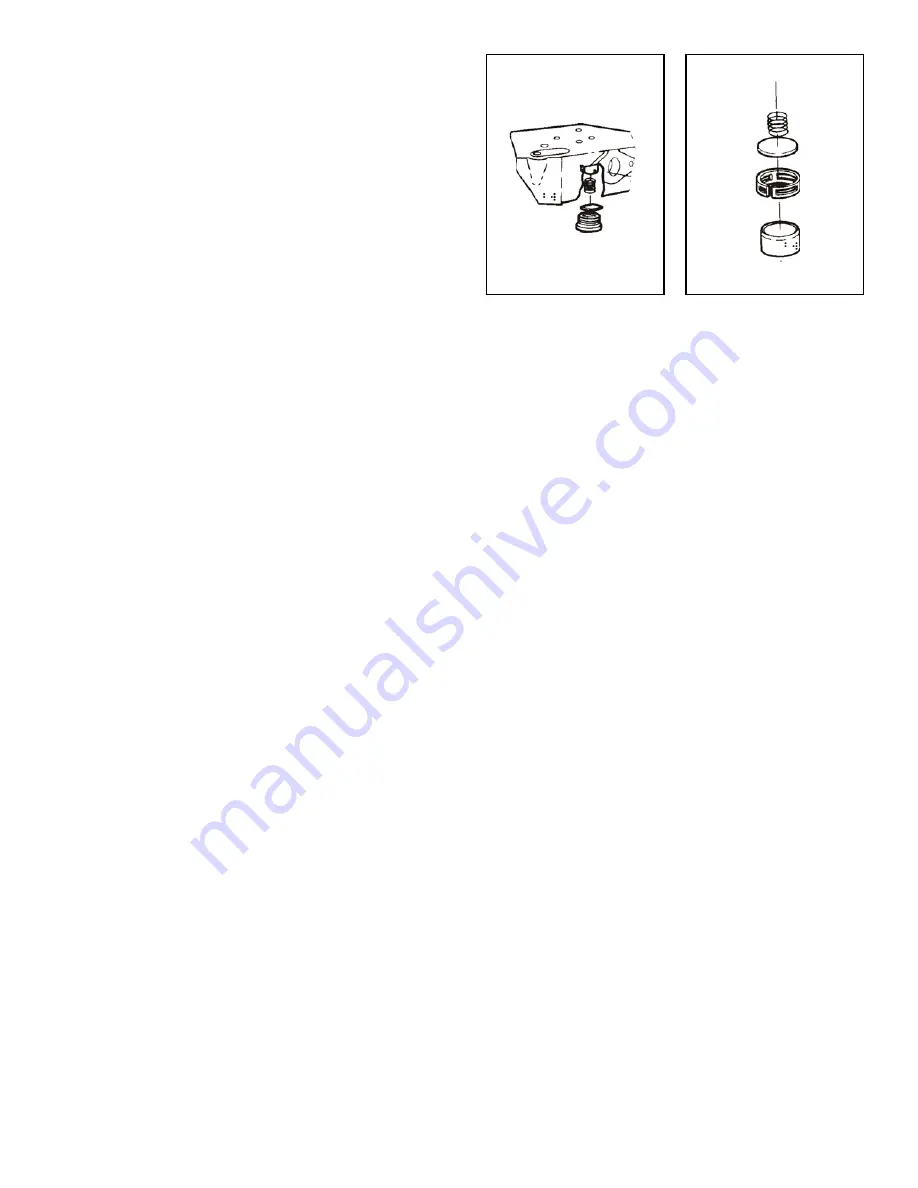
9
Crankshaft
Check the crankshaft threads, keyways, tapered ends and
all machined and ground surfaces for wear, scores, or
damage. Standard crankshaft journals are 1.1250 in. to
1.1242 in. in diameter. If the crankshaft journals are
excessively scored or worn or out of round and cannot be
reground, the crankshaft must be replaced. Connecting
rod bearing inserts are available in .010 in., .020 in. and
.030 in. undersizes for compressors with reground
crankshafts. Main bearing journals must be maintained so
the ball bearings are a snug fit or so that no more than .0065
in. clearance exists between the precision sleeve main
bearing and the main bearing journals on the crankshaft. In
crankshafts fitted with oil seal rings, the oil seal ring groove
or grooves must not be worn. The ring groove walls must
have a good finish and they must be square. Check to be
sure the oil passages are open through the crankshaft.
Connecting Rod Bearings
Used bearing inserts must be replaced. Connecting rod
caps are not interchangeable. The locking slots of the
connecting rod and cap should be positioned adjacent to
each other. Clearance between the connecting journal and
the connecting rod bearing must not be less than .0003 in.
or more than .0021 in. after rebuilding.
REPAIRS
Discharge Valves, Valve Stops and Seats
If the discharge valve seats merely show signs of slight wear,
they can be dressed by using a lapping stone, grinding
compound and grinding tool. If the discharge valve stops
are to be replaced, an application of a sealer is required,
such as “Locktite Retaining Compound #75.” Be sure that
the press fit between the discharge valve stop outside
diameter and the valve stop bore in the cylinder head is a
minimum of .0008 in. and a maximum of .0028 in. If this fit
can not be maintained, a new cylinder head body must be
used. Be sure to completely support the outside top of the
cylinder head casting, while pressing in the replacement
stops. Install the new discharge valve springs and valves.
Screw in the discharge valve seats. Discharge valve travel
should be between .041 in. to .057 in.
To test for leakage by the discharge valves, apply 100 pounds
of air pressure through the cylinder head discharge port
and apply a soap solution to the discharge valves and seats.
A slight leakage in the form of soap bubbles is permissible.
If excessive leakage is found, leave the air pressure applied
and with the use of a fibre or hardwood dowel and a hammer,
tap the discharge valves off their seats several times. This
will help the valves to seat and should reduce the leakage.
With the air pressure still applied at the discharge port of
the cylinder head, check for leakage around the discharge
valve stops exposed on the top of the cylinder head casting.
No leakage is permitted.
Inlet Valves and Seats
Inlet valves and springs should be replaced, if the inlet valve
seats show signs of slight nicks or scratches. They can be
redressed with a fine piece of emery cloth or by lapping with
a lapping stone, grinding compound and grinding tool. If the
seats are damaged to the extent that they cannot be
reclaimed, they must be replaced. The dimension from the
top of the cylinder block to the inlet valve seat should not
exceed .113 in. nor be less than .101 in.
ASSEMBLY
General Note: All torques specified in this manual are
assembly torques and can be expected to fall off after
assembly is accomplished. Do not retorque after initial
assembly torques fall.
To convert inch pounds of torque to foot pounds of torque,
divide inch pounds by 12.
inch pounds
÷
12 = foot pounds
To convert foot pounds of torque to inch pounds of torque,
multiply foot pounds by 12.
foot pounds x 12 = inch pounds
Installing the Crankshaft
Cautionary Note:
All flange mounted compressors must be assembled without
a gasket between the crankcase and flange adapter and
some compressors do not require gaskets on the end cover.
Install the new crankcase gaskets only where they were
removed during disassembly. In service failure of the
compressor will occur if gaskets are used in disregard of
the preceding.
FIGURE 13 - DISCHARGE
VALVE, VALVE STOP AND
SEAT
FIGURE 14 - INLET VALVE
AND SEAT
Содержание TU-FLO 501
Страница 28: ...28 NOTES ...
Страница 35: ...35 ...
Страница 36: ...BW1421 2004 Bendix Commercial Vehicle Systems LLC All rights reserved 9 2004 Printed in U S A 36 ...