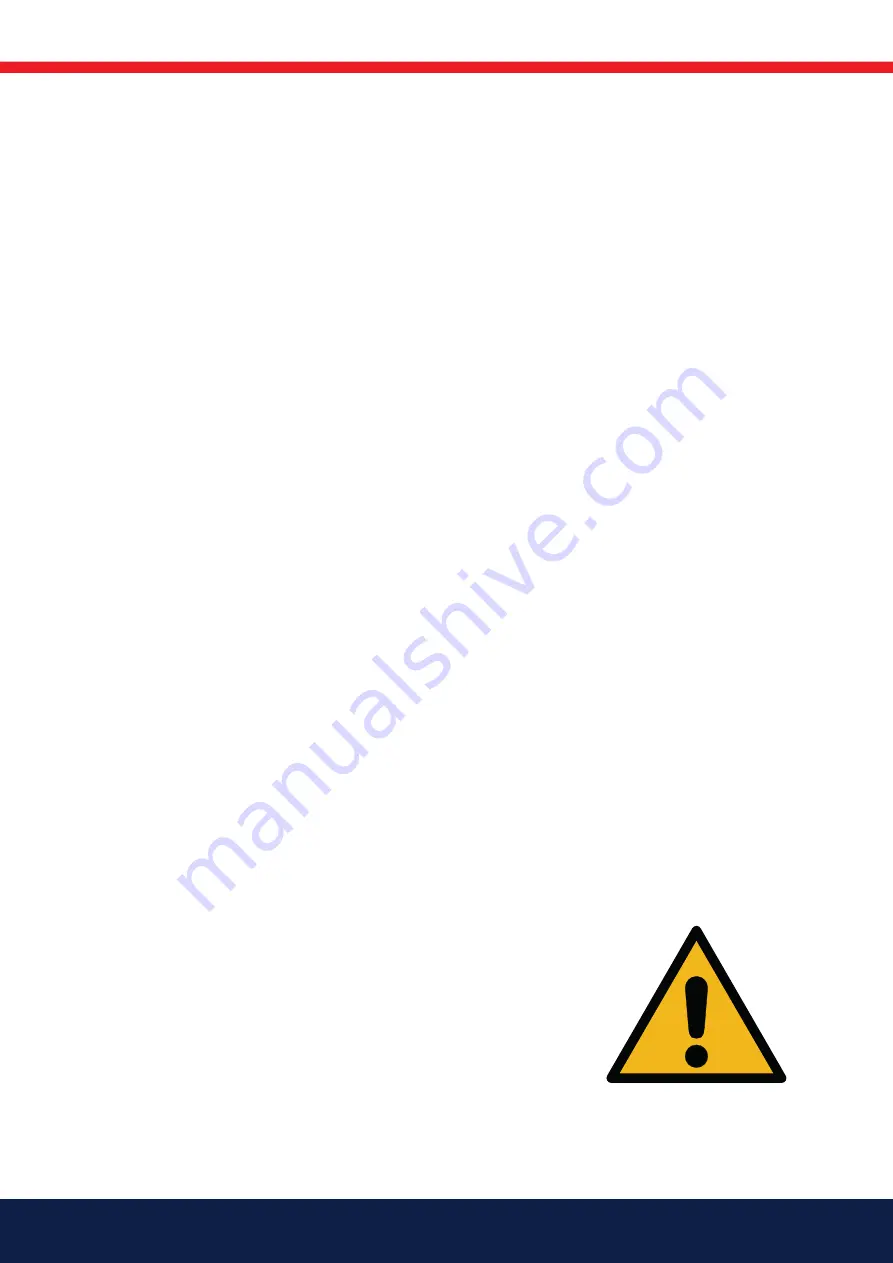
5
Bentone
•
All components must be installed without being bent, twisted
or subjected to mechanical or thermal forces that affect
components.
•
Care must be taken by the installer to ensure that no electrical
cables or fuel lines are crushed or otherwise damaged during
installation or service.
•
Sharp edges can occur on, for example: fl ame tube, fan wheel
and air damper.
•
The gas outlet from the pressure regulator must be
confi gured in accordance with applicable regulations and lead
to a safe area.
- before fi rst start:
•
The burner must not be put into operation without proper
safety and protection devices.
•
Permitted ambient temperature during operation -10 to +60
°C. Max. 80% relative humidity, no condensation.
•
The surface temperature of the burner’s components may
exceed 60 °C.
•
Handle with caution – the burner has moving parts, and there
is risk of crushing injuries.
•
Seal inspections must be performed during installation and
servicing to prevent leakage.
•
Fitting and installation work has been completed and
approved.
•
Electrical installation has been correctly performed.
•
Flue gas ducts and combustion air ducts are not blocked.
•
All actuators and control and safety devices are in working
order and correctly set.
•
If the boiler is equipped with an access hatch, this must be
equipped with a hatch opening switch connected to the
burner’s safety system.
•
When in operation, the burner’s noise level can exceed 85 dBA
– use hearing protection!
- Operation:
•
Carry out all stipulated settings, service and inspection work
within the set time.
1.3 What to do if you smell gas
•
Turn off the fuel supply.
•
Turn off the equipment and remove the boiler from operation.
•
Open windows and doors.
•
Prevent open fl ames or sparking, e.g. do not turn lights on or
off, do not use any electrical appliances or mobile phones.
•
Evacuate the building.
•
Notify the installer or gas supplier of the problem so that it
can be rectifi ed.
Содержание BG 400LN
Страница 42: ......
Страница 43: ......
Страница 44: ...Enertech AB P O Box 309 SE 341 26 Ljungby www bentone com...