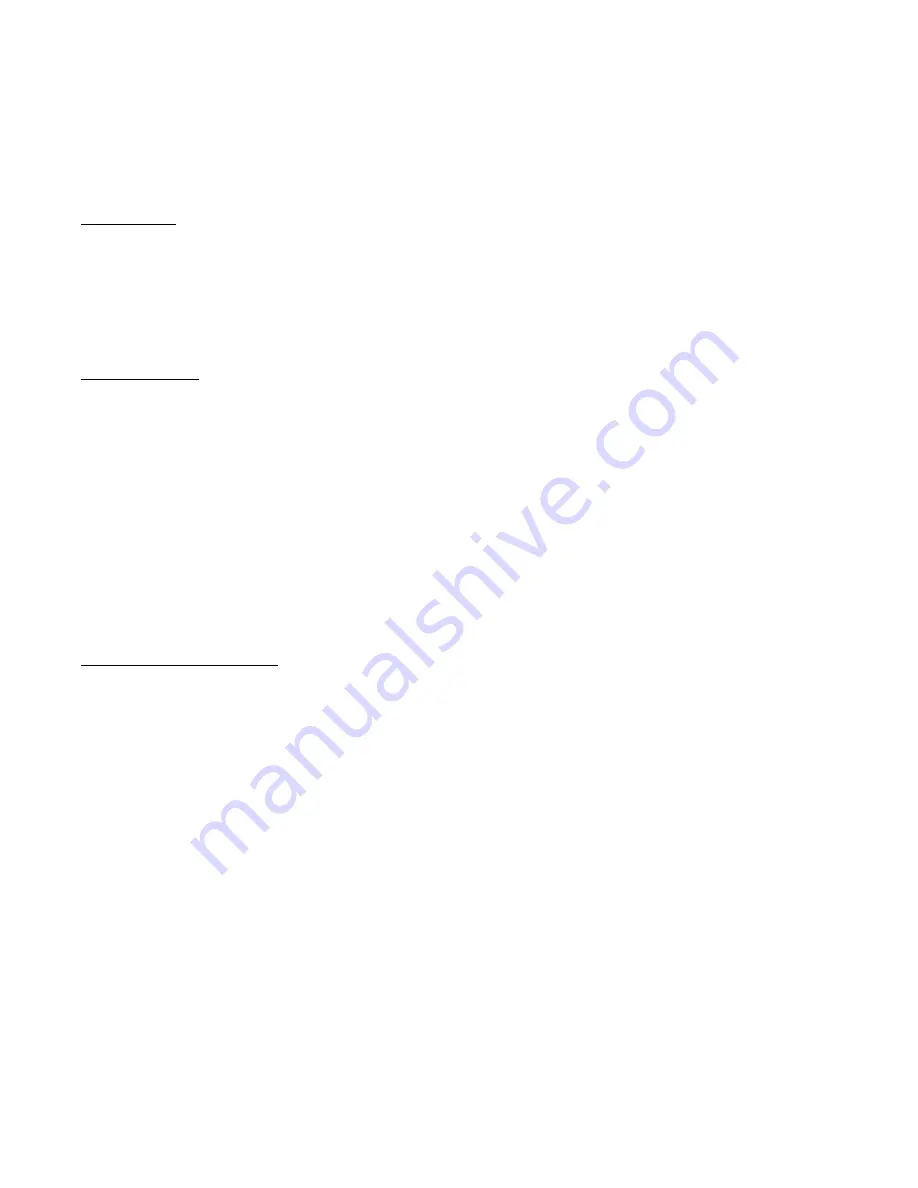
7
modulators. Because the modulators are controlled by the
EC-17
™
controller, the solenoid valves in the appropriate
modulator are opened and closed to gently pump the brake
on the spinning wheel only. This gentle brake application
forces the differential to drive the stationary or slowly spinning
wheel.
Once wheel spin is eliminated, the dash lamp goes out and
the traction system disengages control.
In the event that extended periods of traction operation are
experienced, without vehicle motion being detected, the
ABS traction system will disable traction control to prevent
brake fade. The system will re-enable traction control after
a short period of time.
TRACTION CONTROL AT VEHICLE SPEEDS
ABOVE 25 MPH
If wheel spin occurs at any speed above 25 mph, the
EC-17
™
controller will instantly blink the traction dash lamp
to advise the driver that a wheel spin is occurring.
