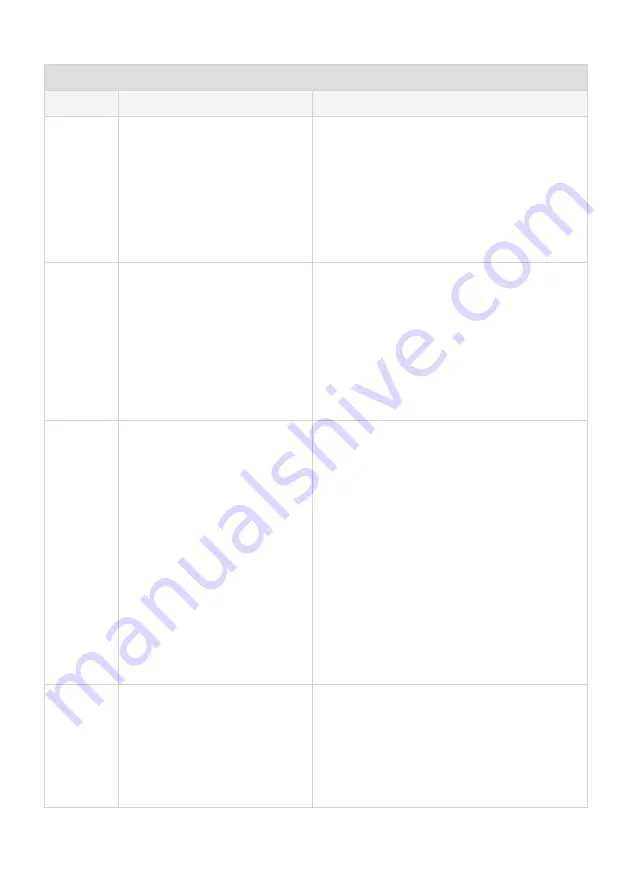
26
Troubleshooting guide
Problem
Cause
Solution
Excessive
electrode
consumption
1. Inadequate gas flow
2. Improper size electrode for
current required
3. Operating of reverse polarity
4. Electrode contamination
5. Excessive heating inside torch
6. Electrode oxidising during cooling
7. Shield gas incorrect
1. Increase gas flow
2. Use larger electrode
3. User larger electrode or change polarity
4. Remove contaminated portion, then prepare again
5. Replace collet. Try wedge collet or reverse collet.
6. Increase gas flow post time to 1 sec per 10 amps
7. Change to proper gas (no oxygen or CO
2
)
Erratic Arc
1. Incorrect voltage (arc too long)
2. Current too low for electrode size
3. Electrode contaminated
4. Joint too narrow
5. Contaminated shield gas. Dark
stains on the electrode or weld
bead indicate contamination
6. Base metal is oxidised, dirty or oily
1. Maintain short arc length
2. Use smaller electrode or increase current
3. Remove contaminated portion, then prepare again
4. Open joint groove
5. The most common cause is moisture or aspirated
air in gas stream. Use welding grade gas only. Find the
source of the contamination and eliminate it promptly.
6. Use appropriate chemical cleaners, wire brush, or
abrasives prior to welding
Inclusion of
tungsten or
oxides in
weld
1. Poor lift starting technique
2. Excessive current for tungsten size
used
3. Accidental contact of electrode with
puddle
4. Accidental contact of electrode to
filler rod
5. Using excessive electrode extension
6. Inadequate shielding or excessive
drafts
7. Wrong gas
8. Heavy surface oxides not being
removed
1. Many codes do not allow scratch starts. Use copper
strike plate.
2. Reduce the current or use larger electrode
3. Maintain proper arc length
4. Maintain a distance between electrode and filler metal
5. Reduce the electrode extension to recommended
limits
6. Increase gas flow, shield arc from wind, or use gas lens
7. Do not use ArO
2
or ArCO
2
GMAW (MIG) gases
for TIG welding
8. Joint area needs to be cleaned prior to welding
Porosity
in Weld
Deposit
1. Entrapped impurities, hydrogen, air,
nitrogen, water vapour
2. Defective gas hose or loose
connection
3. Filler material is damp (particularly
aluminium)
4. Filler material is oily or dusty
1. Do not weld on wet material. Remove condensation
from line with adequate gas pre-flow time
2. Check hoses and connections for leaks
3. Dry filler metal in oven prior to welding
4. Replace filler metal
Содержание Smootharc MMA 170
Страница 1: ...Smootharc MMA 170 O P E R AT I N G M A N U A L...
Страница 34: ...34...
Страница 35: ...35...