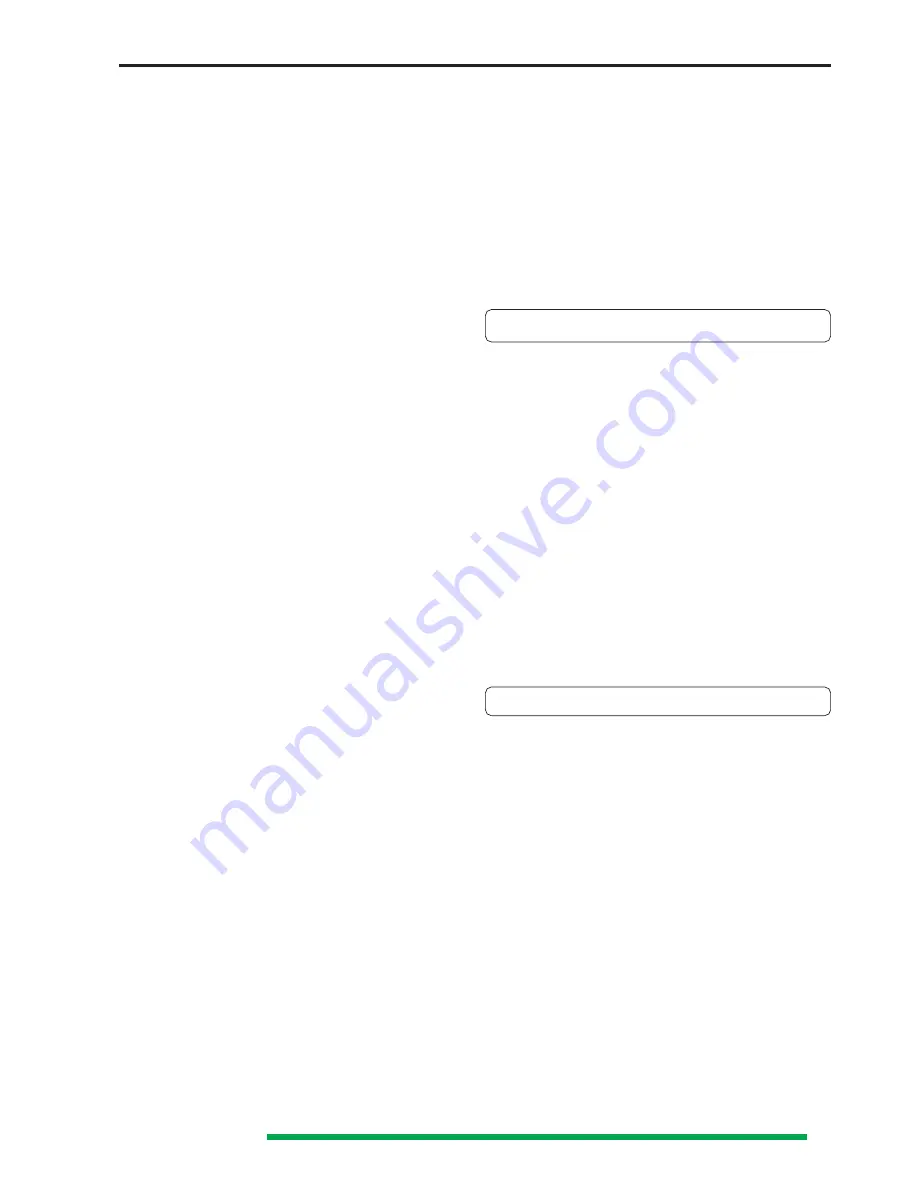
39
Subject to change without notice
(DC input coupling).
Maximum deviations of 0.12div (3%) are permissible. If a
x10 probe (1%) is connected between the 0.2V output and Y
input, the deflection coefficient should be set to 5mV/div.
Then the maximum deviation is 0.16div.
With higher tolerances it should first be determined if the
cause lies, within the amplifier or in the amplitude of the
square-wave signal. On occasions it is possible that the probe
is faulty or incorrectly compensated. If necessary the
measuring amplifier can be calibrated with an accurately
known DC voltage (DC input coupling). The trace position
should then vary in accordance with the deflection coefficient
set. With variable control in the attenuator sector fully counter-
clockwise, the input sensitivity is decreased at least by the
factor 2.5 in each position. In the 50mV/div position, the
displayed calibrator signal height should vary from 4div to at
least 1.6div.
Transmission Performance
of the Vertical Amplifier
The transient response and the delay distortion correction
can only be checked with the aid of a square-wave generator
with a fast rise time (max. 5ns). The signal coaxial cable
must be terminated at the vertical input of the
oscilloscope with a resistor equal to the characteristic
impedance of the cable (e.g. with HZ22). Checks should be
made at 100Hz, 1kHz, 10kHz, 100kHz and 1MHz, the
deflection coefficient should be set at 5mV/div with DC input
coupling. In so doing, the square pulses must have a flat top
without ramp-off, spikes and glitches; no overshoot is
permitted, especially at 1MHz and a display height of 4-5div.
