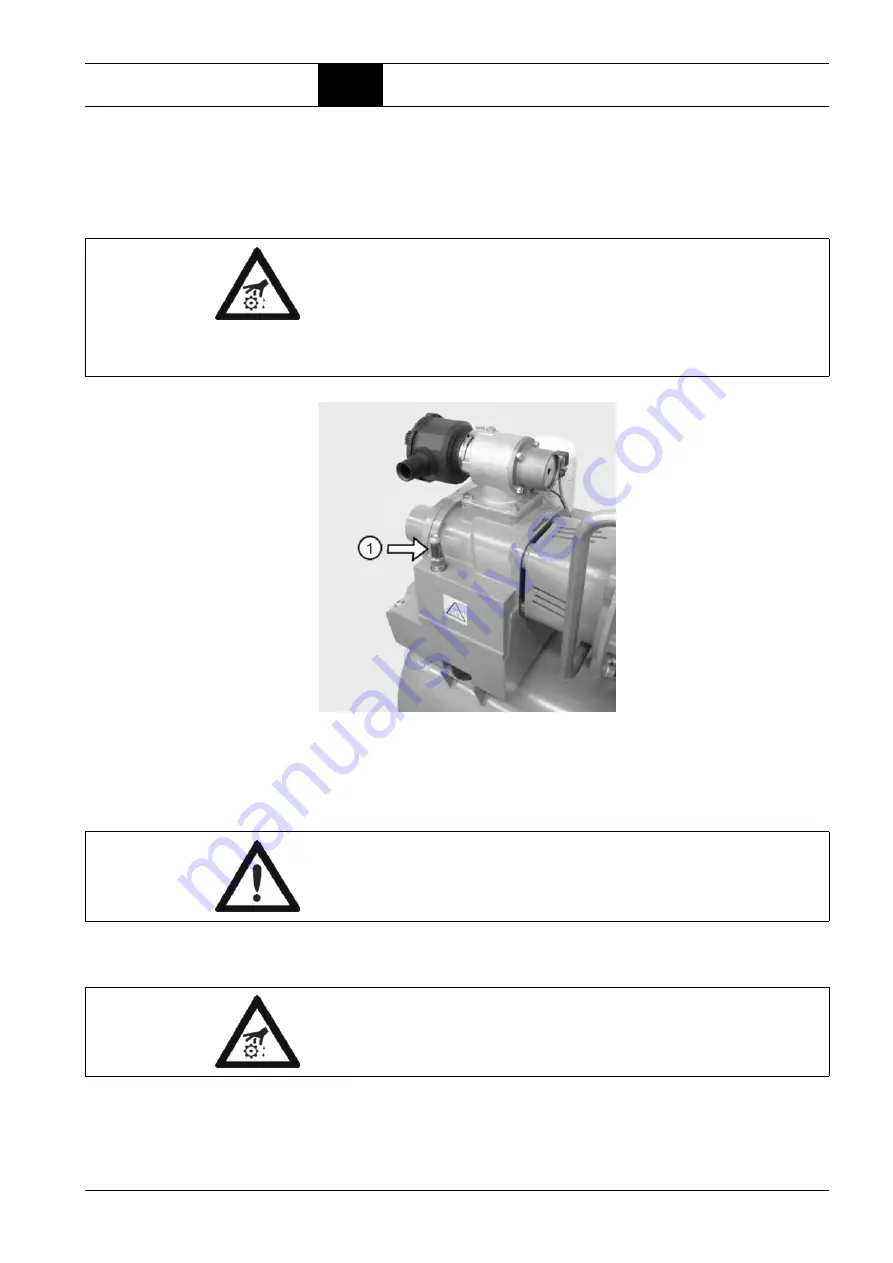
BOGE Operating instructions for C 10 L...C 20 L series screw compressors
Page 45
Maintenance
5.3
Regular maintenance work
Checking the safety
valve
Check:
–
After approx. 3,000 operating hours, however, at least once a year.
Check safety valve by opening the screw plug (1).
Fig. 5.9: Check safety valve
Nozzle with dirt catch
Change:
–
After 3,000 operating hours, however, no later than after one year.
–
Switch off the compressor using the OFF button.
Caution: Risk of injury!
Danger of burning due to hot oil!
Take extreme care when checking the safety valve with the compressor run-
ning taking all safety measures into consideration.
Always wear safety gloves!
A hot air-oil mixture escapes when opening!
–
Open the threaded plug
(1) counterclockwise. The
air-oil mixture escapes.
–
Tighten the threaded plug
by turning clockwise.
Attention!
If the prescribed maintenance intervals are not complied with, the residual oil
content in the compressed air rises considerably.
Caution: Risk of injury!
Press Emergency Stop button, open mains disconnection device and secure
against unintentional switch on by means of a padlock.