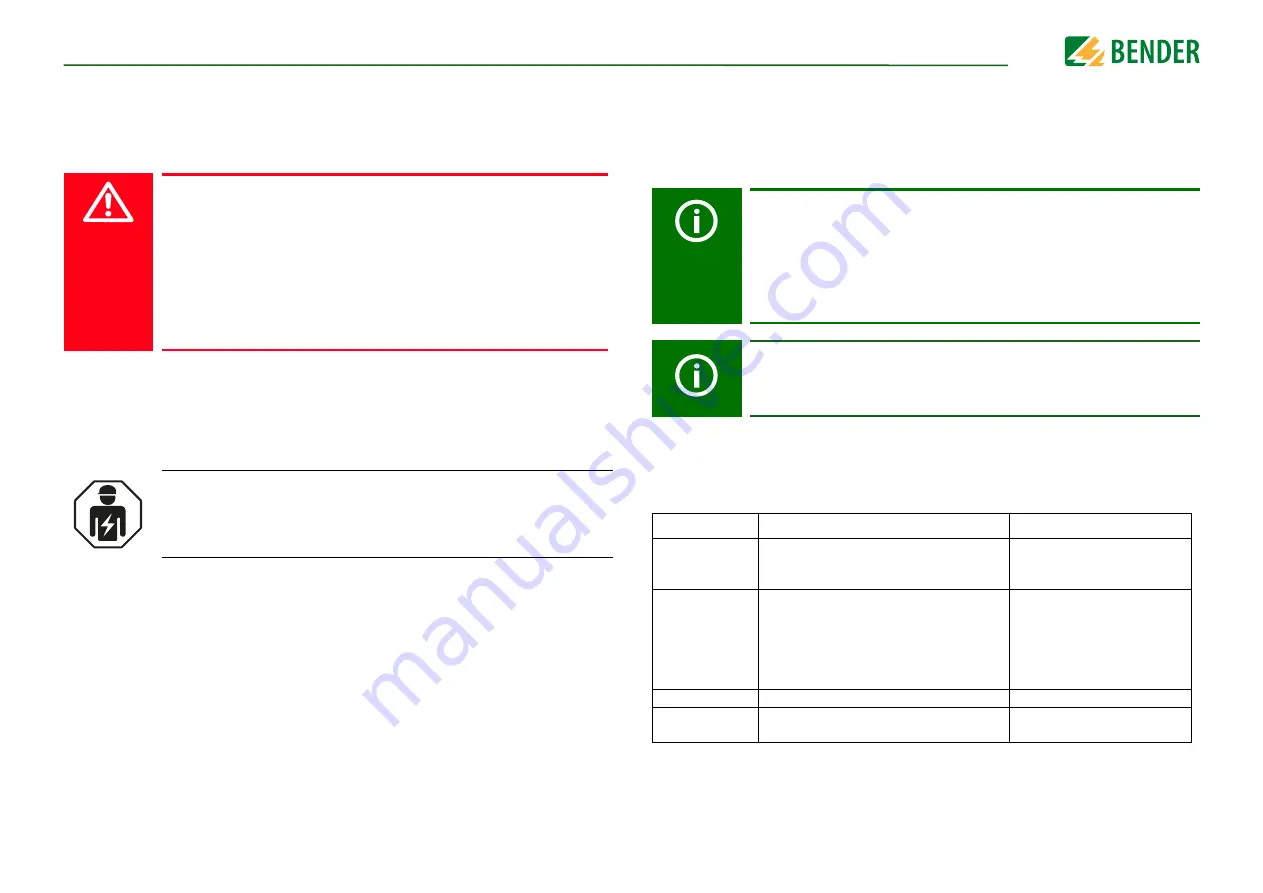
iso165C_D00154_03_M_XXEN/01.2019
7
Safety information
2. Safety information
2.1 General safety instructions
Part of the device documentation in addition to this manual is the enclosed "Safety in-
structions for Bender products".
If the device is used outside the Federal Republic of Germany, the applicable local stand-
ards and regulations must be complied with. The European standard EN 50110 can be
used as a guide.
2.2 Intended use
The ISOMETER® iso165C and ISOMETER® iso165C-1 monitor the high-voltage (HV) insula-
tion resistance between the car chassis and the active HV components of an unearthed
DC drive system (IT system) in electric vehicles with supply voltages of DC 0 V...600 V. The
insulation condition is monitored on the DC side as well as on the AC motor side of the
electrical drive system. Existing insulation faults will be reliably signaled even under high
system interferences, which can be caused by motor control processes, acceleration or
energy recovery for example.
Both ISOMETER®s feature a CAN bus interface and can be easily integrated into an exist-
ing CAN environment in hybrid or fully electric vehicles.
DANGER
Risk of electrocution due to electric shock!
Touching live parts of the system carries the risk of:
• An electric shock
• Damage to the electrical installation
• Destruction of the device
Before installing and connecting the device, make sure that the installa-
tion has been de-energised. Observe the rules for working on electrical in-
stallations.
Only skilled persons are permitted to carry out the work necessary to install,
commission and run a device or system.
Ensure the correct rated input voltage and supply voltage is applied. For insulation or
voltage tests, the ISOMETER® must be separated from the IT system for the duration of the
test. To check that the device has been properly connected, perform a functional test be-
fore commissioning the system. It is necessary to examine whether the initial settings
meet the requirements of the IT system.
2.2.1 ISOMETER® iso165C and ISOMETER® iso165C-1 comparison
While the ISOMETER® iso165C and ISOMETER® iso165C-1 are similiar in many aspects (re-
fer to the features list on
) the main differences between the two are shown in the
table below:
With reference to the general application of an IMD in IT systems, only one
active IMD in a galvanically interconnected system is permitted. If IT sys-
tems are to be interconnected via a coupling switch, it must be ensured via
a supervisory unit that all other IMDs are separated from the IT system and
switched to inactive. IT systems coupled via capacitors or diodes can also
influence the insulation monitoring system. For this reason, central control
of the various IMDs must be implemented.
In the event of an ISOMETER® alarm message, the insulation fault should
be eliminated as quickly as possible.
Feature
iso165C
iso165C-1
Contains an out-
put driver
No
Yes. Error and Warning signals
are available on the separated
high-side driver
Coupling relays at
power on
The HV coupling relays of the HV1 voltage
path are, by default, open and therefore no
valid voltage and insulation resistance mea-
surements are possible until these relays are
closed, which must be carried out using an
external command
The HV coupling relays of the
HV1 voltage path are automati-
cally closed at power on
Baud rate
250 kBaud
500 kBaud
Terminating resis-
tance
124 Ω
internally
None