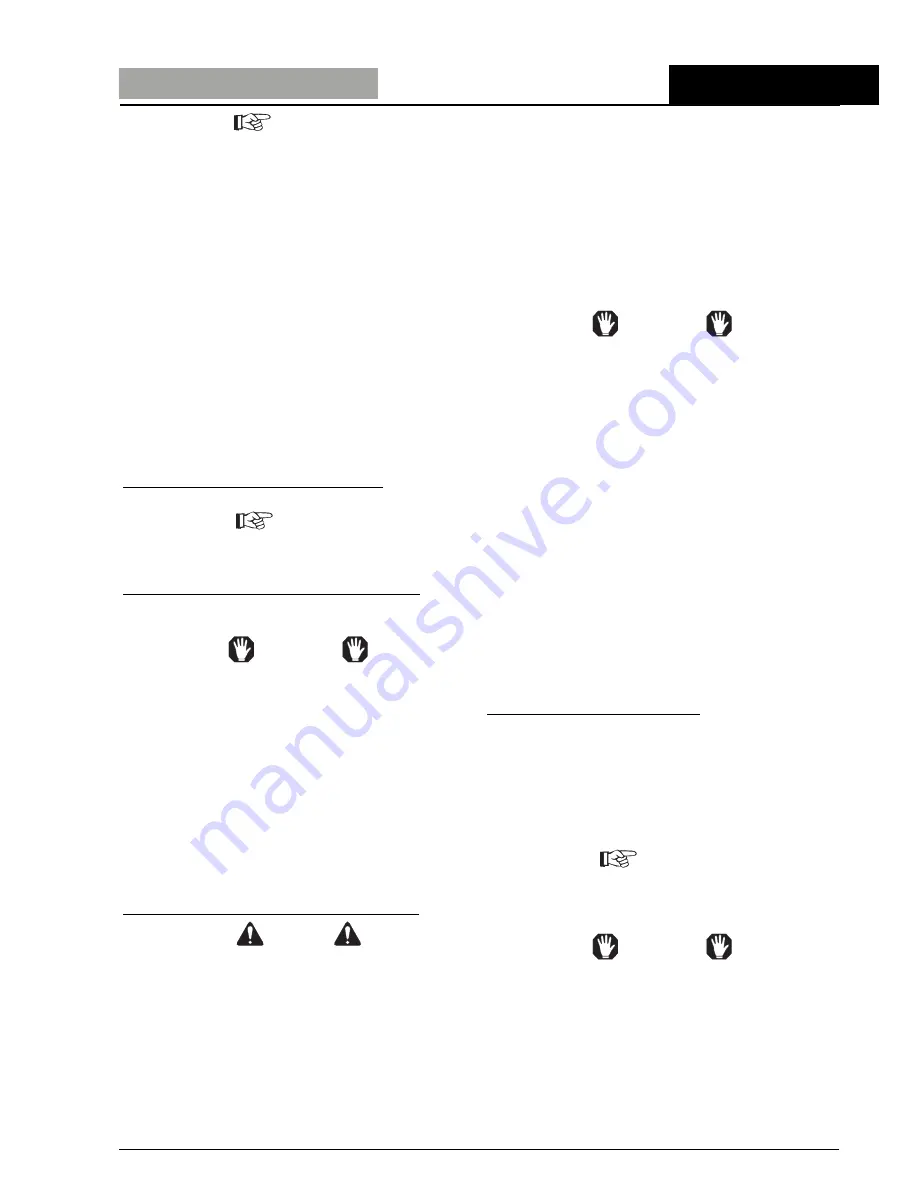
15
ENGLISH
IMPORTANT
Every operation of installation, electrical or hydraulic
connection, programming, maintanance etc...has to be
carried out by QUALIFIED personnel, authorised by the
manufacturer;
any interventions carried out by UNQUALIFIED
personnell, may compromise the technician’s own safety,
as well as the safety of other personnel (operators, etc.)
or of any other equipment connected to the washing
machine.
The manufacturer declines all responsibility for
accidents or damage to persons or property caused
by failure to comply with the above listed provisions.
3.1
INSTALLATION (Fig. 6-7)
-
After having removed the packing, make sure that the
machine is in a perfect condition and that all the parts
have been included.
-
Position the machine in the required setting.
3.1.a Connecting the drain pipe (Fig. 6)
-
Fix the drain pipe (11) to the relative preset outlet.
IMPORTANT
It is essential to ensure that the drain pipe that it is not
throttled in any part.
3.1.b Connection to the water main (Fig. 6-7)
-
Screw the end of the fill pipe (12) to a 3/4”G threaded
cock, fitting the filter (13 Fig. 7) in between.
ATTENTION
It is essential to connect the cold water delivery pipe to a
throttle cock in order to separate the water main from the
machine itself. Also make sure that there are no sharp
bends.
If there is sand in the water main, it will be necessary to
install a filter between it and the machine. If the water main
is without, it is advisable to install a decalcifier prior to the
machine with a setting of min. 4 and max. 8 French
degrees.
The manufacturer declines all responsibility for
damage to the machines caused by failure to comply
with the above listed provisions.
3.1.c Connection to the water main (Fig. 6-7)
DANGER
-
Before connecting to the electricity main, always
check that the data pertaining to the power source
correspond to those indicated on the identification
plate (pos. 9 Fig. 5) and that the main electric power
switch installed prior to the machine is
disconnected “0” OFF.
-
An appropriately sized omnipolar circuit-breaker
with a minimum 3 mm gap between its contacts
must be installed between the power supply main
and the machine.
-
The manufacturer declines all responsibility for
accidents or damage to persons or property caused
by failure to comply with the above listed provisions.
•
Connect the electrical power cable (14) to the main
switch installed prior to the machine.
•
Connect the equipotential ground conductor to the
terminal (15).
3.2
DETERGENT DISPENSER (Optional)
(Fig. 8)
The machine is equipped with an automatic detergent
dispenser.
•
Insert the red supply tube (16) into the canister (17).
ATTENTION
Always wash the hands under running water if they come
into contact with detergent, or comply with the specific
indications pertaining to the utilized type of detergent
itself.
•
Proceed with a few no-load cycles until the intake and
delivery tubes have filled.
To adjust the dispenser, refer to the relative enclosed
manual and to the utilized type of detergent.
3.3
FILLING THE RINSING AGENT
DISPENSER (Fig. 8)
•
Insert the transparent tube (18) into the canister (19)
containing rinsing agent.
•
Start the machine as described in paragraph 2.1. The
dispenser will suck about 3 cm of liquid from the
canister.
•
Fill during the cycle by opening (slightly) and closing
the door until the tube has completely filled.
3.3.a Adjusting the dose (Fig. 8)
•
Start the machine as described in paragraph 2.1 and
hold a glass up to the light at the end of the cycle.
•
The drops of water on the glass will indicate insufficient
dosage while streaks will indicate that dosage is
excessive either in relation to density or quantity.
•
Regulate by means of the plug (20), turning clockwise
to decrease the quantity or anticlockwise to increase it.
IMPORTANT
These data are indicative and not binding since they may
vary according to the hardness of the water or the utilized
type of detergent and rinsing agent.
ATTENTION
If the utilized product (detergent or rinsing agent) is
changed, it is advisable to flush out the dosing system with
water and to then proceed by filling the dispensers.
Part 3: For the technician