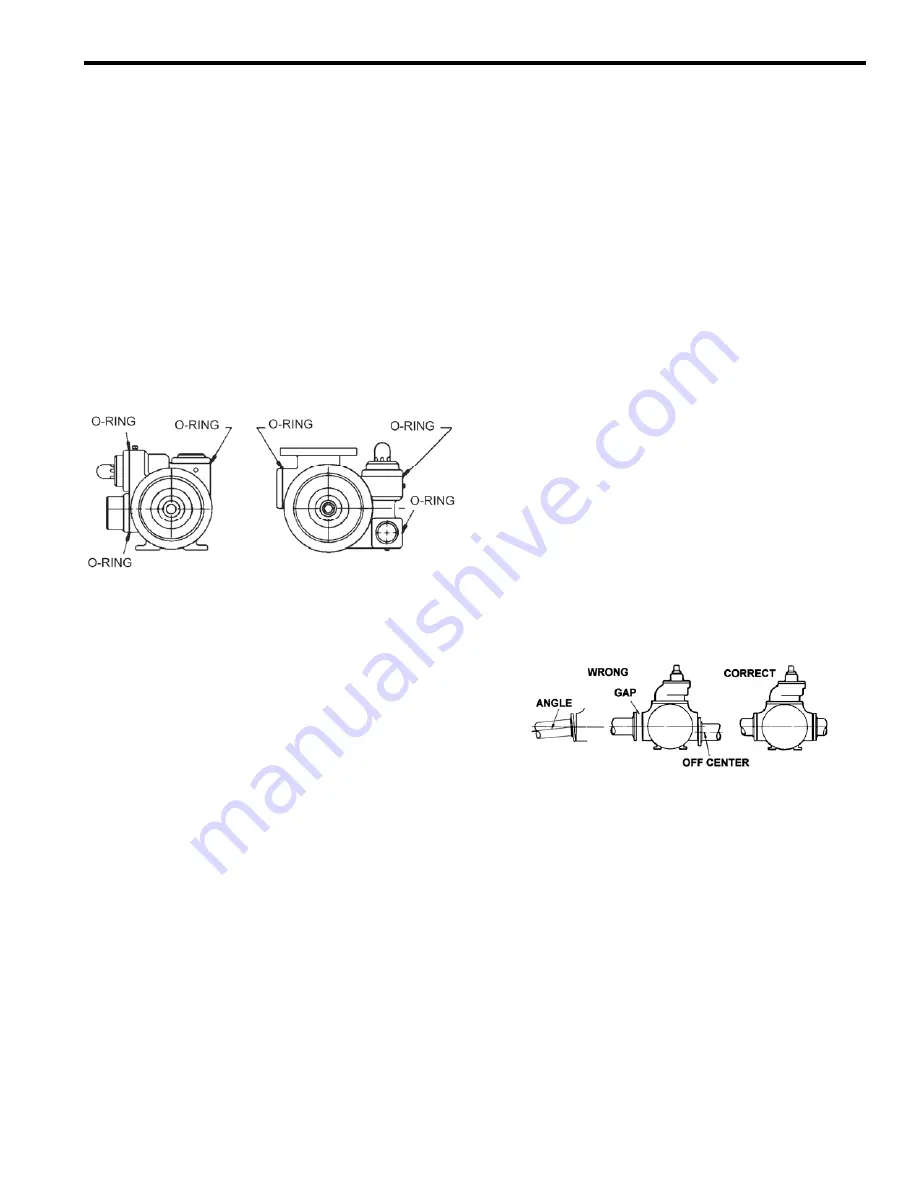
701-C00 Page 3/16
GENERAL INSTALLATION AND OPERATION
NOTICE:
Blackmer pumps must only be installed in systems
designed by qualified engineering personnel. System
design must conform with all applicable regulations and
codes and provide warning of all system hazards.
WELDED CONNECTIONS
NOTICE:
Pumps with welded connections contain three non-
metallic o-ring seals that will be damaged if welding is
done with these o-rings installed.
Prior to welding the piping, remove the O-rings from under the
inlet flange, outlet flange and relief valve cover as indicated in
Figure 1.
Reinstall the inlet and outlet flanges. Weld the piping to the
the inlet and outlet flanges. After the welding is complete,
reinstall the O-rings.
Figure 1
PRE-INSTALLATION CLEANING
NOTICE:
New pumps might contain residual test fluid and/or rust
inhibitor. If necessary, flush pump prior to use.
Foreign matter entering the pump WILL cause extensive
damage. The supply tank and intake piping MUST be
cleaned and flushed prior to pump installation and operation.
LOCATION AND PIPING
Pump life and performance will be significantly reduced when
installed in an improperly designed system. Before starting
the layout and installation of the piping system, review the
following:
1. Locate the pump as near as possible to the source of
supply to avoid excessive inlet pipe friction.
2. The inlet piping and fittings should be at least as large as
the intake port on the pump. It should slope downward to
the pump, and should not contain any upward loops.
Minimize the number of intake line fittings and eliminate
restrictions such as sharp bends; globe valves,
unnecessary elbows, and undersized strainers.
3. A strainer must be installed in the inlet line to protect the
pump from foreign matter. The strainer should be located
at least 24" (0.6m) from the pump, and have a net open
area of at least four times the area of the intake piping.
Strainers must be cleaned regularly to avoid pump
starvation.
4. The intake and discharge piping system must be free of
all leaks.
5. Expansion joints, placed at least 36" (0.9m) from the
pump, will compensate for expansion and contraction of
the pipes. Contact the flexible connector/hose
manufacturer for required maintenance/care and design
assistance in their use.
6.
ALL piping and fittings MUST be properly supported to
prevent any piping loads from being placed on the pump.
7. Check alignment of pipes to pump to avoid strains which
might later cause misalignment. See Figure 2. Unbolt
flanges or break union joints. Pipes should not spring
away or drop down. After pump has been in operation
for a week or two, completely recheck alignment.
Figure 2
8. Install pressure gauges in the NPT ports provided in the
pump casing to check pump performance at start up.
9. The use of a 1.5” or 2” vapor return line will speed up
delivery by preventing pressure build up at the receiving
tank and pressure reduction in the supply tank.
10. Keeping the liquefied gas systems full of liquid, even
when idle, will keep the O-rings from changing shape,
shrinking or super cooling. Evaporation of liquefied gas
leaves an abrasive powder on the surface which can
cause wear to the pump, meter, and seals.
Содержание CRL4B
Страница 15: ...701 C00 Page 15 16 NOTES...