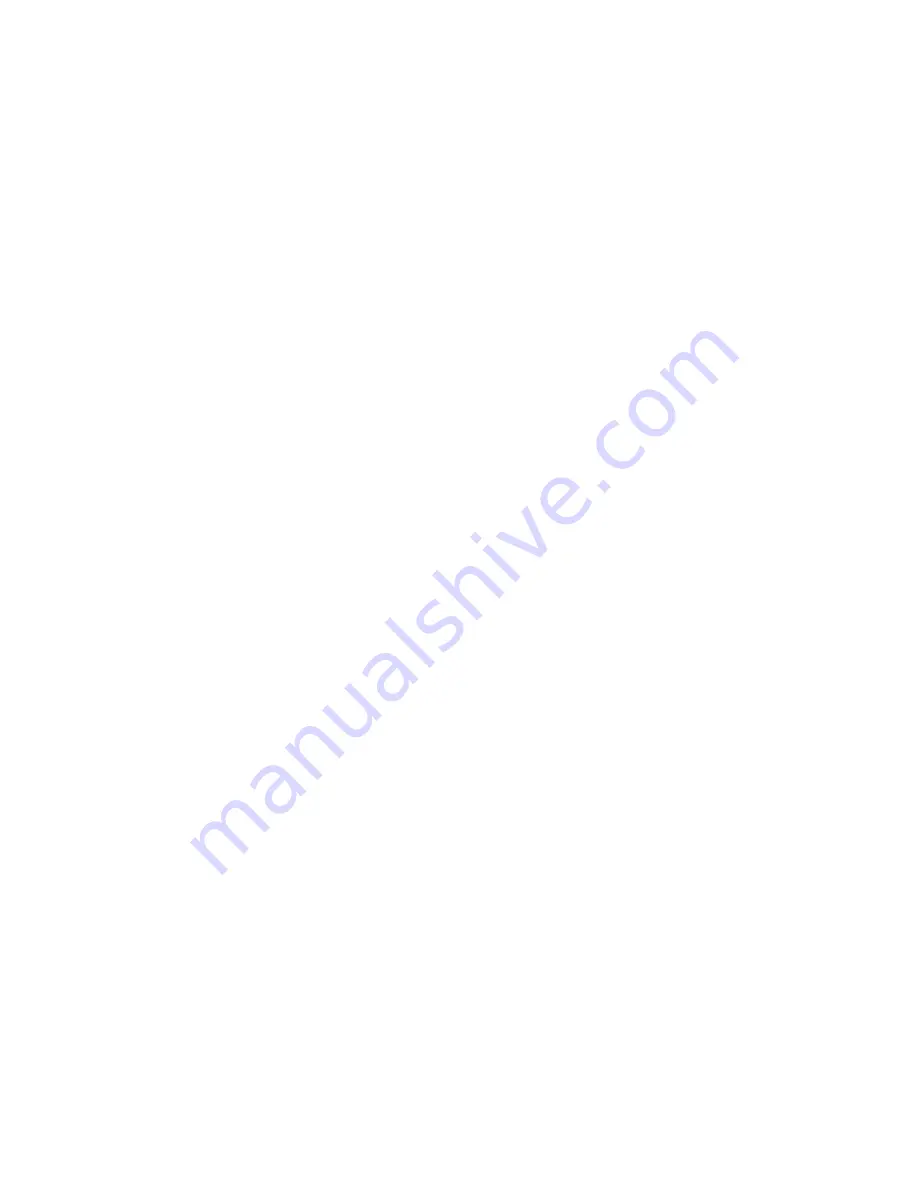
OPERATING INSTRUCTIONS
MACHINE WITH RECLAIM
*** READ BEFORE OPERATING EQUIPMENT ***
1.
Preparing parts for Blasting:
All parts to be processed must be free of
oil, grease, and moisture. Make sure parts
are dry before putting into cabinet for
cleaning.
2.
Air Pressure:
Set air pressure at 80 PSIG. Most parts
for blasting cleaning cabinet should be
blasted at 80 psi. Designate parts to be
processed, start at lower pressure and
work up the PSI scale to obtain desired
finish.
***WARNING***
DO NOT CONNECT TO HIGH
PRESSURE BOTTLE GAS, RUPTURE
AND EXPLOSION CAN OCCUR.
3.
Gun Angle and Distance:
Direct blast at part with an approximate
(45-60) degree angle with ricochet toward
the back side of cabinet. Do not hold at
90 degree to part being processed. This
will cause the media to blast to bounce
back into the blast stream and slow
blasting action. Also 90-degree angle will
cause excessive wear on gun and viewing
window. Hold gun approximately 6 inches
from part being cleaned.
***WARNING***
GUN MUST ALWAYS BE POINTED
AWAY FROM THE OPERATOR AND
TOWARD ITEM BEING PROCESSED.
NEVER BLAST WITH ANY OF THE
CABINET DOORS OPEN. WHILE
LOADING AND UNLOADING, NO ONE
SHOULD BE AT THE OPERATOR
STATION AT FRONT OF THE BLAST
CABINET.
4.
Media:
Media should be good quality and dry.
Damp media will cause the media not to
flow and will clog abrasive flow. NEVER
USE SAND. See
**CAUTION**
, below. If
you are having a problem selecting media
for a specified job, contact your distributor
for their recommendations.
**CAUTION**
**CAUTION**
DO NOT USE SAND BLASTING SAND.
THIS WILL CAUSE SILICA DUST
WHICH IS THE CAUSE OF SILICOSIS
DISEASE, A CONDITION OF MASSIVE
FIBROSIS OF THE LUNGS.
PAGE 2