible.