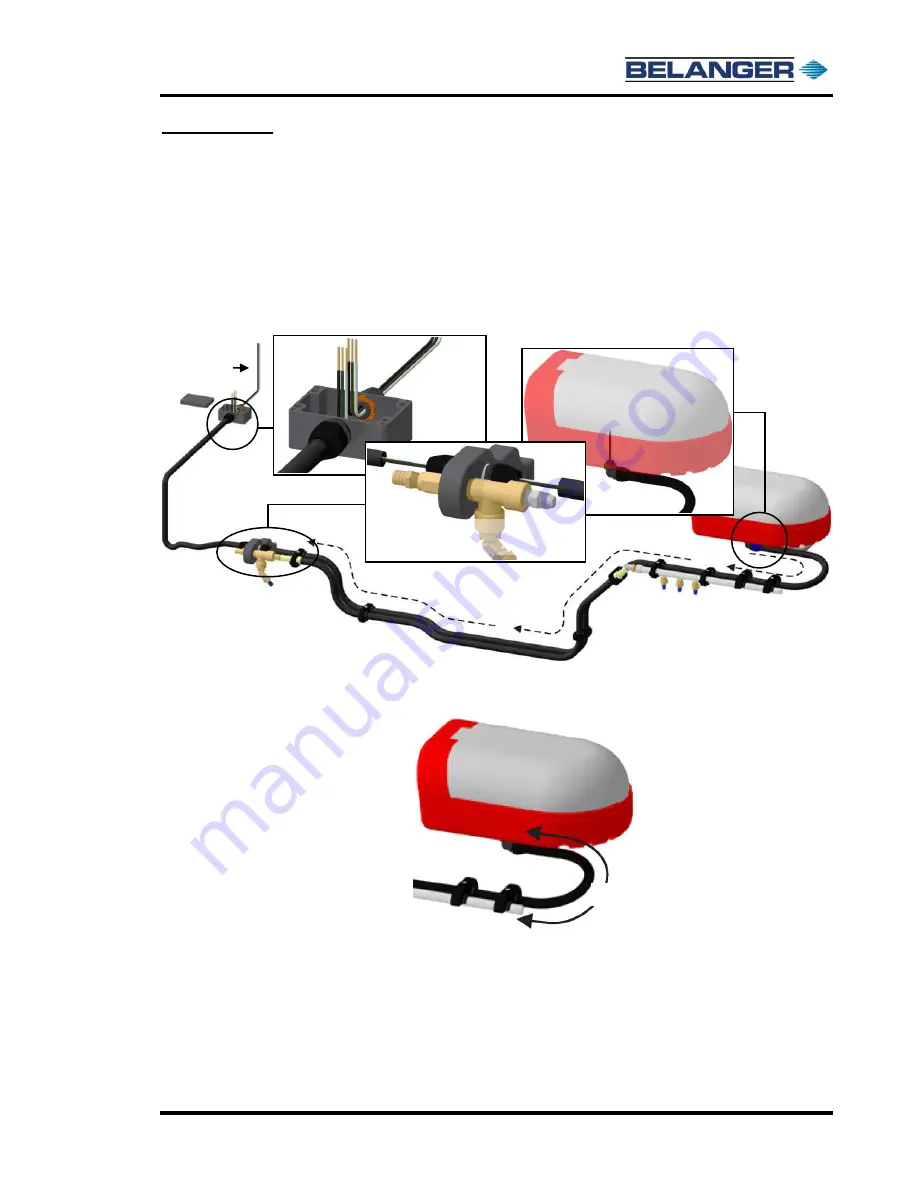
QUICKFIRE®
Signature
®
Series
1MANUL826
Belanger, Inc. * PO BOX 5470 * Northville, MI 48167-5470 * Ph (248) 349-7010 * Fax (248) 380-9681
51
Installation
Utility Connections for Side Wheels: Electric
Water Feeds
1) Unwrap the hose from around the Head Assembly, run it through the split grommets as
shown below, and follow the shown path all the way to the junction box atop the leg
assembly.
Do not tighten the clamps together until the conduit has been adjusted.
2) From the MCC system panel, (see wiring schematics) drop the wiring 208-230VAC to
the electrical boxes on the top of the two QuickFire wrap legs you installed.
3) Confirm that there is
20” of conduit at the area shown below and tighten all of the clamp
fasteners. Tighten all cord grips.
4) When feeding wiring through cord grip in electrical boxes, use wire nuts and electrical
tape to terminate wiring (see wiring schematics located in MCC panel).
1. From motor, down
through conduit
2. From one conduit, through
fittings and through 2
nd
conduit
3. Use wire-
nuts to
connect to
main power
Main power
from drop
20”
Содержание QuickFire Wrap Around Signature Series
Страница 1: ...QuickFire Wrap Around Signature Series QuickFire Wrap Around Signature Series 1MANUAL826 Rev03 ...
Страница 2: ......
Страница 4: ......
Страница 105: ......
Страница 106: ......