If the torque limiting feature is programmed in, the EC-17
™
controller uses its link to the engine control module and
sends a signal to reduce engine torque to a level suitable for
the available traction.
NOTE: THE EC-17
™
CONTROLLER WILL NOT SIGNAL THE
ATR
™
VALVE TO APPLY THE BRAKES, EVEN SLIGHTLY,
AT ANY SPEED ABOVE 25 MPH.
ANTILOCK AND TRACTION SYSTEM
OPERATION DURING COMPONENT FAILURE
The Bendix
®
EC-17
™
controller handles equipment failure
using a conservative fail safe philosophy. Any single electrical
failure of a component devoted to antilock or traction control
results in simultaneous illumination of the appropriate
condition lamp on the dash, a disabling of part or all of the
antilock or traction system, and reversion to standard braking
on wheels no longer under EC-17
™
controller control.
Depending upon the type of failure and its position of
occurrence, the EC-17
™
controller disables all or only a
portion of the antilock and traction system. A power or
controller failure, however, will result in complete disabling
of both systems and reversion to standard (non-antilock)
braking is still available on all wheels.
There are a variety of ways to clear diagnostic trouble codes
detected by the system. In most cases, the system will
reset the diagnostic trouble code condition when the source
of the original diagnostic trouble code has returned to a
normal state for a period of time. Isolated diagnostic trouble
codes are able to be reset by the system, but repeated
occurrence (and self-clearing) of some diagnostic trouble
codes will require a manual reset. This is done to aid in the
troubleshooting of intermittent diagnostic trouble codes. The
PC interface (or optional magnetic reset) is used to manually
clear diagnostic trouble codes.
method provides a unique and desirable type of wheel spin
control. Ideally both methods are used to control vehicle
traction. While all EC-17
™
controllers are capable of providing
wheel control antilock and traction control (utilizing both
methods of control), not all systems will be configured for
both methods. Depending upon the vehicle, either or both
traction control methods will be activated during the self
configuration procedure.
Torque Limiting - In order for the torque limiting control feature
to be used, the vehicle must be equipped with an
electronically controlled engine throttle. The torque limiting
feature allows the EC-17
™
controller to reduce engine torque
to a suitable level for the available traction. Torque limiting
helps to minimize the amount (or speed) of wheel spin. It is
especially useful in helping to minimizing a power jackknife
and when all drive wheels are on an equally slippery surface.
Differential Braking - In order for the differential braking control
to be used, the vehicle must be equipped with an antilock
traction relay valve such as the Bendix
®
ATR-1
™
or ATR-2
™
.
Additionally after mid-year 2000 the ECU requires J1922/
J1939 drivers torque request. The ATR-1
™
and ATR-2
™
relay
valves contain a solenoid assembly which provides this
feature. The differential braking feature allows the EC-17
™
controller to gently pump the brake on the spinning wheel.
Since the vehicle's differential tends to drive the wheel that
presents the least resistance (the wheel on the most slippery
surface), a slight brake application to this wheel only, forces
the differential to drive the stationary or slowly spinning wheel.
Differential braking can be activated only when vehicle speed
is under 25 MPH and one drive wheel is spinning faster than
the other(s).
Traction Enable/Disable Switch - The traction control enable/
disable switch allows the operator to engage or disengage
the traction control system as necessary. The switch may
be used to either engage or disengage the traction control
system while the vehicle is in motion. It must be noted
however that while the traction control will disengage while
the vehicle is in motion it will not re-engage (even with the
switch in the engaged position) until the vehicle comes to a
complete stop.
TRACTION CONTROL AT VEHICLE SPEEDS
OF 0 TO 25 MPH
When wheel spin is detected and the vehicle is stopped, or
moving at any speed up to 25 mph, the EC-17
™
controller
simultaneously executes the following operations:
It instantly blinks the traction dash lamp to advise the driver
that a wheel spin is occurring.
If the torque limiting feature is active, the EC-17
™
controller
uses its link to the engine control module and sends a signal
to reduce engine torque to a level suitable for the available
traction.
If the differential braking feature is configured into the system,
the EC-17
™
controller energizes the solenoid in the ATR
valve which then applies air to each of the rear axle