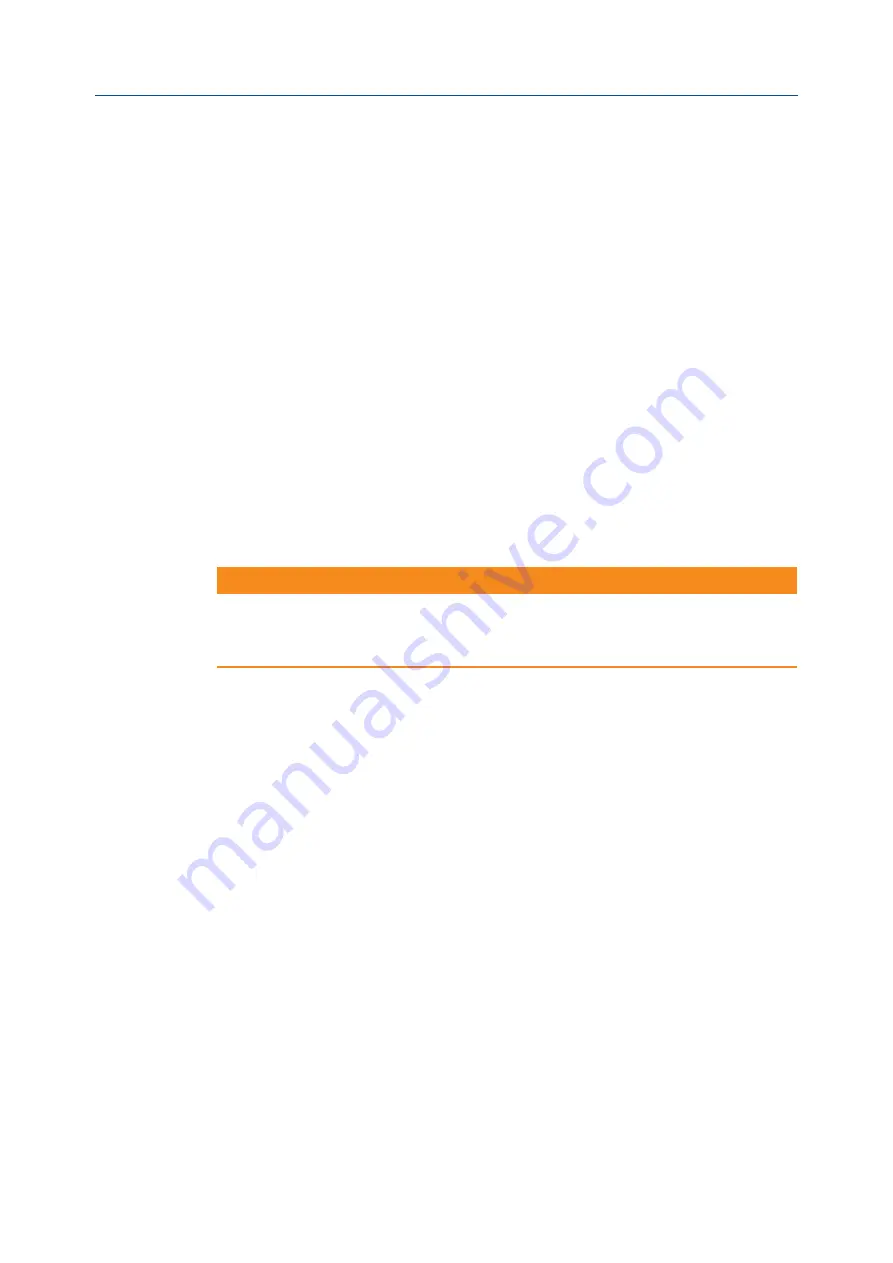
July 2020
Installation, Operation and Maintenance Manual
MAN 575 Rev. 4
10
Installation
Section 2: Installation
2.5
Pneumatic Connections
Connect the actuator to the pneumatic feed line with fittings and pipes in accordance to
the plant specifications. They must be sized correctly in order to guarantee the necessary
air flow for the operation of the actuator, with pressure drops not exceeding the maximum
allowable value.
The shape of the connecting piping must not cause excessive stress to the inlets of the
actuator. The piping must be suitably fastened so as not to cause excessive stress or
loosening of threaded connections, if the system undergoes strong vibrations.
Every precaution must be taken to ensure that any solid or liquid contaminants which
may be present in the pneumatic pipe-work to the actuator are removed to avoid
possible damages to the unit or loss of performance. The inside of the pipes used for the
connections must be well cleaned before use: wash them with suitable substances and
blow through them with air or nitrogen.
The ends of the tubes must be well debarred and cleaned. Once the connections are completed,
operate the actuator and check that it functions correctly, that the operation times meet the
plant requirements and that there are no leakages in the pneumatic connections.
2.6
Electrical Connections (If Any)
!
WARNING
The connections should be made by qualified staff. Before carrying out any operation,
cut line power off. Safety provisions as per CEI 64-8 regulation should be complied with
(same as IEC 60364).
Connect the electrical feed, control and signal lines to the actuator, by linking them up with
the terminal blocks of the electrical components. In order to do this, the housing covers
must be removed without damaging the coupling surfaces, the O-rings or the gaskets.
Remove the plugs from the cable entries. For electrical connections use components (cable
glands, cables, hoses, conduits) which meet the requirements and codes applicable to the
plant specifications (mechanical protection and/or explosion-proof protection). Screw
the cable glands tightly into the threaded inlets, so as to guarantee the weatherproof
and explosion-proof protection (when applicable). Insert the connection cables into
the electrical enclosures through the cable glands, and connect the cable wires to the
terminals according to the applicable wiring diagram. If conduits are used, it is advisable
to carry out the connection to the electrical enclosures by inserting hoses so as not to
cause anomalous stress on the housing cable entries. Replace the plastic plugs of the
unused enclosure entries by metal ones, to guarantee perfect weatherproof tightness
and to comply with the explosion-proof protection codes (where applicable). Once the
connections are completed, check that the controls and signals work properly.