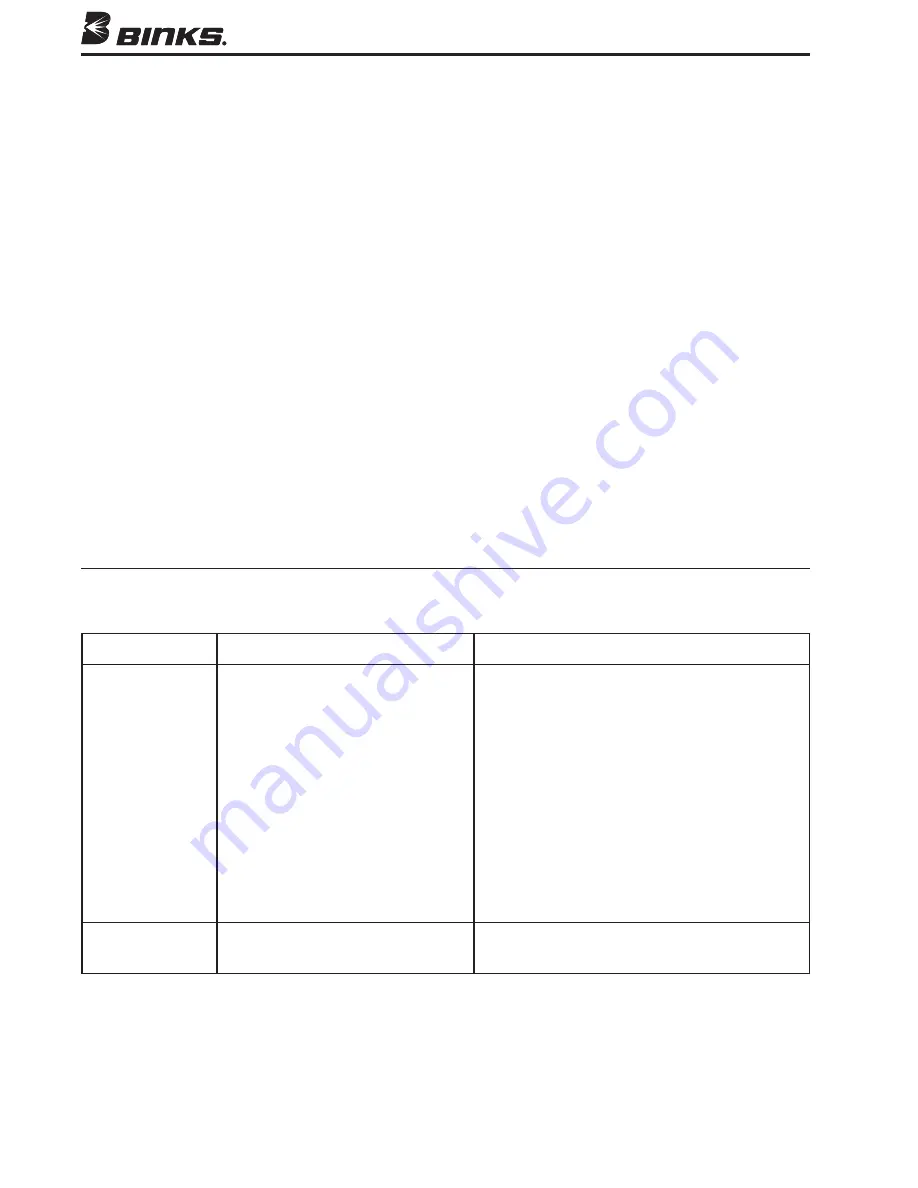
4
AIR MOTOR DRIVE SERVICE CHECKS
OPERATION AND MAINTENANCE
CONDITION
CAUSE
CORRECTION
1. Air motor needs lubrication or
cleaning.
2. Motor vanes need replacing or
contaminants present in motor
chamber, Figure 2.
3. Low oil level in gear box, Figure 3.
4. Gear and shaft assembly (58) and/
or worm gear (65) worn, Figure 3.
5. Air motor bearing (40 or 51) worn,
Figure 2.
Air motor
sluggish or
inefficient
Oil leakage
from gear box.
1. Seal (62, Figure 3) worn.
1. Lubricate (see "Air Motor Lubrication" section).
Disassemble and clean per parts replacement
instructions.
2. Disassemble, clean motor per parts replace-
ment instructions. Replace worn vanes.
3. Add oil per lubrication instructions.
4. Replace worn parts per parts replacement
instructions.
5. Replace bearings per parts replacement
instructions.
1. Replace seal per parts replacement
instructions.
Always install new gaskets (45) when reassembling air
motor.
Assemble the end plates to the body using an arbor press
with a pusher acting on both races of the bearing while
rigidly supporting the opposite (drive) end of the shaft.
Gear Box (refer fo figure 3, page 7)
1. Remove oil fill plug (60) or cover plate (56) and drain
gear box lubricant.
2. Remove set screws (63) and remove gear box from air
motor.
3. Disassembly gear box per exploded view, Figure 3.
Discard gaskets (59 and 64). Do not remove oil seal
(62) unless leakage or seal damage is indicated.
4. If oil seal (62) was removed, inspect seal seating bore
in housing (61). Remove any burrs or contaminants
from seal seating bore. Burrs or contaminants could
distort new oil seal during installation.
5. Inspect gear and shaft assembly (58) for wear grooves,
burrs, or contamination of seal seating area. If seal
seating area is damaged, shaft must be repaired or
replaced.
6. Inspect all other parts for wear spots, chipping, or other
damage. Replace damaged or worn parts.
7. If oil seal (62) is being replaced, inspect new seal for
damage before installing. Use arbor press to install
seal. Press fixture diameter must be close fit with gear
box bore diameter to avoid damage to seal. Install with
inner casing and sealing lip toward bottom of bore.
Drive seal squarely into bore to avoid warping. Oil seal
is recessed 3/32 inch from bottom of housing (61)
when properly installed.
8. Reassemble gear box per exploded view. Install new
gaskets (59 and 64). Just prior to assembling gear box
with air motor, apply a small dab of thread locking
compound (53) to threads of setscrews (63). Connect
motor and gear box and torque set screws (63) to 60
inch-pounds (6.8 N-m), minimum. Refill gear box per
gear box lubrication instructions.