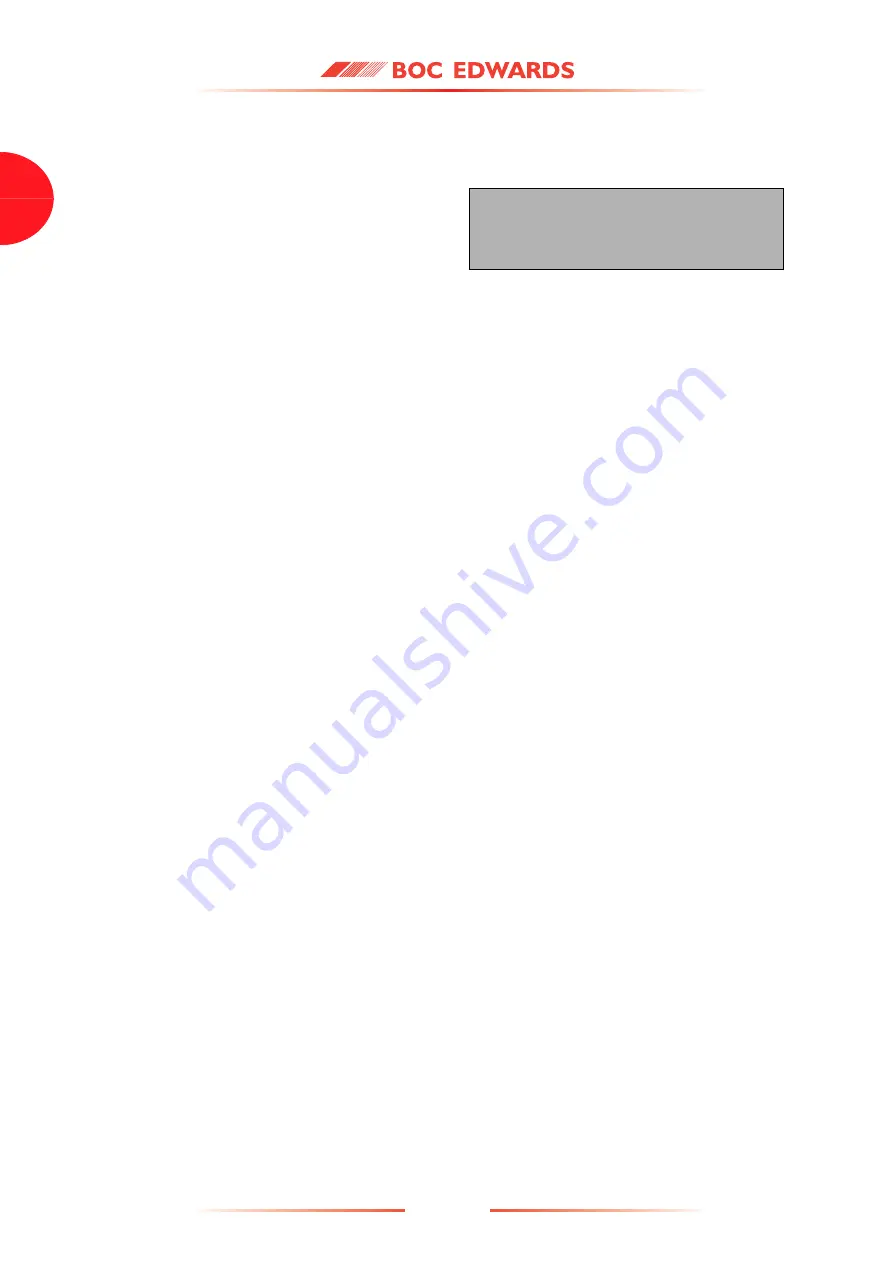
Issue A
Nov 02
PAGE
26
XDS Dry Pump
MAINTENANCE
26
11. The fixed scroll tip seal must be cut into 2
sections and the orbiting scroll tip seal must be
cut into 3 sections. Each scroll tip seal groove
has indicator marks to show where the tip seal
must be cut (refer to Figure 10).The seals have
a sealing face and the opposite face has minute
grooves. Ensure that the grooved side of the
seal is fitted downwards into the scroll, so that
the sealing face is upwards. Start at the centre
of the orbiting scroll and fit the seal into the
groove (refer to Figure 9). The seal should be as
close to the end of the groove as possible.
When the indicator mark is reached, cut the
seal to the mark. This allows an area into which
the seal can expand. Repeat for all sections in
both scrolls. Ensure that the tip seal is pushed
fully home, particularly at the pinch-points, with
finger pressure before reassembly.
12. Reassemble, making sure that the tip seals do
not fall out. Reconnect the fan connector, then
refit the fixed scroll assembly taking care to
tighten the six fixing screws progressively and
evenly.
13. Some period of running-in may be required
before optimum performance is reached.
Depending on the application, the vacuum
achieved directly following a tip seal
replacement may be sufficient for your
requirements. Typically, this can be up to a
decade more than the final vacuum achievable
with a bedded in tip seal. During run in, deposits
of tip seal dust will be produced. Ensure the
exhaust is connected to a silencer or an exhaust
line to collect tip seal deposit, refer to
Section 7.3.2 for further information. If
possible, occasional venting through the gas
ballast control or valve on the inlet is
recommended.
5.7
Test the motor condition
Test the earth continuity and the insulation
resistance of the pump motor, in accordance with
local regulations for the periodic testing of electrical
equipment.
We recommend that the earth continuity is less
than 0.1
Ω
and the insulation resistance is greater
than 2M
Ω
. (Reference EN61010-1).
If the pump fails these tests, you must contact BOC
Edwards
.
5.8
Fault-finding
5.8.1
The pump has failed to start or has
stopped
• The electrical supply fuse has blown.
• The electrical supply voltage does not match
that for which the inverter input has been
configured.
• The inverter drive has not reset after an over
temperature event. Disconnect the mains
supply and wait for at least one minute and
attempt to restart.
• The motor is faulty.
• Fan not working or not connected.
• The ambient temperature is too high.
• The cooling air supply is insufficient or is too
hot.
• The process gas is too hot or the throughput
is too high.
CAUTION
Do not flash test the XDS35i or damage to the
inverter may result.
Содержание A730-01-983
Страница 2: ......
Страница 6: ...Issue A Nov 02 XDS Dry Pump PAGE iv iv This page intentionally blank ...
Страница 10: ...Issue A Nov 02 XDS Dry Pump PAGE 4 4 This page intentionally blank ...
Страница 14: ...Issue A Nov 02 XDS Dry Pump PAGE 8 8 This page intentionally blank ...
Страница 16: ...Issue A Nov 02 PAGE 10 XDS Dry Pump INSTALLATION 10 Figure 3 Installation drawing ...
Страница 20: ...Issue A Nov 02 XDS Dry Pump PAGE 14 14 This page intentionally blank ...
Страница 31: ...Nov 02 Issue A XDS Dry Pump MAINTENANCE PAGE 25 25 Figure 10 Tip seal length adjustment 1 Tip seals trim point ...
Страница 34: ...Issue A Nov 02 XDS Dry Pump PAGE 28 28 This page intentionally blank ...
Страница 36: ...Issue A Nov 02 XDS Dry Pump PAGE 30 30 This page intentionally blank ...
Страница 40: ...Issue A Nov 02 XDS Dry Pump PAGE 34 34 This page intentionally blank ...
Страница 43: ...This page intentionally blank ...