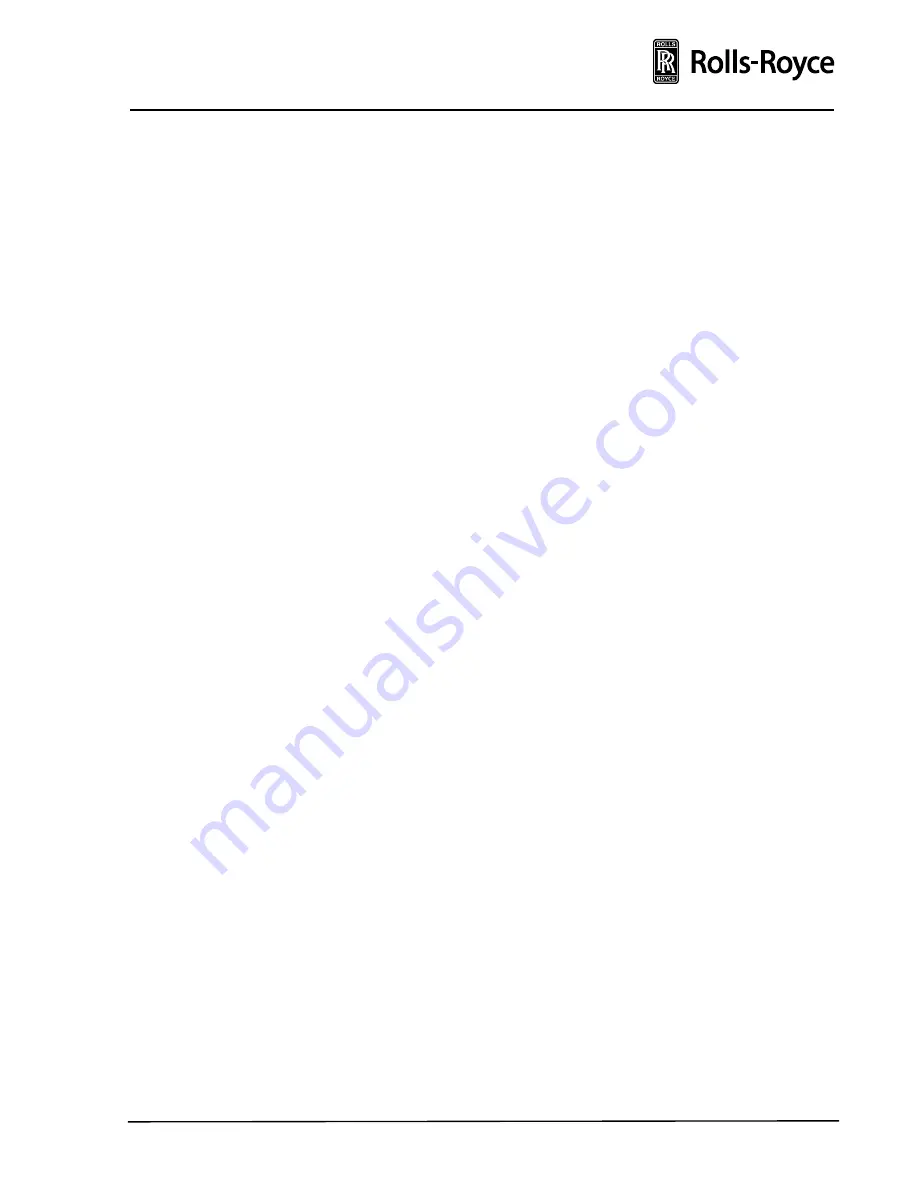
3.02
, Gas
Safety, Control and Monitoring System
Page 5 : 9
0211 BC
•
External start interlock - Signal from external
systems indicating that engine start should be
blocked.
Slow down
Slow down is a digital output to the propulsion con-
trol system or PMS for automatically reduction of
power on engine. A situation has occurred which re-
quires the power to be reduced immediately. The
power is to be reduced to the minimum required to
retain ships manoeuvrability. Repeated slow down
alarms should result in back-up propulsion.
The following conditions results in a "slow down"
alarm:
•
Low control air pressure - control air pressure
below set point
•
Knock alarm level #3 - heavy knocking on one
or several cylinders
•
Governor alarm - alarm generated by the speed
governor (see alarm list for details)
Power rate reduce
Power rate reduce is a digital output to the propul-
sion control system or PMS requesting on/off load
rate to be reduced. A situation occurred which re-
sults in the engine control system being unable to
safely respond to rapid on/off loading rates. The rate
of change of power must be reduced to safely run
the engine.
The following conditions results in a "power rate
reduce" alarm:
•
Governor alarm - alarm generated by the speed
governor (see alarm list for details)
Distributed I/O
Background
This I/O range is an IP20 modular based system,
designed for rough environment.
