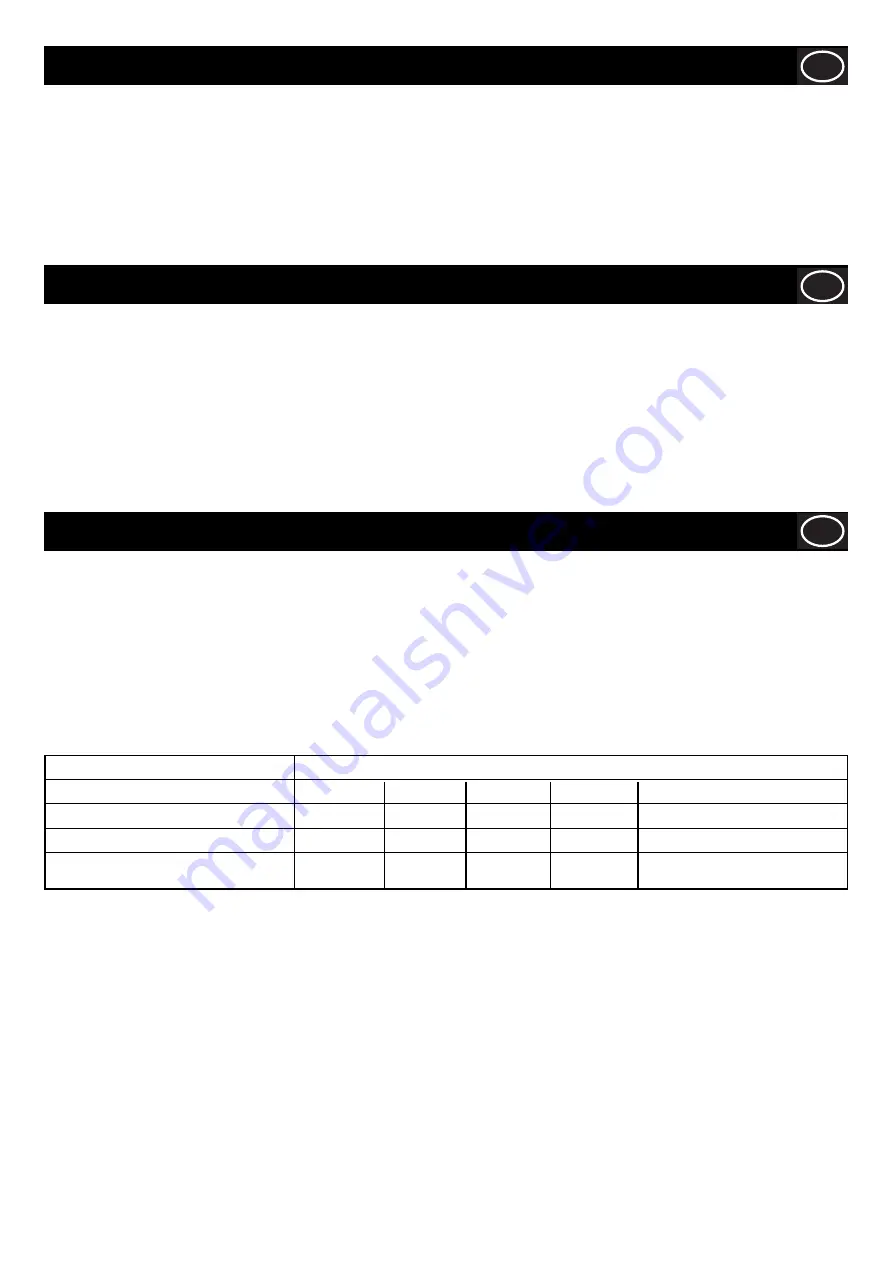
11
Pre start-up inspection
The following Pre-start-up inspection must be performed before the start of each work session or after every four hours of use,
whichever is fi rst. Please refer to the service section for detailed guidance. If any fault is discovered, the compactor must not be used
until the fault is rectifi ed.
1. Thoroughly inspect the compactor for signs of damage. Check componenents are present and secure. Pay special attention
to the belt drive safety guard fi tted between the engine and the vibrator unit.
2. Check the engine oil level and top up as necessary.
3. Check the engine fuel level and top up as necessary.
4. Check for fuel and oil leaks.
Pre-Start Checks
GB
Reasons For Compaction
Soil, which has been disturbed or new infi ll, subbase and blacktop, will have small voids or air pockets which, if not compacted, will
lead to one or more problems occurring.
1. As traffi c crosses the surface of an uncompacted area, the material is compressed. This leads to subsidence of the top
surface as the material fi lls the voids.
2. A similar situation occurs with static loads on uncompacted ground. The load (e.g. a building) will sink.
3. Materials with voids are more susceptible to water seepage, leading to erosion. Water ingress may also cause the soil
to expand during freezing temperatures and contract during dry spells. Expansion and contraction is a major cause of
damage to building foundations and normally leads to the structure requiring underpinning.
Compaction increases the density of the material and therefore increases its load bearing capacity. Reduces air voids
and therefore reduces the risk of subsidence, expansion and contraction, due to ingress of water.
GB
Applications
Applications/materials fall into three categories:
1. Cohesive materials (less than 20% granular) e.g clay, silt & heavy soils.
2. Granular materials (more than 20% granular) e.g hard core, sand & light soils.
3. Bituminous materials e.g asphalt (tarmac), cold lay (bitumin emulsion products).
The chart shows the HAUC specifi cations for layer depth and number of passes for Dual Force’ plates. If standard machines are used,
optimum compaction can not be guaranteed, however, if layer depths are reduced and number of passes increased, results can be
improved.
Moisture content of cohesive & granular materials is critical to effective compaction. If granular material is too dry it will fl ow around the
plate instead of compacting. If the moisture content is too high the material may dry out after compaction and shrinkage will occur.
GB
1400 -1800 kg/m2
COMPACTION PASSESS REQUIRED PER LAYER OF COMPACTED THICKNESS UP TO.
40MM
60MM
80MM
100MM
150MM
Cohesive Materials
**
2** 4** 5** 6** Reduce
Layer
Thickness
Granular Materials
2*
3*
4*
5
9
Bituminous
6
10
12
Reduce
Layer
Thickness
* Usually placed in 100mm minimum layer so not specifi ed by HAUC.
** The nature of cohesive materials makes plate compaction diffi cult. Optimum compaction is not guaranteed and not
recommended by HAUC.