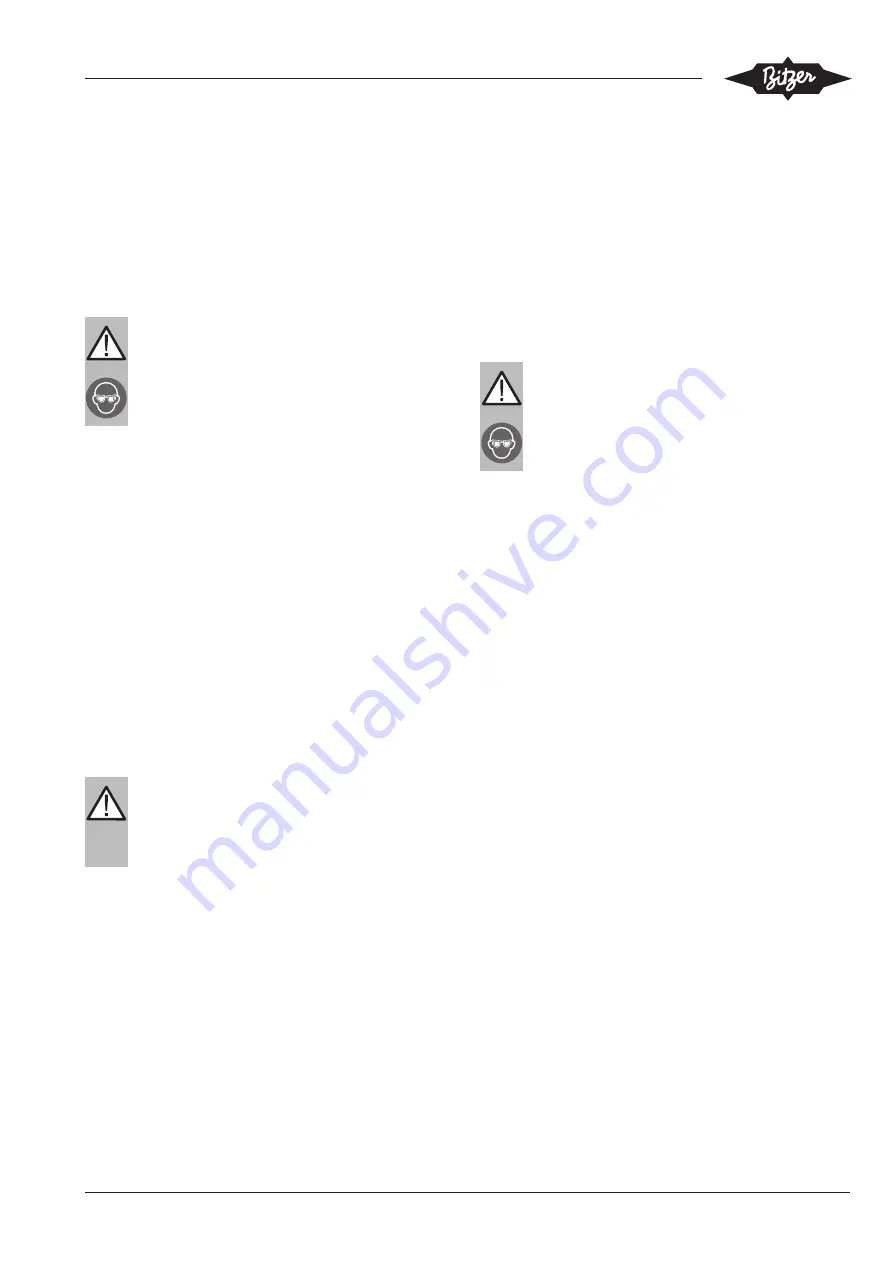
SB-520-2
33
9
Decommissioning
9.1
Standstill
Leave the oil heater switched on until disassembly.
This prevents increased refrigerant concentration in the
oil.
9.2
Dismounting the compressor
WARNING
The compressor is under pressure!
Serious injuries are possible.
Depressurize the compressor!
Wear safety goggles!
In the case of repair work requiring dismounting or in
the event of decommissioning:
Close the shut-off valves on the compressor. Extract
the refrigerant. Do not deflate the refrigerant, but dis-
pose of it properly!
Open screwed joints or flanges on the compressor
valves. Remove the compressor using hoisting equip-
ment.
9.3
Disposing of the compressor
Drain the oil from the compressor. Dispose of waste oil
properly!
Have the compressor repaired or dispose of it properly.
9.4
Dismounting the oil separator and oil cooler
WARNING
Oil separator and oil cooler are under pressure!
Serious injuries are possible.
Depressurize oil separator and oil cooler!
Wear safety goggles!
Drain oil when performing repair work or decommis-
sioning the oil separator and oil cooler.
If possible, block refrigerant and oil lines in front of and
behind the oil separator and oil cooler.
Prepare a pan: Drain oil, collect oil and dispose of it
properly.
In case of damage, the oil separator or oil cooler must
be separated from the refrigerator system and re-
placed. For this, extract the refrigerant and drain the
coolant.
Dispose of contaminated substances properly!
10 Tightening torques for screwed connections
10.1 Mind when mounting or replacing
WARNING
The system is under pressure!
Serious injuries are possible.
Wear safety goggles!
Assess the risk of intervention and take appropriate
measures, for example: wear additional personal pro-
tective equipment, shut off system or shut off the valves
before and after the respective system part and depres-
surise.
Before mounting
▶ Clean threads and threaded bores carefully.
▶ Use new gaskets only!
▶ Do not oil gaskets with metallic support.
▶ Flat gaskets may be moistened slightly with oil.
Admissible screwing methods
• Tighten with calibrated torque spanner to indicated
torque.
• Tighten with pneumatic impact wrench and retighten
with calibrated torque spanner to indicated torque.
• Tighten with electronically controlled angled wrench
to indicated torque.
Tolerance range of tightening torques: ±6% of nominal
value
Flange connections
▶ Tighten them crosswise and in at least 2 steps
(50/100%).