It has various marine approvals and is certified
according to shock and vibrating level B in DNV's
regulation (up to 4g). The I/O range consists of
several specially designed input and output
modules which together can form a complete set of
I/O. Each node has a bus coupler interfacing the I/O
modules with the appropriate field bus system.
Design
The I/O system is used for both the SSC System and
the Monitoring System. The two systems will be
arranged into separate physical stations to avoid
mixing of the two systems, both supplied by sepa-
rate supply lines. The I/O stations will be located on
the engine as well as in the ECC for interfacing the
signals to and from external sources as propeller
control/PMS. This will reduce the amount of cabling
and the length of the signal cable as the I/O stations
is located close to the sensor. When the signal collec-
tion is separated into several stations another bene-
fit is that a fault in one station can not influence the
signals in another station and hence the risk of
system failures is minimized.
Most signals common to both the SSC and the
Monitoring system will be arranged with either
separate sensors to both I/O stations or sensors with
separate sensing elements. This design method has
the benefit that the operator has a backup if one of
the sensors should fail. A failure on a sensor will be
indicated on the alarm management system.
The distributed I/O modules include diagnostic
signals used to indicate faulty behaviour of a sensor.
All diagnostic data is presented on the alarm system.
I/O Communication
Background
The I/O communication is of type Profinet. Profinet is
based on Industrial Ethernet and is a development
of the Profibus standard into today's technology.
Profinet is a flexible solution giving the engineer a
wide variety of configuration possibility. Several
topology designs can be used and the low level field
bus can be accessed from practically anywhere.
Profinet also incorporates PROFISafe for dealing with
safety functions up to SIL 3 level.
Topology
The Profinet is arranged with a ring topology. This
topology is chosen to increase the safety of the field
bus. Each I/O station is a node on the ring with its
own built in 2-port switch capable of dealing with a
ring structure. This makes the need for "drop-off"
cables from a switch unnecessary.
In the ECC there is a ring master. The ring master is a
switch, with built-in ring master function. The ring
master make sure that if there is to be a wire break
on the field bus somewhere in the ring; the ring
master will make sure that the signal packet are rout-
ed around the wire break, as well as signalling to the
alarm management system that a wire break on the
field bus system has occurred.
Содержание B35:40
Страница 1: ...Ma r i n e P r o j e c t G u i d e B e r g e ne n g i n et y p eB 3 5 4 0G a s...
Страница 2: ...BLANK...
Страница 4: ...BLANK...
Страница 6: ...BLANK...
Страница 9: ...Gas Technical data Page 1 8 1 02 0611 B TECHNICAL DATA...
Страница 17: ...Gas Main dimensions Page 1 8 1 03 0611 B MAIN DIMENSIONS...
Страница 18: ...Main dimensions Page 2 8 1 03 Gas 0611 B...
Страница 19: ...1 03 Gas Main dimensions Page 3 8 0611 B...
Страница 20: ...Main dimensions Page 4 8 1 03 Gas 0611 B...
Страница 21: ...1 03 Gas Main dimensions Page 5 8 0611 B...
Страница 22: ...Main dimensions Page 6 8 1 03 Gas 0611 B...
Страница 23: ...1 03 Gas Main dimensions Page 7 8 0611 B...
Страница 24: ...Main dimensions Page 8 8 1 03 Gas 0611 B...
Страница 26: ...Gas Load limit Page 1 1 1 07 0314 B G LOAD LIMIT Load limit curve B35 40 PG...
Страница 31: ...Starting and control air system Page 4 5 2 01 Gas 0615 BC...
Страница 32: ...2 01 Gas Starting and control air system Page 5 5 0615 BC...
Страница 37: ...Exhaust gas system Page 4 5 2 03 Gas 0317 BC...
Страница 38: ...2 03 Gas Exhaust gas system Page 5 5 0317 BC...
Страница 44: ...Fuel gas supply system Page 4 4 2 05 Gas 0717 BC...
Страница 48: ...Page 4 6 2 06 Gas 1011 BC...
Страница 49: ...2 06 Gas Page 5 6 1011 BC...
Страница 50: ...Page 6 6 2 06 Gas 1011 BC...
Страница 56: ...Lubricating oil system Page 4 9 2 08 Gas 0915 BC...
Страница 57: ...2 08 Gas Lubricating oil system Page 5 9 0915 BC...
Страница 58: ...Lubricating oil system Page 6 9 2 08 Gas 0915 BC...
Страница 59: ...2 08 Gas Lubricating oil system Page 7 9 0915 BC...
Страница 60: ...Lubricating oil system Page 8 9 2 08 Gas 0915 BC...
Страница 61: ...2 08 Gas Lubricating oil system Page 9 9 0915 BC...
Страница 70: ...3 02 Gas Safety Control and Monitoring System Page 7 9 0211 BC...