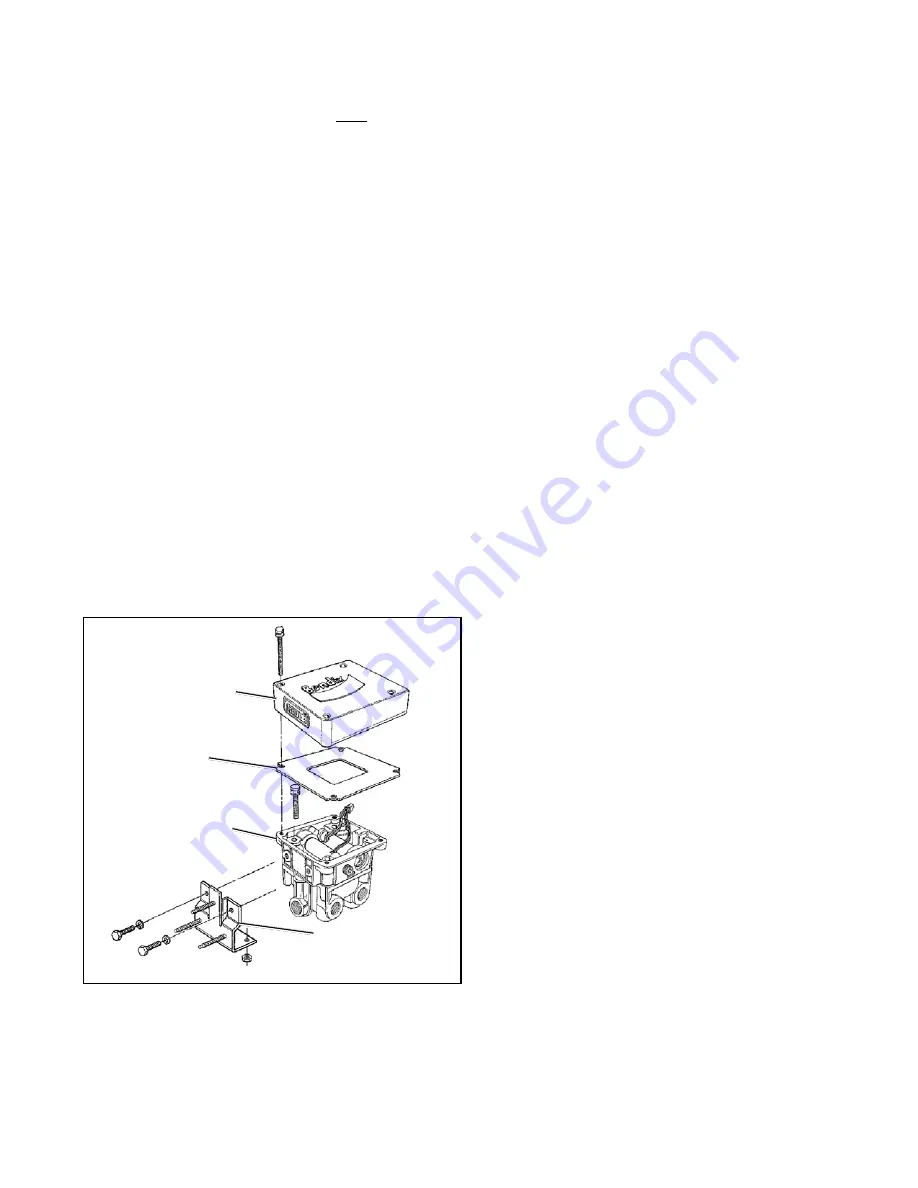
9
4.
If the work is being performed on the vehicle’s air
brake system, or any auxiliary pressurized air
systems, make certain to drain the air pressure from
all reservoirs before beginning ANY work on the
vehicle. If the vehicle is equipped with an AD-IS
™
air dryer system or a dryer reservoir module, be
sure to drain the purge reservoir.
5.
Following the vehicle manufacturer’s
recommended procedures, deactivate the electrical
system in a manner that safely removes all
electrical power from the vehicle.
6.
Never exceed manufacturer’s recommended
pressures.
7.
Never connect or disconnect a hose or line
containing pressure; it may whip. Never remove a
component or plug unless you are certain all
system pressure has been depleted.
8.
Use only genuine Bendix
®
replacement parts,
components and kits. Replacement hardware,
tubing, hose, fittings, etc. must be of equivalent
size, type and strength as original equipment and
be designed specifically for such applications and
systems.
9.
Components with stripped threads or damaged
parts should be replaced rather than repaired. Do
not attempt repairs requiring machining or welding
unless specifically stated and approved by the
vehicle and component manufacturer.
10. Prior to returning the vehicle to service, make
certain all components and systems are restored
to their proper operating condition.
REMOVING EC-14
™
CONTROLLER ASSEMBLY
Locate the EC-14
™
controller on the trailer and determine if
it is mounted on a modulator (e.g. M-12
™
modulator) or is
remote mounted to a trailer frame member using a bracket.
Use the appropriate removal procedure below.
Removing the EC-14
™
Controller and M-12
™
Modulator:
1. Identify and remove all air lines connected to the
M-12
™
modulator.
2. Disconnect the electrical connector from the EC-14
™
controller.
3. Note and mark the mounting position of the MC-14
™
modulator-controller assembly on the vehicle. Loosen,
remove and save the nuts on the mounting hardware
that attaches the MC-14
™
modulator controller bracket
to the vehicle. Remove the MC-14
™
modulator controller
assembly from the vehicle.
4. Remove as much contamination as possible from the
exterior of the assembly making sure to keep the
contamination away from the open ports.
5. Note and mark the position of the EC-14
™
controller
relative to the M-12
™
modulator. Remove and retain the
four hex cap screws that secure the EC-14
™
controller
to the M-12
™
modulator. Carefully separate the EC-14
™
controller from the M-12
™
modulator enough to expose
the wire harness that connects both units electrically.
Disconnect the wire harness by separating the four pin
connector at the EC-14
™
controller. Peel the gasket from
the EC-14
™
controller or M-12
™
modulator and retain for
reuse. Note: Use a new gasket if damaged during
removal or if a new gasket is immediately available.
INSTALLING THE EC-14
™
CONTROLLER
ASSEMBLY
1. After noting the positioning marks made prior to
disassembly, reconnect the M-12
™
modulator wire
harness to the EC-14
™
controller, position the gasket
on the EC-14
™
controller then secure the EC-14
™
controller to the M-12
™
modulator using the four cap
screws. Torque the cap screws to 50-80 Ibs. in.
2. Mount the assembled MC-14
™
modulator controller on
the vehicle and orient it in the position marked prior to
removal.
3. Reconnect all air lines.
4. Reconnect the electrical connector to the EC-14
™
controller.
5. Test the MC-14
™
modulator controller for operation and
air leakage prior to placing the vehicle in service.
6. Perform the “Initial Start up Procedure” in the
Troubleshooting section to assure proper antilock
system operation.
DIAGNOSING AND LOCATING A SYSTEM
PROBLEM
GENERAL
The EC-14
™
controller contains self test and diagnostic
circuitry that continuously checks for proper operation of
FIGURE 7 - MC-14
™
MODULATOR CONTROLLER
EC-14
™
CONTROLLER
GASKET
MOUNTING
BRACKET
M-12
™
MODULATOR
Содержание EC-14 ANTILOCK CONTROLLER
Страница 2: ...2 FIGURE 2 MC 14 ANTILOCK BRAKE SYSTEM...
Страница 8: ...8 FIGURE 6 MC 14 ANTILOCK WIRING SCHEMATIC...