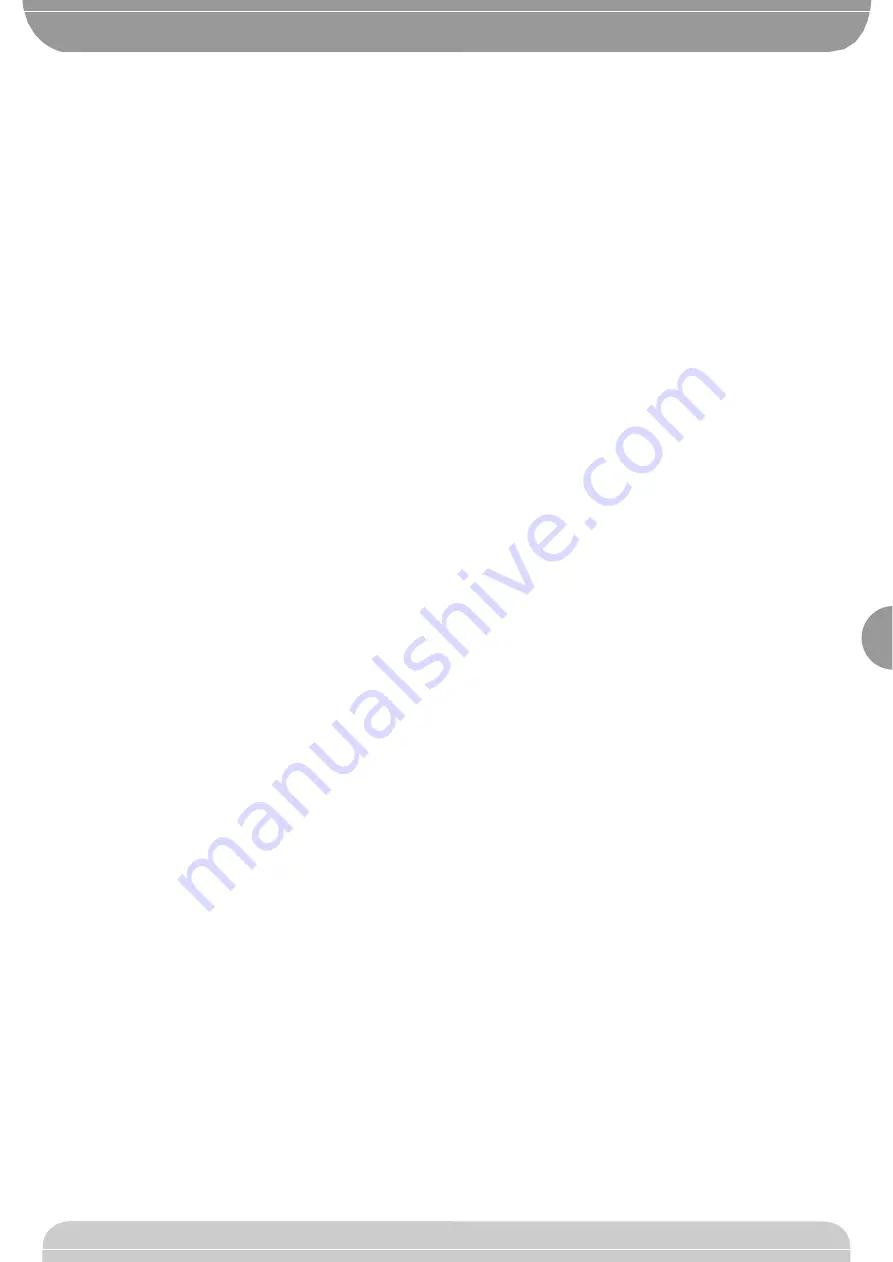
287
1) GENERAL SAFETY
WARNING! An incorrect installation or improper use of the product
can cause damage to persons, animals or things.
•
The “
Warnings
” leaflet and “
Instruction booklet
” supplied with this
product should be read carefully as they provide important information
about safety, installation, use and maintenance.
•
Scrap packing materials (plastic, cardboard, polystyrene etc) according
to the provisions set out by current standards. Keep nylon or polystyrene
bags out of children’s reach.
•
Keep the instructions together with the technical brochure for future
reference.
•
This product was exclusively designed and manufactured for the use
specified in the present documentation. Any other use not specified in
this documentation could damage the product and be dangerous.
•
The Company declines all responsibility for any consequences resulting
from improper use of the product, or use which is different from that
expected and specified in the present documentation.
•
Do not install the product in explosive atmosphere.
•
The construction components of this product must comply with the
following European Directives: 89/336/CEE, 73/23/EEC, 98/37/EEC
and subsequent amendments. As for all non-EEC countries, the above-
mentioned standards as well as the current national standards should
be respected in order to achieve a good safety level.
•
The Company declines all responsibility for any consequences resulting
from failure to observe Good Technical Practice when constructing
closing structures (door, gates etc.), as well as from any deformation
which might occur during use.
•
The installation must comply with the provisions set out by the following
European Directives: 89/336/CEE, 73/23/EEC, 98/37/EEC and
subsequent amendments.
•
Disconnect the electrical power supply before carrying out any work on
the installation. Also disconnect any buffer batteries, if fitted.
•
Fit an omnipolar or magnetothermal switch on the mains power supply,
having a contact opening distance equal to or greater than 3mm.
•
Check that a differential switch with a 0.03A threshold is fitted just before
the power supply mains.
•
Check that earthing is carried out correctly: connect all metal parts for
closure (doors, gates etc.) and all system components provided with an
earth terminal.
•
Fit all the safety devices (photocells, electric edges etc.) which are
needed to protect the area from any danger caused by squashing,
conveying and shearing.
