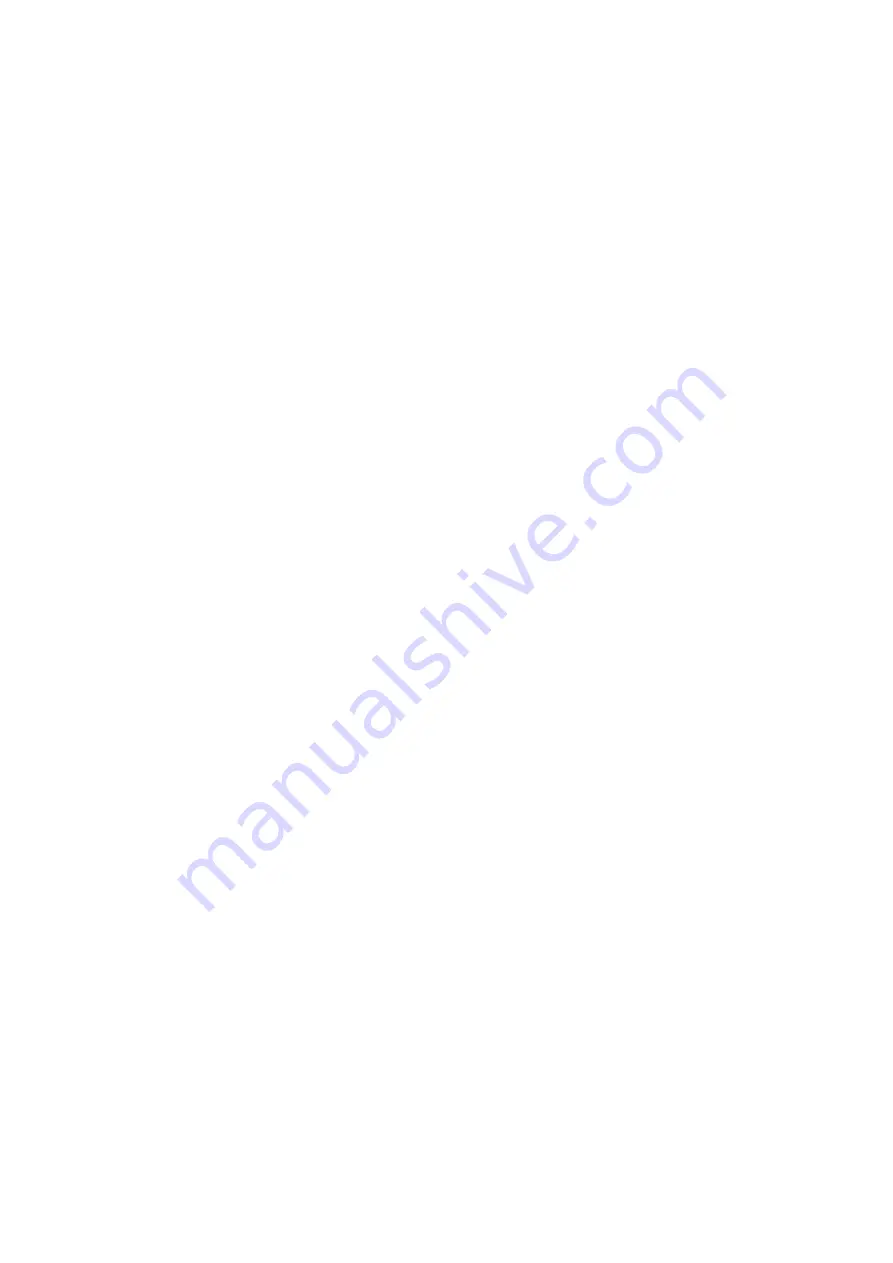
7
www.BormannTools.com
To make sure that the rubber packing of the water collector pad is in perfect condition in order to eliminate the leakage of the
drained water.
