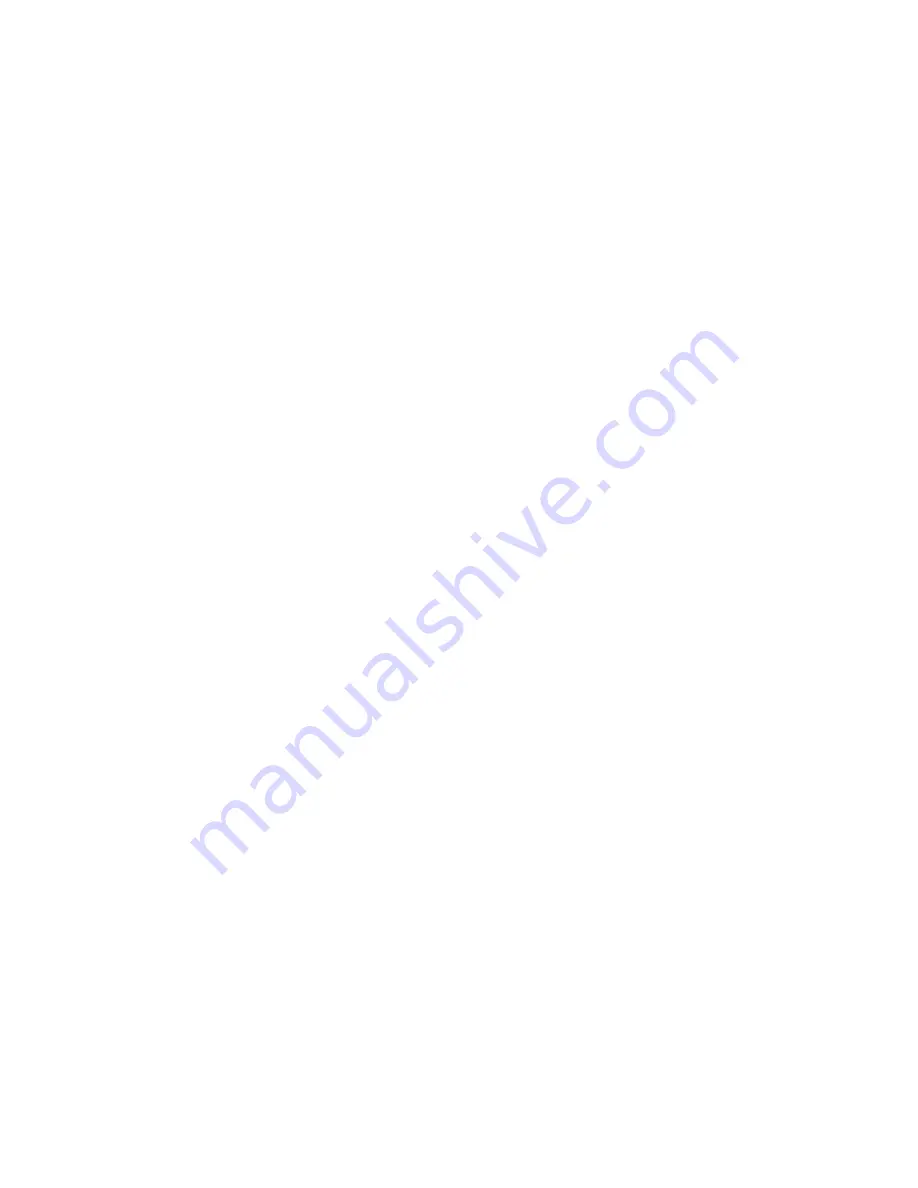
Safety İnstructions
Ø
Be sure that electrical connection is made carefully. To avoid unwanted situations like electrical shock, protect the main supply cable with a holster.
Ø
Before running the machine, be sure that all of the protections are mounted properly and all the covers are closed.
Ø
Avoid from smoke and moisture.
Ø
Please use the parts and equipments which are recommended. Usage of unsuitable parts and materials which arebigger than the capacity of the machine can cause unwanted situations.
Ø
Check the machine and inform the defects everyday.
Ø
Don’t leave any material after chancing the band.
Ø
Do not hold the material while the machine is cutting. Always tighten the material by using essential parts.
Ø
Please pay attention to choose the area of the machine which doesn’t include anything that creates difficulties to control the machine
Ø
Please be sure that the teeth of the band are looking to correct direction.
·
Don’t leave the band on the ground or any place that is dangerous for other people.
·
Be careful when using the machine and keep the working area clean ( clean the saw dusts and oil traces )
·
Pay attention to security instructions when using the machine.
·
Don’t wear loose cloths when using the machine.
·
Regardless use the protective gloves when using the machine.
·
Don’t get close too much to the machine when running.
·
Before carrying out any cleaning or maintenance procedure, disconnect the machine from main supply.
·
İn some conditions, noise level can be about 85 db. Band choice and cutting speed is important factor for noise level.
·
İllumination is an important factor for security.
·
Ratio of coolant liquid is important for obtaining optimum lubrication.
·
Never use the machine if you notice any fault of the machine or absence of any part of the machine.
-
Control the emergency button at least once a week and be sure that it is working properly.
Содержание BMSO 325C
Страница 1: ......
Страница 18: ......
Страница 19: ......
Страница 20: ......
Страница 31: ......
Страница 32: ......
Страница 33: ......
Страница 34: ......
Страница 35: ......
Страница 36: ......
Страница 37: ......
Страница 38: ......
Страница 39: ......
Страница 40: ......
Страница 41: ......
Страница 42: ......
Страница 43: ......
Страница 44: ......