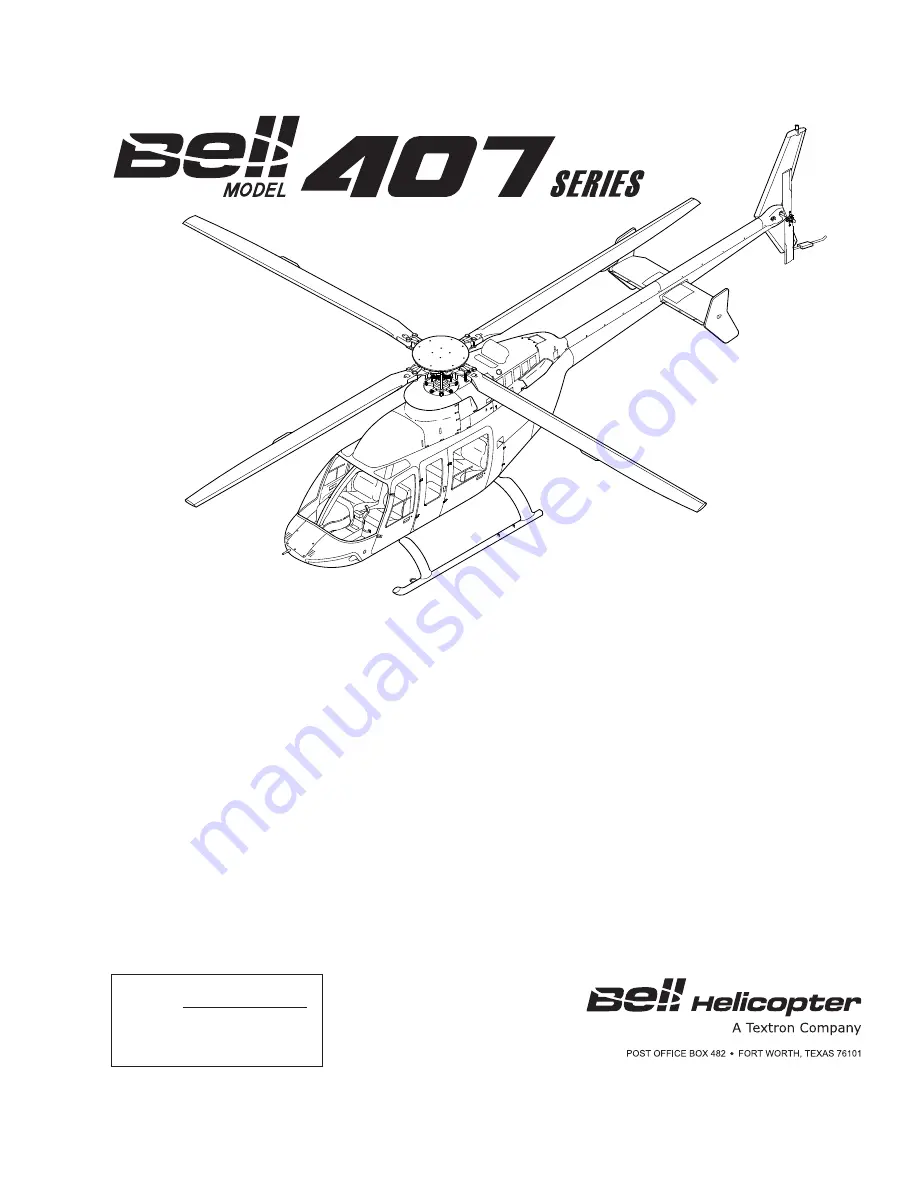
BHT-407-MM-1
NOTICE
The instructions set forth in this manual, as supplemented or modified by Alert Service Bulletins (ASB) or
other directions issued by Bell Helicopter Textron Inc. and Airworthiness Directives (AD) issued by the
applicable regulatory agencies, shall be strictly followed.
Export Classification C, ECCN EAR99
22 FEBRUARY 1996
REVISION 47 — 2 MAY 2019
COPYRIGHT NOTICE
COPYRIGHT
201
BELL ® HELICOPTER TEXTRON INC.
AND BELL HELICOPTER TEXTRON
CANADA LTD.
ALL RIGHTS RESERVED
MAINTENANCE MANUAL
VOLUME 1
GENERAL INFORMATION