At the same time, the leading top corner of the pulse must
not be rounded. In general, no great changes occur after the
instrument has left the factory, and it is left to the operators
discretion whether this test is undertaken or not.
Of course, the quality of the transmission performance is
not only dependent on the vertical amplifier. The input
attenuators, located in the front of the amplifier, are
frequency-compensated in each position. Even small
capacitive changes can reduce the transmission performance.
Faults of this kind are as a rule most easily detected with a
square-wave signal with a low repetition rate (e.g. 1kHz). If a
suitable generator with max. output of 40Vpp is available, it
is advisable to check at regular intervals the deflection
coefficients on all positions of the input attenuators and
readjust them as necessary. A compensated 2:1 series
attenuator is also necessary, and this must be matched to
the input impedance of the oscilloscope. This attenuator can
be made up locally. It is important that this attenuator is
shielded. For local manufacture, the electrical components
required are a 1M
Ω
±1% resistor, in parallel with it, a trim-
mer 3-15pF cap. in parallel with approx.10pF. One side of
this parallel circuit is connected directly to the input connector
of CH I or CH II and the other side is connected to the
generator. If possible use a low-capacitance coaxial cable. The
series attenuator must be matched to the input impedance
of the oscilloscope in the 5mV/div position. Variable control
to CAL., DC input coupling; square tops exactly horizontal;
no ramp-off is permitted. This is achieved by adjusting the
trimmer located in the 2:1 attenuator. The shape of the square-
wave should then be the same in each input attenuator
position.
Operating Modes: CH.I/II, DUAL, ADD,
CHOP., INVERT and X-Y Operation
In DUAL mode two traces must appear immediately. On
actuation of the Y-POS. controls, the trace positions should
have minimal effect on each other. Nevertheless, this cannot
be entirely avoided, even in fully serviceable instruments.
When one trace is shifted vertically across the entire screen,
the position of the other trace must not vary by more than
0.5mm.
A criterion in chopped operation is trace widening and
shadowing around and within the two traces in the upper or
lower region of the screen. Set time coefficient to 0.5ms/
div, Set input coupling of both channels to GD and advance
the INTENS. control fully clockwise. Adjust FOCUS for a sharp
display. With the Y-POS. controls shift one of the traces to a
+2div, the other to a -2div vertical position from the horizontal
center line of the graticule.
Do not try to synchronize (with the time variable con-
trol) the chop frequency (0.5MHz)!
Check for negligible trace widening and periodic shadowing
when switching between 0.5ms/div and 0.2ms/div.
It is important to note that in the I+II add mode or the I-II
difference mode the vertical position of the trace can be adjusted
by using both the Channel I and Channel II Y-POS. controls.
In X-Y Operation, the sensitivity in both deflection directions
will be the same. When the signal from the built-in square-
wave generator is applied to the X-input, then there must be
a horizontal deflection of 4div ±.16div when the deflection
coefficient is set to 50mV/div position. The check of the mono
channel display is unnecessary; it is contained indirectly in
the tests stated above.
Triggering Checks
The internal trigger threshold is important as it determines
the display height from which a signal will be stable displayed.
It should be approx. 0.3-0.5div for the instrument. An increa-
sed trigger sensitivity creates the risk of response to the
noise level in the trigger circuit. This can produce double-
triggering with two out-of-phase traces.
Alteration of the trigger threshold is not required.
Checks can be made with any sine-wave voltage between
50Hz and 1MHz. The instrument should be in automatic peak
(value) triggering (
NM
LED dark) and the LEVEL knob in
midrange position. It should be ascertained whether the same
trigger sensitivity is also present with Normal Triggering (
NM
LED lights). In this trigger mode, TRIG. LEVEL adjustment is
absolutely necessary. The checks should show the same
trigger threshold with the same frequency. On changing the
trigger slope, the start of the sweep changes from the
positive-going to the negative-going edge of the trigger signal.
As described in the Operating Instructions, the trigger
frequency range is dependent on the trigger coupling
selected. Internally the instrument should trigger perfectly
at a display height of approx. 0.5div, when the appropriate
trigger coupling mode is set.
For external triggering, the external trigger input connector
requires a signal voltage of at least 0.3Vpp, which is in
synchronism with the Y input signal. The voltage value is
dependent on the frequency and the trigger coupling mode
(AC-DC-HF-NR-LF).
Checking of the TV triggering is possible with a video signal
of any given polarity.
Use the TV-L or TV-F setting for video sync pulse separation.
Test Instructions