Boring/Drilling Operation
Ensure that the machine is securely placed. Install the selected diamond core bit onto the drive spindle and connect the water
hose to water cock on the machine. Switch on the machine under no-load condition, turn on the water cock and start drilling
gently when water flows out from the core bit. Slowly advance the diamond core bit at beginning otherwise the core bit may be
vibrated. After drilling depth reaches 5 mm. apply pressure for constant cutting. When the turning speed of the motor drops
obviously in drilling operation
It means the motor is overloaded, properly decrease the feed pressure immediately. If fumes or
peculiar smells be noted in drilling operation, switch off the machine immediately for a rest to avoid the motor be overloaded and
burned out.
CAUTION:
Steady even pressure assures true running, accurate holes, and longer bit lite. A constant bit speed must be maintained at all
times and should be applied.so the bit is constantly cutting.
Overload will damage the motor and the diamond core bit insufficient pressure will polish the diamond core bit, reducing the
drilling efficiency.
Material to Be Drilled
CAUTION:
In drilling it is most important to understand the object material to be drilled. Materials such as sand gravel and broken stone are
usually used for concrete and asphalt. The grain size of mixture and the mixing ratio of the sand materials greatly affect drilling.
Different material characteristics (concrete, steel-reinforced concrete, porous or solid masonry) require different and varying feed
pressures on the diamond core bit.
When steel reinforcing rods are encountered while drilling in steel reinforced concrete, the current will be increased suddenly
which may cause vibration of the motor, decrease the feed pressure to maintain e constant turning speed or the diamond core bit
may be damaged. When drilling in poor quality of concrete with sand, gravel and steel piece, the diamond core bit may be blocked
with instantaneous overload of the machine and automatically break of the switch caused by overcurrent. Shut down the machine
immediately and free the' diamond core bit Restart the drilling operation after dressing the core bit.
When woodblocks, thick asphalt layers or asphalt feels are encountered in drilling operation. The current will also be increased,
decrease the feed pressure and drill gently
Removal of the Drilling Core
Take care to slow the feed rate before the core bit drilling through ceilings, walls, etc. to avoid the drilling core be blocked in the
diamond core drilling crown and difficult to be taken out. If the drilling core remains hanging in the diamond core drilling crown
after the core-drilling operation is complete, the bit must be unscrewed from the drive spindle and be flushed with water to
remove scraps, and then the drilling core can be knocked out with a wood rod.
If the core-drilling operation does not penetrate fully, the drilling core can be broken up by inserting a tool such as a chisel into the
drilling gap. If the drilling core cannot be secured, use a tool such as a hammer drill to make an angled hole into the drilling core,
and insert a rod to extract it
Caution:
When carrying out vertical drilling, e.g.in a ceiling, note that the drilling core normally drops out as soon as the hole is completed.
Take appropriate steps to ensure that personal injury or material damage does not result. Never hit the casing of the drilling core
with a metal item such as a hammer or wrench in order to loosen the drilling core. This will cause the casing pipe to become
dented, which will make blocking of the drilling core even more likely on future occasions. The diamond core drilling crown may
then be rendered unusable.
Take care not to damage the diamond core bit when removing the drilling core.
Clearance Adjustment
Avoid the machine be vibrated in drilling operation. When the clearance between the feed slider and the rack (the column)
becomes larger, vibration will be occurred. Check the clearance adjusting screws to determine whether they are loose and adjust
the clearance property by tightening the clearance adjusting screws. The are two clearance using screws on the feed slider both
above the handle grip and another two on the left side of the feed slider
Maintenance and inspection
Caution:
Always be sure that the machine is switched off and unplugged before attempting to perform inspection or maintenance.
Содержание 022190
Страница 1: ...BDD1600 Owner s manual Art Nr 022190 www BormannTools com...
Страница 2: ...2 www BormannTools com GB 1 2 3 Off 4...
Страница 4: ...4 www BormannTools com 1 2 3 7 5 9 11 6 12 1...
Страница 5: ...5 www BormannTools com...
Страница 6: ...6 www BormannTools com ON OFF 5 mm...
Страница 7: ...7 www BormannTools com 15...
Страница 8: ...8 www BormannTools com 500V 7 M...
Страница 9: ...9 www BormannTools com 44 Nm 47 Nm Service 220 240V 50HZ 2380W 160MM 0 1401RPM...