•
Position at least one luminous signal indication device (blinker) where
it can be easily seen, and fix a Warning sign to the structure.
•
The Company declines all responsibility with respect to the automation
safety and correct operation when other manufacturers’ components
are used.
•
Only use original parts for any maintenance or repair operation.
•
Do not modify the automation components, unless explicitly authorised
by the company.
•
Instruct the product user about the control systems provided and the
manual opening operation in case of emergency.
•
Do not allow persons or children to remain in the automation operation
area.
•
Keep radio control or other control devices out of children’s reach, in
order to avoid unintentional automation activation.
•
The user must avoid any attempt to carry out work or repair on the
automation system, and always request the assistance of qualified
personnel.
•
Anything which is not expressly provided for in the present instructions,
is not allowed.
2) GENERAL OUTLINE
The
TELEC MA
system is compatible with the
EElink
protocol for fast
installation and maintenance.
It is suitable for motorising sectional doors (fig.14), protruding fully retracting
spring-operated overhead doors (fig.2) and counterweight overhead doors
provided with an appropriate towing arm (fig.3). The overhead door must
not be higher than 2.5 metres (3.5m with extension). It is easy to install and
fast to fit and does not need the door to be modified. The irreversible
gearmotor keeps the door locked in the closing position. The control unit is
built-in. It controls the operation relays and the safety devices (photocell,
rubber skirt) before performing every manoeuvre.
3) TECHNICAL SPECIFICATIONS
3.1) Actuator
Power supply: ................................ 230V
±
10%, 50-60Hz Single-phase(*)
Motor voltage: ................................................................................... 24Vdc
Max power absorbed from mains: ................................................... 140W
Lubrication: ................................................................... Permanent grease
Towing and pushing force: ................................................................ 600N
Working stroke: ............................ 2.55m (extended to 3.5m in Mod.PT1)
Average speed: .............................................................................. 7m/min
Impact reaction in closing: ...................... Ampere-stop (Stop and reverse)
Manoeuvres in 24 hours: ...................................................................... 100
Limit switches: .................................................... Electrical and adjustable
Courtesy light: ........................................................... 230V 25W max, E14
Working temperature: .......................................................... -15
°
C / +60
°
C
Degree of protection: ......................................................................... IP30
Total weight: ..................................................................................... 12 kg
Noise: .......................................................................................... <70dB(A)
Dimensions: .................................................................................. See fig.1
(*) Available in all mains voltages.
3.2) QTELEC MA control unit
(fig.16)
Supply to accessories: ..................................................... 24Vac (1A max)
Ampere-stop setting: ........................................... On closing and opening
Automatic closing time: ..................................................... From 2 to 120s
Working time: ....................................................................... From 1 to 60s
Reverse pause: ........................................................................ Approx. 1s
Blinker connection: ........................................................ 230Vac max 40W
Service light switching time: ................................................................. 90s
Pre-alarm time: ....................................................................................... 3s
Parameter and option setting: ........... By means of LEDs and small keys
Incorporated Rolling-Code radio receiver: ............ Frequency 433.92MHz
Coded by means of: .............................................. Rolling-Code algorithm
No. combinations: ........................................................................ 4 milliard
Impedance antenna: .......................................................... 50Ohm (RG58)
Max no. of radio controls to be memorised: .......................................... 64
3.3) Transmitter
Key colour : .......................................................................................... Red
Power supply : ........................................................... 12V Alkaline battery
Range : ............................................................................... 50-100 metres
Transmitter versions: ..................................................................................
TRC1
- Single-channel,
TRC2
- Double-channel,
TRC4
- Four-channel.
4) ACTUATOR INSTALLATION
4.1) Preliminary checks
•
Check that the door is balanced.
•
Check that the door slides smoothly along its entire travel.
•
If the door has not been newly installed, check the wear condition of all
its components.
•
Repair or replace faulty or worn parts.
•
The automation reliability and safety are directly influenced by the state
of the door structure.
4.2) Fitting
After being unpacked, the door opener looks as illustrated in fig.4.
Remember to dispose of all the packing elements by separating the
different types of material (cardboard, polystyrene, PVC etc.) according to
the provisions set out by the current standards.
•
Remove the existing locking bolt from the cremone bolt of the door.
•
Position joint “
G
” as shown in fig.5.
•
Position the half track as in fig.6, and lower it to the supporting surface
while tensioning the chain and therefore obtaining a whole track.
•
Fit the joint to overlap each of the two half tracks by half its length, as in fig.7.
•
Secure the joint by tightening the appropriate screws supplied, as in
fig.8. The door opener is thus ready to be installed.
•
Mark the mid-point of the door and fix the track articulated joint to the
door frame, as in fig.9. If the ceiling is high enough, the articulated joint
can be fitted higher up and fixed to the masonry lintel by means of
dowels.
•
With the help of an adequate support, lift the motorised head until the
track is levelled, as in fig.10.
•
Fix the two supporting brackets to the ceiling, as in fig.11. Recheck
everything and fix the two supporting brackets to the gearmotor
base plate.
•
Release the towing carriage (fig.12) by pulling the wire, and bring the
towing arm as far as the door panel. Fix the towing arm to the door panel,
as in fig.13, using the screws supplied.
5) ELECTRICAL INSTALLATION SET-UP
(fig.14)
I)
Type-approved omnipolar circuit breaker with at least 3-mm contact
opening, provided with protection against overloads and short circuits,
suitable for cutting out automation from the mains. Place, if not al ready
installed, a type-approved differential switch with a 0.03A threshold just
TELEC MA
TELEC MA
AUTOMATION FOR SPRING OVERHEAD DOORS
AUTOMATION FOR SPRING OVERHEAD DOORS
D811266_02