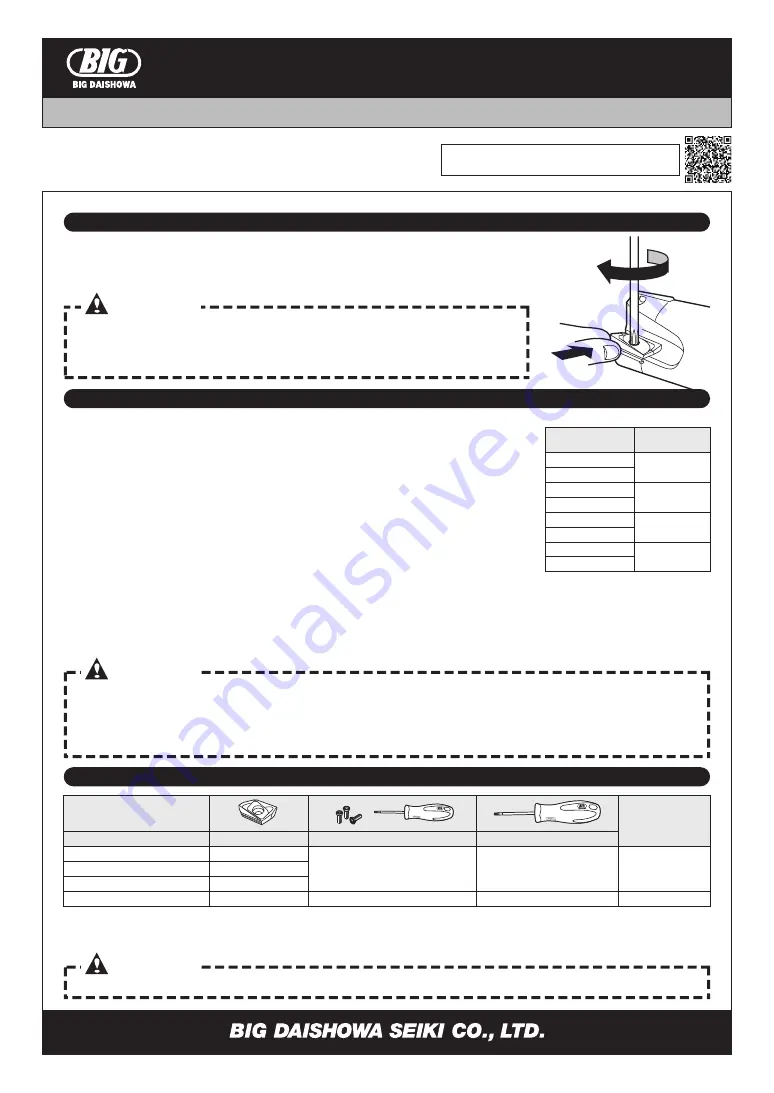
●
Before clamping inserts, remove any foreign matter on the insert seat with air blow.
●
Wipe the side and back faces of inserts with lint-free cloth throughly.
●
Tighten the screw while applying light pressure on the insert.
●
Ensure there is no gap between the insert and the insert seat.
・
Do not substitute other insert clamping screws. Use only genuine BIG screws.
・
Note: Inserts are very sharp!! Be careful to prevent injury to hands when replacing inserts.
・
Replace clamp screw periodically.
・
Do not use torx wrench with damaged tip or clamping screw with damaged torx socket.
CAUTION
CAUTION
・
Between FULLCUT MILL FCR and FCM, tools and inserts are not compatible.
・
Refer to the General Catalog to select the insert.
・
The insert clamping screw set includes 10 screws and 1 exclusive wrench.
FULLCUT MILL has exclusive shape of insert for each cutter diameter. In case an unsuitable insert is used, improper performance will occur.
S2506DS
S3508DS
DA-T 8
DA-T15
1 (0.7)
3 (2.2)
FCR16,17 (FCR .625)
FCR20,21 (FCR .750)
FCR25,26 (FCR1.000)
FCR32,33 (FCR1.250)
BRG1608
BRG2008
BRG2508
BRG3210
Tightening
torque
N
・
m (lbf
・
Ft)
Model
Insert
Insert Clamping Screw Set
Wrench
・
Do not apply under inappropriate cutting condition.
・
Do not use after the body has been in a collision and strongly shocked.
・
The tool may cause burns to skin if touched immediately after
long periods of cutting time.
・
Minimize the overhang of the tool for use.
CAUTION
●
Refer to the General Catalog for recommended cutting conditions.For the Standard Type
models with long gauge length and all the Long Type models, start operating with lower cutting
parameters and increase them gradually while observing the results.
●
NEVER exceed the maximum allowable rotational speed.
●
FULLCUT MILL FCR can be used for feeding in Z axis such as ramping,helical interpolation and drilling.
Please observe the following recommendations during operation.
・
Air blow or coolant supply must be provided when machining pockets.
(Directed through tool center is recommended.)
・
Feed angle should be less than 3° when ramping and helical interpolation.
・
Z-Axis Drilling depth(plunging) in one pass should be less than:
ø16,17(ø.625")
・・・
0.5mm(.020")
ø20,21(ø.75"), ø25,26(ø1")
・・・
1mm(.039")
ø32,33(ø1.25")
・・・
2mm(.079")
For deep hole drilling operations, the following procedure is necessary:
1.Plunge in Z-axis to maximum depth defined above
2.Radial feed cutter to required dimensions.
Note: Minimum radial feed must exceed "Cutter diameter minus 2mm(.079")"
3.Repeat this procedure until the required depth is completed.
●
Chatter may occur in long projection slot milling with 3-inserts Oversize models. In such a case,
2-inserts models taking deeper depth of cut can increase efficiency.
・
Use only with machine tool that have sufficient rigidity and
horsepower.
・
Use a cover on a machine tool and a protector such as glasses
against shattering chips and broken tools due to misuse.
・
Do not use insoluble oil due to the danger of causing fire.
34.000
34.000
28.000
23.000
Model
FCR 16,17
FCR .625
FCR 20,21
FCR .750
FCR 25,26
FCR1.000
FCR 32,33
FCR1.250
MAX
(min
-1
)
(Caution)
Influences of vibration caused by
dynamic imbalance or runout and
cutting resistance are not calculated
to determine the above max.
allowable rotational speed.
Beware of it especially in the case of
long tool extension.
The maximum allowable rotational speed
FULLCUT MILL
FCR Type
OPERATION MANUAL
HOW TO CLAMP INSERTS
ABOUT CUTTING CONDITION
INSERT AND PARTS
Please read these instructions before use and keep them where the operator
may refer to them whenever necessary.
OPERATION MANUAL DOWNLOAD SITE
https://big-daishowa.com/manual_index.php