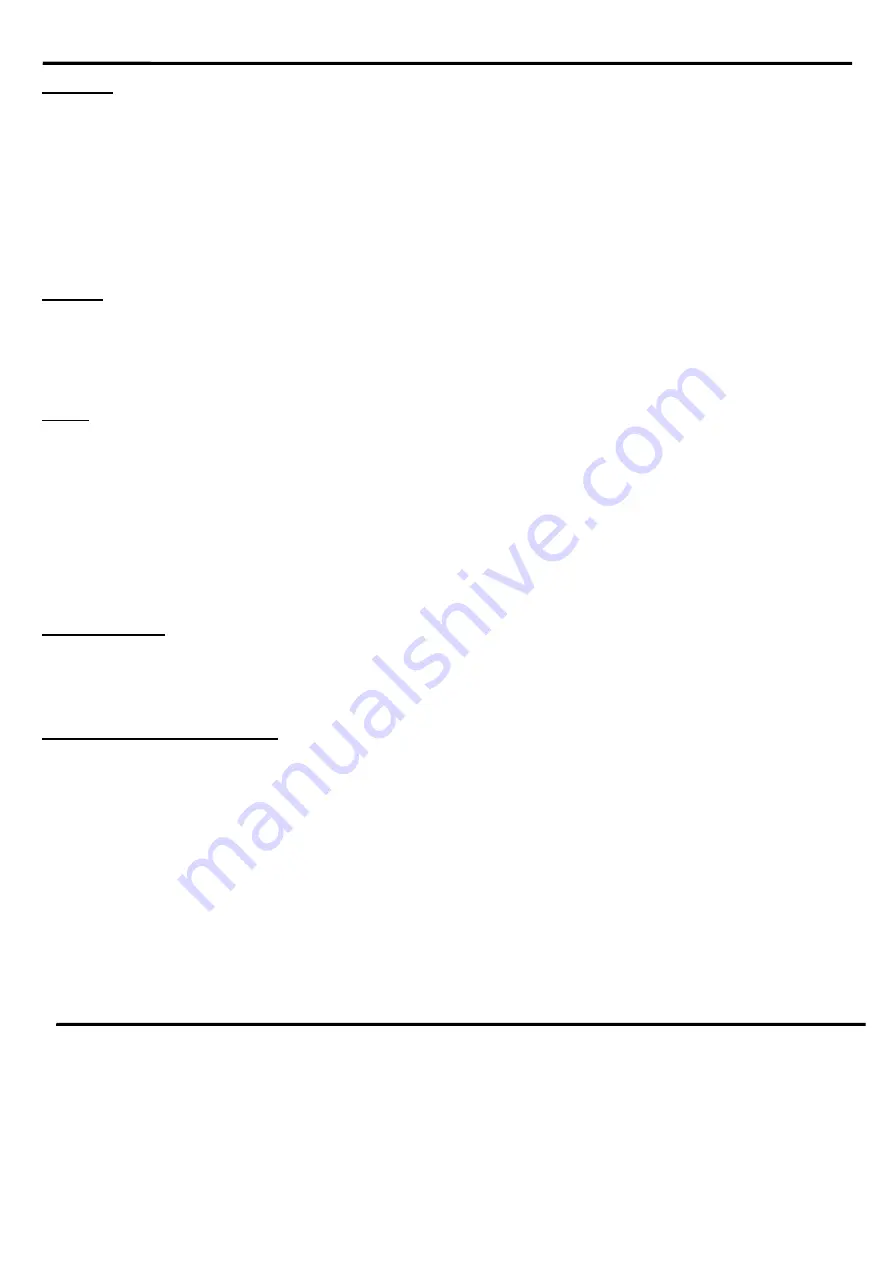
IS200 Electro-Hydraulic Actuator Positioner
Orange Instruments Limited.
Drwg. No.: 1357-007 Issue : K Date : 07/10/2013 Page :
3 of 9
Iss c - Certificate number added. Iss D - Ta changed to -20 to +60
Iss E - Details of fail modes, timers and retrans. O/P added. Retrans. Signal barrier changed to KFD0-CC-Ex1
Iss F
– Details of change in Max/min on & off times + addition of 10R in line with pos o/p –ve
Iss G
– Stepping times range change to allow finer adjustment 15/11/2007
Iss H
– CE Cert. of Conformity details added, Ta to –40degC, 60079:0,26 mods 25/06/2008
Iss J
– Harmonised standards in C of C modified to meet current status 04/08/2008
Iss K - Markings changed to meet EN 60079-0:2012 02/10/2103
ATEX Certified Equipment - Change Authority ATEX Manager ONLY
Operation
The IS200 is designed for the closed loop positioning of electro-hydraulic actuators.
The instrument compares two analogue signals, one representing the desired position (command signal) and the other
representing the actual position (feedback signal) of the actuator.
A difference between these two signals will cause one of the IS200 outputs to operate, driving the actuator to the desired
position.
A positional Dead-
zone may be adjusted to overcome “hunting” problems associated with mechanical overrun of the
actuator.
The speed of transit of the actuator can be reduced by selecting the stepping mode that provides independently adjustable
on and off times for the open and close solenoid operation.
Physical
The IS200 is housed in a small DIN rail mounted polyester enclosure measuring 85 x 70 x 58h. The circuit boards are
coated with a resist layer that protects the track from moderate condensation and mould growth problems. Connections are
via screw terminals with a capacity of 2.5mm
2
but the use of ferrules or crimps is recommended. All adjustments are
accessible on the front panel of the enclosure.
Wiring
To comply with the IS Certification the IS200 must be wired as shown in the circuit on Page 7. Wiring should be completed
by suitably trained personnel taking into account the following notes:
To ensure RFI compliance the analogue signals MUST be routed in copper braided screened cables with a fill factor
density of at least 0.7.
The screens should be terminated to the metal of the actuator housing, ideally at a suitable metal cable gland.
Signal cables should be routed separately from power and switching conductors.
Ensure that all supply and signal barriers are present and correctly connected and supplied with power from the safe
area.
Positioner set-up
The solenoid sense and command signal default mode are set up by a sequence of push button operations at power up.
These operations will affect the outputs to the solenoids so it is important that the actuator is isolated hydraulically during
these operations to avoid unwanted movement of the actuator. Note that a low value resistor, 10R, might be required in the
negative lead, Terminal 19, of the retransmitted signal output to reduce instability in the IS200 / barrier loop.
Setting solenoid operating sense
If the actuator has a spring assisted return to a default position it may be necessary to change the sense of the output
solenoid such that at the desired balance point one of the solenoids is energised thus holding the actuator position against
the spring. A one-off operation of the positioner will store the choice in non-volatile EEPROM memory.
1. Hold in the CALIBRATE pushbutton and apply power to the positioner.
2. The CALIBRATE LED will light continuously and pressing the manual DECREASE and INCREASE pushbuttons will
cause the appropriate DECREASE and INCREASE LEDS to “toggle” on and off.
3. Select the pattern of LEDs to reflect what is required at balance e.g. for an actuator that fails downscale the
DECREASE LED should be lit.
4. When satisfied press the CALIBRATE button again.
5. Remove power from the positioner.