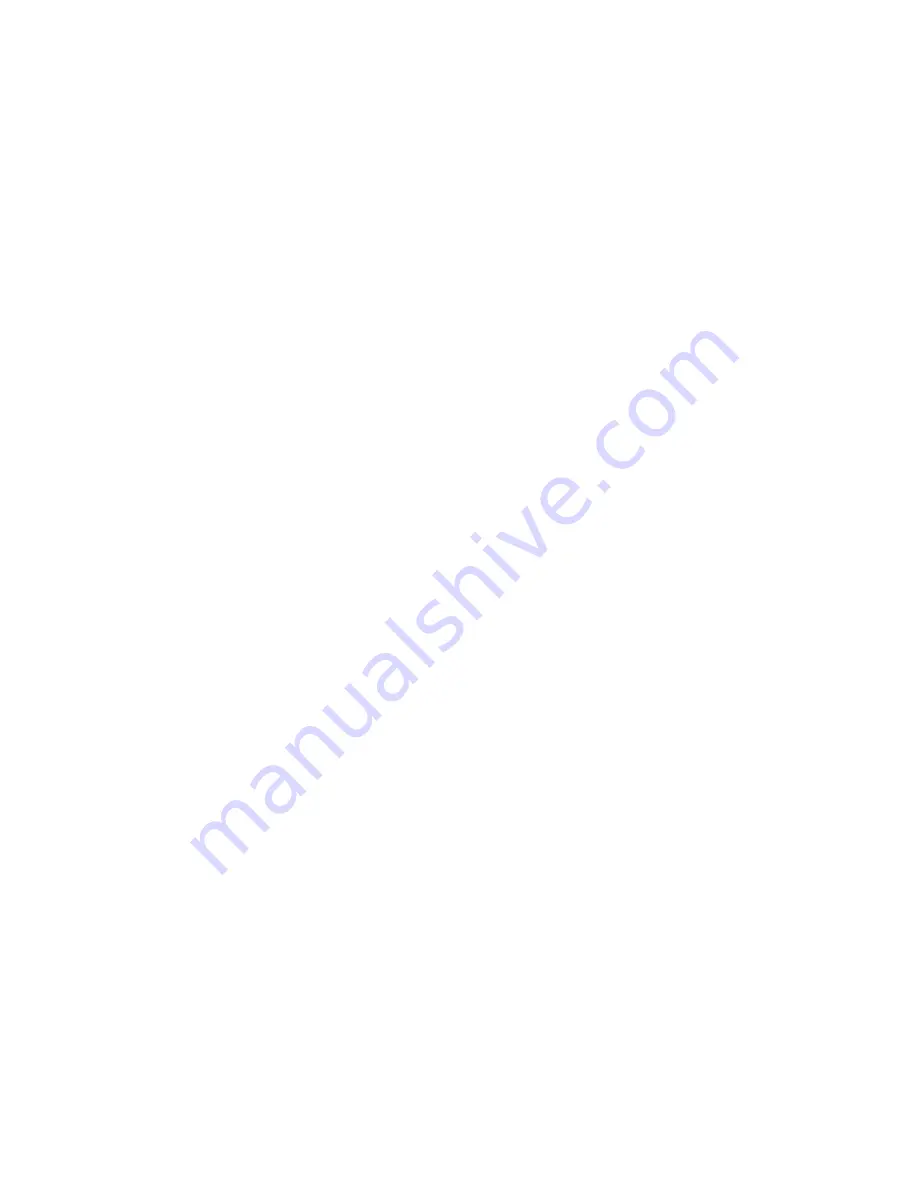
2
PREVENTIVE MAINTENANCE
A. Every month, 8,000 miles, or after 300 operating hours,
depending on type of operation:
1. Check push rod travel and adjust travel at the slack
adjuster if needed. Push rod travel should be as short
as possible without brakes dragging. Excessive push
rod travel reduces braking efficiency, shortens
diaphragm life, gives slow braking response and
wastes air.
2. Check push rod to slack adjuster alignment from
release to full stroke position to be sure push rod
moves out and returns properly without binding at
the cover hole or with other structures. Also check
the angle formed by the slack adjuster arm and push
rod. It should be 90° or greater when the chamber is
in the applied or released positions.
3. Check tightness of mounting nuts. Check cotter pins
to make sure they are in place.
4. Check all hoses and lines. They should be secure
and in good condition.
B. Every year or after each 100,000 miles or 3,600 operating
hours, depending on type of operation.
1. Disassemble and clean all parts.
2. Install new diaphragm or any other parts if they are
worn or deteriorated.
When the diaphragm, spring, or both are replaced they should
be replaced in the corresponding chamber on the same axle.
OPERATING AND LEAKAGE TESTS
A. Operating Test
1. Apply brakes and observe that the push rods move
out promptly and without binding.
2. Release brakes and observe that the push rods return
to the released position promptly and without binding.
3. Check push rod travel. Push rod travel should be as
short as possible without brakes dragging. Adjust
travel of push rod at slack adjuster if necessary.
B. Leakage Test
1. Loosen rubber boot from around push rod hole in
cover. Make and hold a full brake application.
Coat area with soap suds and check for leakage. No leakage
is permissible. If leakage is detected, the diaphragm must
be replaced.
REMOVING
1. Block vehicle wheels.
2. Disconnect line to rotochamber.
3. Remove the yoke pin.
4. Remove the rotochamber.
INSTALLING
1. Before installing chamber, check bracket for distortion,
cracks or any condition which might cause chamber
misalignment or malfunction.
2. Re-install the chamber on the bracket. Tighten the
mounting nuts securely and evenly.
3. Connect the air lines to the rotochamber and check for
leakage.
4. Insert the push rod yoke pin through the hole in the yoke
and slack adjuster. Make sure the same hole location in
the slack adjuster on each side of the axle is used.
5. The yoke should be adjusted on the push rod so that
with brakes released the angle formed by the push rod
and slack adjuster will be greater than 90° and all slack
adjusters should be at the same angle. With properly
adjusted brakes applied, the angle should still be greater
than 90°.
DISASSEMBLY
For ease in disassembly, if the rotochamber has been in
service and shows signs of rust accumulation, it is
recommended that the chamber be immersed and soaked
in the cleaning or rust dissolving solvent for 24 hours.
1. Remove yoke and lock nut from push rod.
2. Remove rubber boot.
3. Remove cap screws from cover.
4. Remove cover, springs and spring guides (if so
equipped).
5. Remove nuts from body. These nuts secure the outer
clamp to the body and are located at the air inlet end of
the rotochamber.
6. Grasp the push rod and by pulling and wiggling the
entire assembly consisting of push rod and plate,
diaphragm guide, diaphragm, inner and outer clamps
should ease out of the body.
7. Straighten the rolled diaphragm.
8. Remove outer diaphragm clamp.
9. Remove nuts from inside of diaphragm guide.
10. Disassemble inner diaphragm clamp, diaphragm and
push plate rod assembly from the diaphragm guide.
CLEANING AND INSPECTION
1. Clean all metal parts in a good cleaning solvent.
2. Carefully inspect all metal parts for cracks, distortion or
damage. Replace any parts not considered serviceable.
3. Replace diaphragm and rubber boot.