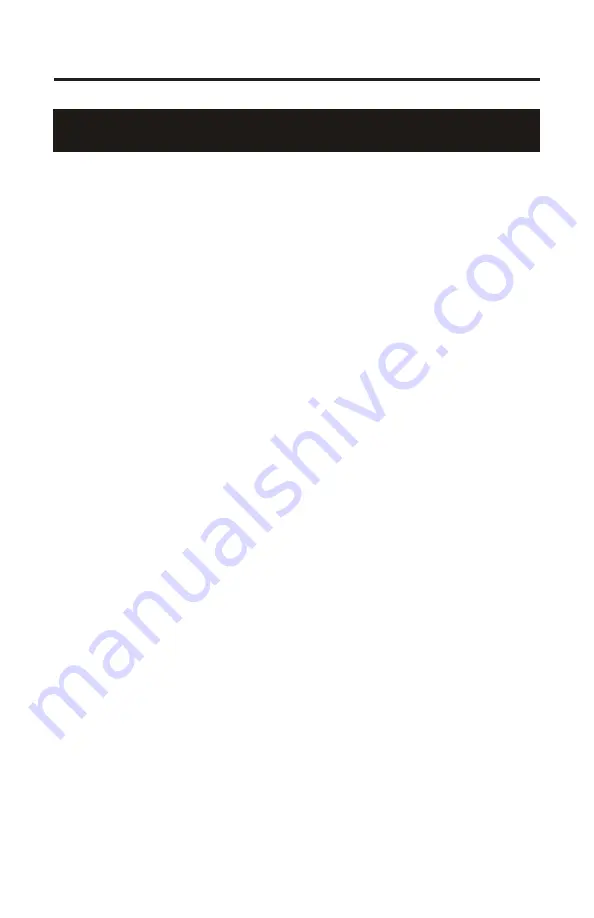
Page 14
7.0 How to Maintain the Pump
7.1 Routine Inspection and Maintenance
The pump requires very little maintenance. However, the pump and all
accessories should be checked regularly. This is especially important when
pumping chemicals. Inspect all components for signs of leaking, swelling,
cracking, discoloration or corrosion. Replace worn or damaged components
immediately.
Cracking, crazing, discoloration and the like during the first week of
operation are signs of severe chemical attack. If this occurs, immediately
remove the chemical from the pump. Determine which parts are being
attacked and replace them with parts that have been manufactured using
more suitable materials. The manufacturer does not assume responsibility
for damage to the pump that has been caused by chemical attack.
7.2 How to Clean the Pump
The pump will require occasional cleaning, especially the Injection fitting,
the Footvalve/Strainer, and the pump head valves. The frequency will
depend on the type and severity of service.
]
Inspect and replace the pumphead valves as required.
]
When changing the diaphragm, the pump head chamber and pump head
cover should be wiped free of any dirt and debris.
]
Periodically clean the injection/check valve assembly, especially when
injecting fluids that calcify such as sodium hypochlorite. These lime
deposits and other build ups can clog the fitting, increase the back pressure
and interfere with the check valve operation. See page 8.
]
Periodically clean the suction strainer. See page 8.
]
Periodically inspect the air vents located under the motor housing and in
the back on the rear housing cover. Clean if necessary.
CAUTION: Proper eye and skin protection must be
worn when installing and servicing the pump.
CAUTION: Proper eye and skin protection must be
worn when installing and servicing the pump.
7.3 Measuring the Pump’s Output - Volumetric Test.
This volumetric test will take into account individual installation factors
such as line pressure, fluid viscosity, suction lift, etc. This test is the most
accurate for measuring the injector’s output in an individual installation.
1.
Be sure the Injection Fitting and Footvalve/Strainer is clean and working
properly.
2.
Fill a large graduated cylinder with the solution to be injected.
3.
With the pump installed under normal operating conditions, place the
suction tubing with the Footvalve/Strainer installed in the graduated
cylinder.
4.
Run the pump until all air is removed from the suction line and the solution
C-1100