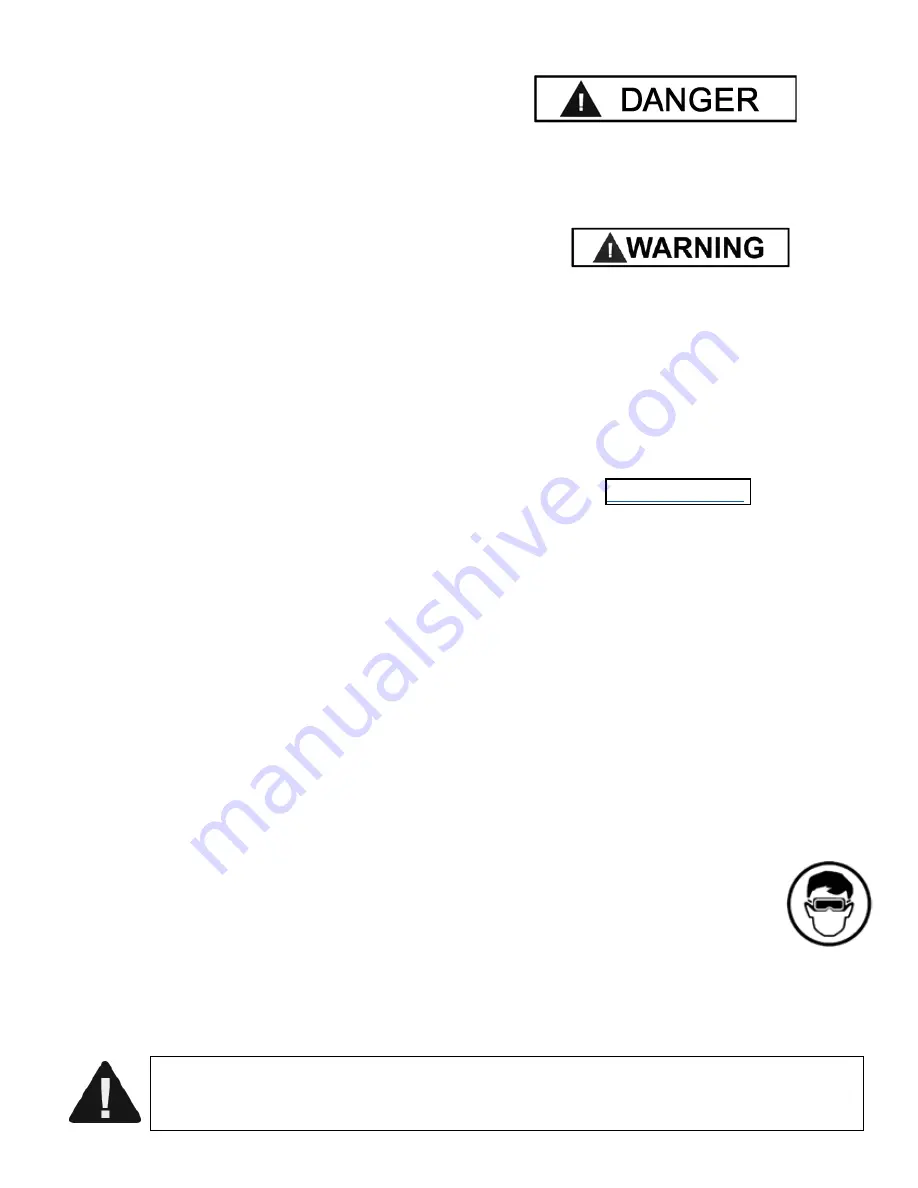
5
INSTALLER / OPERATOR
PLEASE READ AND FULLY
UNDERSTAND.
BY PROCEEDING YOU AGREE TO
THE FOLLOWING.
t
I have visually inspected the site where the lift is to be
installed and verified the concrete to be in good condi-
tion and free of cracks or other defects. I understand that
installing a lift on cracked or defective concrete could
cause lift failure resulting in personal injury or death.
t
I understand that a level floor is required for proper
installation and level lifting.
t
I understand that I am responsible if my floor is of
questionable slope and that I will be responsible for all
charges related to pouring a new level concrete slab if
required and any charges.
t
I understand that BendPak lifts are supplied with
concrete fasteners meeting the criteria of the
American National Standard “Automotive Lifts -
Safety Requirements for Construction, Testing, and
Validation” ANSI/ALI ALCTV-2011, and that I will
be responsible for all charges related to any special
regional structural and/or seismic anch oring require-
ments specified by any other agencies and/or codes
such as the Uniform Building Code (UBC) and/or
International Building Code (IBC).
t
I assume full responsibility for the concrete floor and
condition thereof, now or later, where the above
equipment model(s) are to be installed. Failure to fol-
low danger, warning, and caution instructions may
lead to serious personal injury or death to operator or
bystander or damage to property.
t
I understand that Bendpak lifts are designed to be
installed in indoor locations only. Failure to follow
installation instructions may lead to serious personal
injury or death to operator or bystander or damage
to
property or lift.
Failure to follow danger, warning, and caution instructions
may lead to serious personal injury or death to operator or
bystander or damage to property.
Please read entire manual prior to installation.
Do not operate this machine until you read and understand
all the dangers, warnings and cautions in this manual.
For additional copies or further information, contact:
BendPak Inc. / Ranger Products
1645 Lemonwood Dr.
Santa Paula, CA. 93060
1-805-933-9970
INSTALLER / OPERATOR
PROTECTIVE EQUIPMENT
Personal protective equipment helps makes installation
and operation safer, however, it does not take the place
of safe operating practices. Always wear durable work
clothing during any installation and/or service activity. Shop
aprons or shop coats may also be worn, however loose
fitting clothing should be avoided. Tight fitting leather
gloves are recommended to protect technician hands
when handling parts. Sturdy leather work shoes with steel
toes and oil resistant soles should be used by all service
personnel to help prevent injury during typical
installation and operation activities.
Eye protection is essential during installation
and operation activities. Safety glasses with
side shields, goggles, or face shields are
acceptable. Back belts provide support dur-
ing lifting activities and are also helpful in
providing worker protection. Consideration
should also be given to the use of hearing protection if
service activity is performed in an enclosed area, or if noise
levels are high.
THIS SYMBOL POINTS OUT IMPORTANT SAFETY INSTRUCTIONS WHICH IF NOT FOLLOWED
COULD ENDANGER THE PERSONAL SAFETY AND/OR PROPERTY OR YOURSELF AND OTHERS
AND CAN CAUSE PERSONAL INJURY OR DEATH. READ AND FOLLOW ALL INSTRUCTIONS IN
THIS MANUAL BEFORE ATTEMPTING TO OPERATE THIS MACHINE.